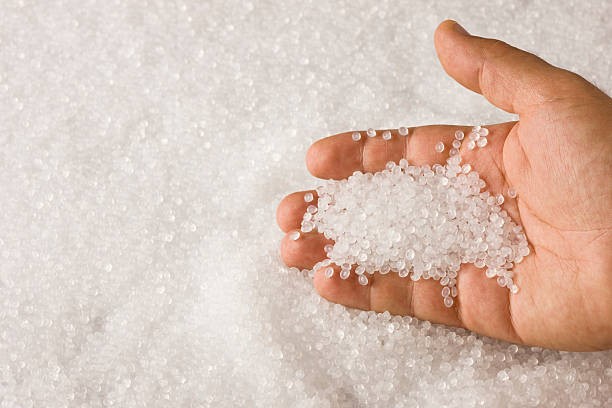
thermoplastic, addition polymers made from propylene monomers, polypropylene was first polymerized in 1951 by petroleum scientists Paul Hogan and Robert Banks who worked at Phillips. The success of the polymerization process was confirmed by Italian and German scientists Natta and Rehn through repetition. Since its inception, it was quickly put into commercial production, less than three years after second trials by Natta, and gained popularity rapidly.
FEATURES AND APPLICATION
- SLIPPERY SURFACE: Polypropylene has a relatively slippery surface and is used in low friction applications such as gears.
- BONDING PROPERTIES: It is relatively hard to bond PP to other surfaces and it does not adhere well to certain glues.
- LOW DENSITY: PP is a weight saving choice for manufacturers.
- CHEMICAL RESISTANCE: It has exceptional chemical resistance to organic solvents like fats at room temperature. However, it is likely to oxidize at high temperatures, which can be concerning during the process of injection molding. Diluted bases and acids don’t react readily with polypropylene. This property makes PP a good choice for containers of cleaning agents, first-aid products, and similar liquid products.
- LOAD BEARING: Polypropylene is not useful for structural applications and thus are applied to non-load bearing functions such as lidding of ketchup and shampoo bottles.
- COPOLYMERIZATION: PP can be easily copolymerized into a composite plastic with other polymers like polyethylene creating plastics favored for more robust engineering applications.
- INSULATION: Polypropylene has a very high resistance to electricity
- LIVING HINGE: Polypropylene can be manufactures into extremely thin pieces of plastic that bend without breaking.
- Polypropylene also has the ability to function as a fiber.
It is used in a variety of applications including packaging for consumer products and plastic parts for various industries including the automotive industry.
RECYCLING OF POLYPROPYLENE
While PP is easily among the most popular plastic packaging materials in the world, only around 1% is recycled, which means most PP is headed for the landfill.
This is primarily due to inconsistencies in the sorting step; PP is virtually nonexistent as a food-grade recycled material because of the inability to separate food-grade PP from nonfood-grade PP.
Currently, the ability to identify what the product once contained has been a nearly impossible task.
Collaborations and consortiums such as Nextloopp aim to solve this problem and mass-generate circular food-grade recycled polypropylene from post-consumer packaging.
They aim to do so by developing the required infrastructure for the recycling process