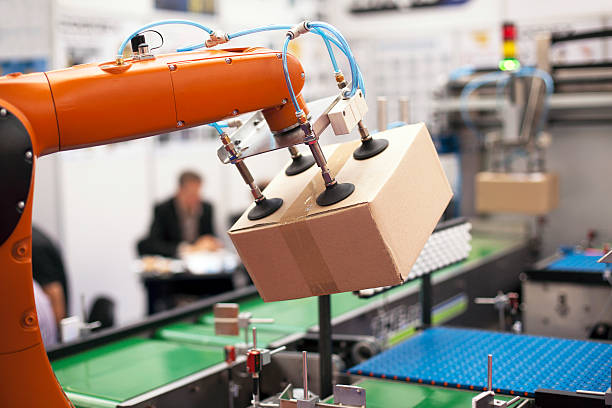
The Impact of Automation Equipment
Packaging automation equipment has emerged as a transformative force, reshaping industries and redefining efficiency. The integration of cutting-edge technologies into packaging processes has not only increased productivity but has also led to significant improvements in quality, cost-effectiveness, and sustainability. In this blog, we'll explore the game-changing advancements in packaging automation equipment that have revolutionized the industry.
Case Erectors and Sealers:
Case erectors automatically form and set up corrugated cases or boxes for packaging. They streamline the process of preparing containers for products. Case sealers, on the other hand, automate the sealing of filled cases, ensuring a secure and uniform closure.
Robotics and Pick-and-Place Systems:
These automated systems, including cartoning machines, excel at tasks that demand precision and speed, significantly reducing the margin of error compared to manual labor. They are adept at handling various packaging elements, from placing products in containers to accurately sealing and labeling them. This not only enhances the overall efficiency of the packaging process but also minimizes the risk of damage or inconsistencies in the final product.
Weighing and Filling Systems:
Weighing and filling systems automate the precise measurement and dispensing of products into packaging containers. These systems are crucial for industries that require accurate filling of products, such as food, pharmaceuticals, and chemicals. Automated weighing and filling contribute to consistency in product quantity, reduce waste, and improve overall production efficiency.
Advanced Conveyor Systems:
Conveyor systems have long been a staple in packaging lines, but recent advancements have taken them to new heights. Modern conveyor systems are equipped with intelligent sensors and controls, allowing for seamless integration with other equipment. These systems optimize the flow of products throughout the packaging line, preventing bottlenecks and ensuring a continuous, streamlined operation. Adjustable speeds, automated diverters, and sorting mechanisms contribute to improved efficiency and flexibility in handling diverse packaging requirements.
Vision Inspection Systems:
Ensuring the quality of packaged goods is paramount, and vision inspection systems have become indispensable in achieving this goal. These systems utilize advanced cameras and sensors to meticulously examine products for defects, ensuring that only items meeting the specified quality standards proceed down the packaging line. This not only enhances the overall product quality but also reduces the likelihood of recalls and associated costs.
Automated Palletizing Systems:
Traditionally a labor-intensive task, palletization has undergone a transformation with the introduction of automated systems. These systems use robotic arms and intelligent algorithms to arrange products on pallets with unmatched speed and precision. Automated palletizing not only reduces the physical strain on workers but also minimizes the risk of errors associated with manual handling, resulting in consistent and optimized pallet loads.
Stretch Wrapping Machines:
Stretch wrapping machines automate the process of securing palletized loads with stretch film. These machines use rotating arms or turntables to apply stretch film tightly around the pallet, ensuring stability during transit and storage. Automated stretch wrapping enhances the speed and reliability of the palletizing process while minimizing film waste and providing a secure wrap for products.
Labeling Systems:
Automated labeling systems apply labels to products or packaging containers with precision and speed. These systems can handle various label types, including pressure-sensitive labels, shrink sleeves, and RFID tags. Automated labeling contributes to the professional appearance of products, ensures accurate information, and supports compliance with labeling regulations.