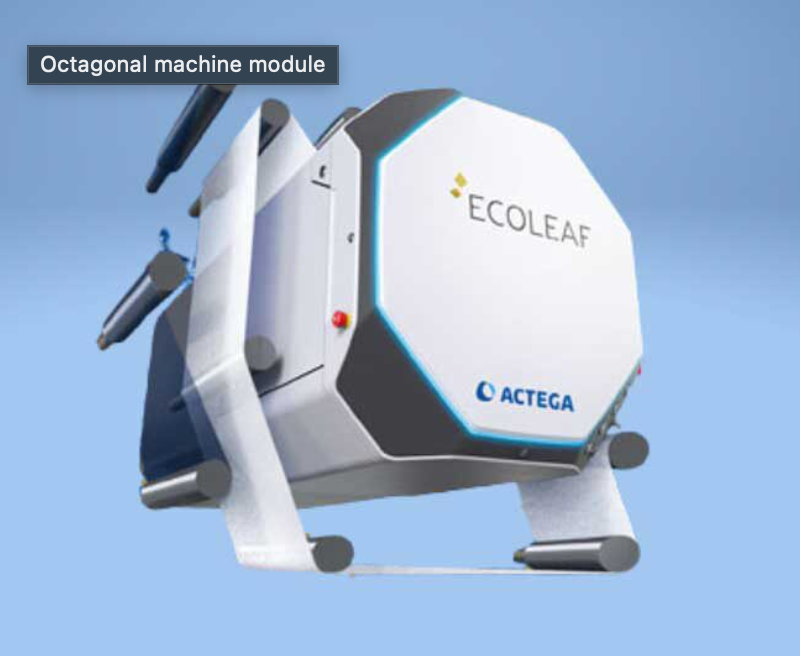
Highly finished packaging and labels have long been known to captivate consumers at the point of sale. Techniques like embossing, special color effects, contrasting matte and gloss finishes, and metallic sheens are particularly effective in catching the eye. Traditional metallisation processes, however, often rely on plastic-coated films, posing environmental challenges. Enter Ecoleaf, a sustainable alternative revolutionizing the industry.
Conventional methods of finishing prints with embossing foil involve using pressure and heat to apply metallic shapes to labels and folded boxes. This process leaves behind plastic film waste. Ecoleaf’s innovative metallisation process, however, transfers metallic pigments precisely where needed, utilizing all metal particles efficiently. Instead of plastic-coated backing films, Ecoleaf employs a 'liquid film,' significantly reducing waste and the environmental impact associated with plastic production and disposal. Despite its sustainable approach, the process maintains the high aesthetic and quality standards demanded by brand owners. Transitioning from traditional hot- or cold-foil embossing to Ecoleaf technology enables the creation of eye-catching metallic embellishments with an improved environmental profile.
"Many companies across Europe are already taking advantage of the benefits that Ecoleaf offers at their digital-, screen- or flexographic-printing production lines. This technology has the potential to transform the industry," says Timo Kondziela, Head of Global Marketing at Actega.
Ecoleaf’s versatility is a key advantage. Compatible with various printing methods, it allows a wide array of metallic finishing options. Tactile metallic effects can be achieved in rotary or flatbed screen printing without embossing. Fine metallisations at high resolutions are possible in flexographic printing, and seamless, variable metallisations can be created in inkjet printing.
The Ecoleaf module can be installed at the start, middle, or end of the printing process, or even as an off-line option. The technology works by using a printed 'trigger image' onto which a metallisation unit transfers an ultra-thin layer of metallic pigments via a dispenser roller. This process enables the realization of diverse metallic effects.
Initially designed for use with narrow web presses and label production, the first Ecoleaf LA430 module is already making waves. Future plans include launching metallisation units for folded boxes and flexible packaging. The innovative Ecoleaf process has garnered significant recognition, winning the German Design Award for outstanding design quality in the Excellent Product Design category for the industrial sector.
Ecoleaf stands poised to transform sustainable packaging, combining environmental responsibility with exceptional design.