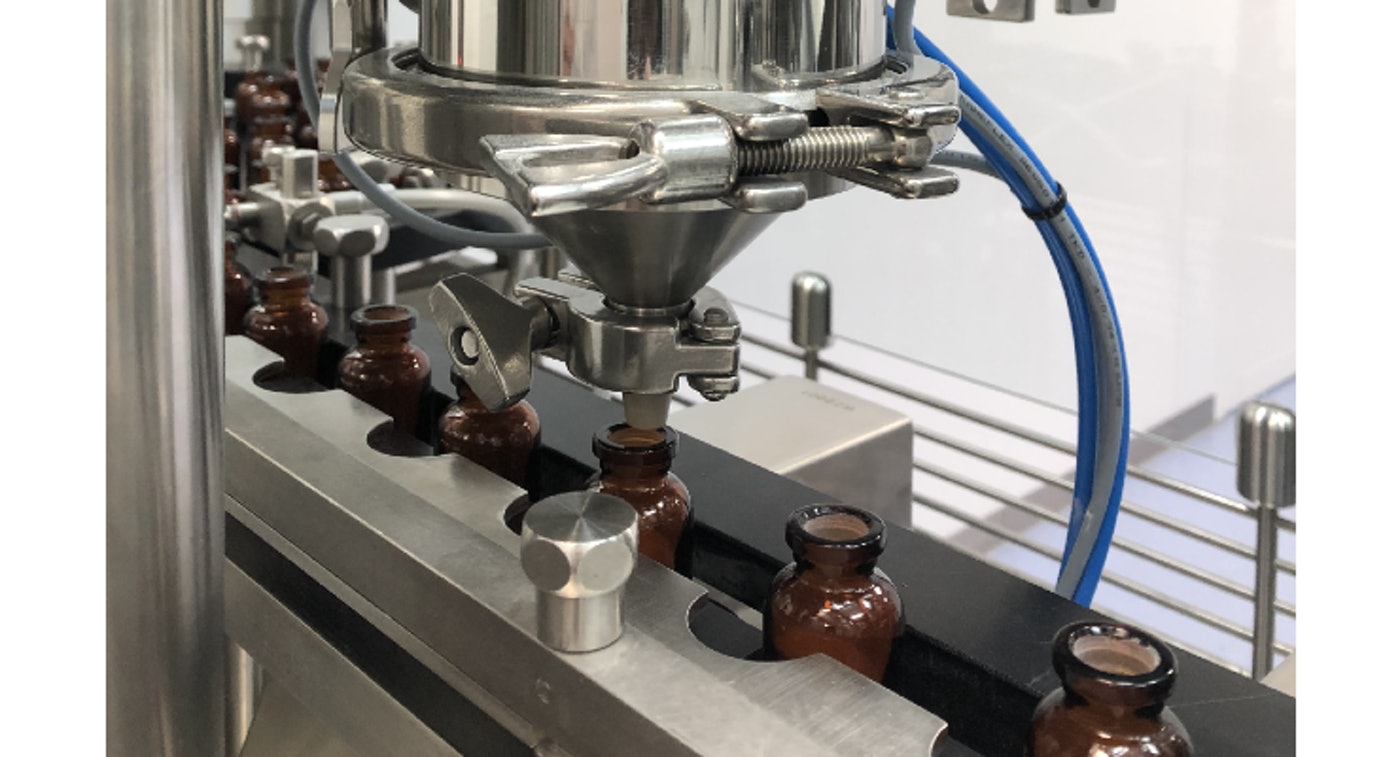
According to research done by Statista in 2018, the global market for personalized medicine was expected to more than double from 2015 to 2022, reaching nearly $2.8 billion in value. As medicines become more personalized, manufacturers will need to answer with greater flexibility and small batch size production.
Bess pro–a branch of bess group that manufactures and distributes high-quality devices and medical products–is working on a range of packaging and R&D processes, including sterilization, sterile packaging, and secondary packaging, as well as on innovations and further developments of products in the fields of head & neck surgery, pneumology, and gastroenterology. This requires the company to produce about 1,000 different types of medical devices and pharmaceutical products in very small batch sizes.
To meet these production size requirements, bess pro turned to Steriline–a manufacturer of complete lines for the aseptic processing of injectable drugs–to deliver a complete line that would substitute manual and laboratory machines with a higher performance automatic line that has an extremely small footprint.
The complete line included:
- The PVFCM50, a powder filling, stoppering, and capping machine under a laminar flow hood
- The RA-V4, a rotary washing machine
- The ST0, a depyrogenation tunnel
It is designed to handle up to 200ml vials with minimal format changes and production speeds up to 200 vials/min, according to vial size and filling volume.
One of the major challenges was the design of the PVFCM50, as Steriline took into consideration the newest filling process requirements which were in-line transport and small width, reduced volume to be monitored and sterilized, and the need for operators to be able to access any part of the machine.
The line included the continuous monitoring of viable and non-viable particles as well as a 100% In Process Control (IPC) of the weight, and a checkweighing system with feedback to the powder filling station. The stoppering process is performed by a vacuum-assisted Pick & Place system while the capping is performed by a rotary blade system. A sensor detects stopper and cap presence and, consequently, the machine rejects all un-stoppered vials as well as those with nonconforming product weight.
Furthermore, a highly accurate dosing process was needed to handle and dose powder for vial filling. So, Steriline designed an auger filling head equipped with a customized screw shape added to the PVFCM50 to protect product integrity.
Steriline further provided two alternatives for Factory Acceptance Test (FAT) virtual procedure, one in live streaming mode and the other recorded and released later for client revision and acceptance.
Bess pro is able to keep low average consumption and purchase costs with Sterline’s production line, which can run automatically without human intervention, and significantly increases production output. The company affirms the line meets GMP standards.
From order to line installation, Steriline provided a turnkey line, fully operating and ready to perform at full capacity–including training and validation assistance–in approximatively 10 months, starting with technical discussions, pre-testing, and trials until the order placement phase.