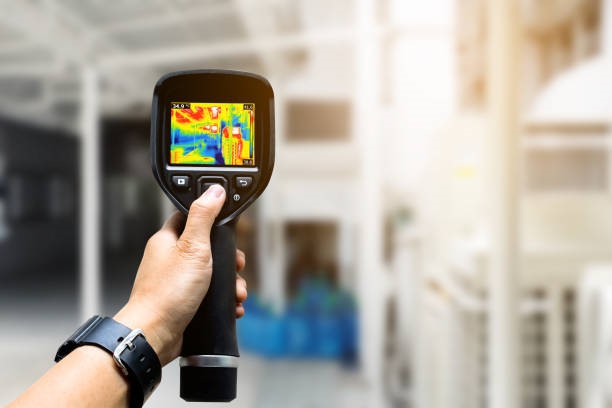
Technologies such as thermal imaging are becoming indispensable tools for ensuring product integrity. Among the myriad applications of thermal imaging, the inspection of packaging materials is one that has exceptionally been enhanced with this technology.
A faulty seal can mean a spoiled meal, a damaged product, or even a safety hazard. Thermal imaging inspection provides a powerful tool to ensure your packages are sealed tight.
What is Thermal Imaging Inspection?
Unlike traditional inspection methods that rely on visual cues, thermal imaging uses infrared cameras to detect variations in heat signatures. Since the sealing process often involves heat, thermal cameras can reveal anomalies in the seal that might be invisible to the naked eye.
Applications in Packaging
In manufacturing, it can detect defects such as weak and incomplete seals, wrinkles, or foreign particles that may compromise the integrity of the packaging.
Food Packaging: Thermal imaging inspection helps detect anomalies such as leaks or foreign contaminants in packaging materials. By identifying temperature variations, it can pinpoint areas of concern that might compromise the quality and safety of the packaged food.
Pharmaceutical Packaging: Thermal imaging can be employed to monitor temperature-sensitive medications throughout the packaging process. It helps identify hot spots or cold spots in the packaging, ensuring that the products are adequately protected from temperature fluctuations.
Electronic Packaging: Thermal imaging helps detect overheating or thermal runaway in packaged electronic devices, which could lead to malfunctions or even safety hazards.
Benefits of Thermal Imaging
- Enhanced Quality Control: Thermal imaging provides non-destructive, real-time inspection of packaging materials.
- Cost Efficiency: By preventing defects early in the packaging process, manufacturers can reduce the likelihood of costly product recalls or rework.
- Ensuring Compliance: Thermal imaging inspection helps companies comply with regulatory standards and industry requirements regarding packaging integrity and safety.
- Process Optimization: By identifying areas for improvement in the packaging process, thermal imaging enables manufacturers to optimize their processes for efficiency and consistency.
- Reduced Waste: By catching seal defects early in the production process, thermal imaging helps minimize product waste and associated costs.
Use Cases of Thermal Imaging in Packaging
- Heat-sealed bags and pouches
- Blister packs
- Rigid containers
- Bottles and cans
- Medical device packaging
Factors that impact Thermal Imaging
Material Properties: Some packaging materials, particularly those with metal films, can be reflective and not ideal for thermal imaging.
Placement of Camera: For optimal results, the thermal camera should be positioned to capture the heat signature immediately after the sealing process.
Data Analysis: Thermal imaging systems often come with software that analyzes the heat signature data and identifies potential defects.