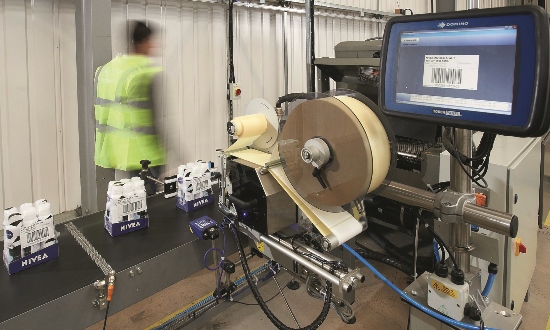
This includes the Oracle Cloud project, scannable 2D / QR codes which it says are crucial for e-commerce platforms, and supply chain systems.
The company said current international trading conditions are very challenging, but demand for its products has remained strong, with total sales growing in 2022.
While its top sectors remain food, beverages, pharmaceuticals and life sciences, Carl Haycock, UK printer operations director, told Packaging News the business is focusing more on the provision of high-quality, variable data printing technology, and how this supports digital transformation in all sectors.
“Variable data printing supports digital transformation for our customers by allowing them to provide more data in a scannable 2D code such as a QR code – to facilitate data sharing up and down the supply chain. For our customers it’s important that our products can do this reliably at any point in the production process.”
Additionally, one of Domino’s key strategic aims will be in providing customers with closed-loop solutions that manage the product coding, and help to minimise errors, waste, and downtime: “This includes data management and deployment from our coding automation solutions, machine monitoring with Domino Cloud, and code verification from our vision offering. These can be provided as part of an integrated solution to ensure the customer that products are of high quality and minimise production downtime.”
Print technology
Domino is now supplying most of its spares and consumables with GS1 Digital Link compliant QR.
Haycock said the inclusion of scannable 2D codes can enable ‘easy booking’ into warehouse systems, and facilitate additional value opportunities in the future, such as allowing customers instant access to information or services.
“We also have some new technologies focused specifically on high-resolution variable data printing, including the K300 – a new, high-speed monochrome solution. The K300 technology can be made available to suit a multitude of different coding needs, including printing on bottle caps to support the move towards recyclable, labelless PET bottles. Labelless PET bottles are fairly self-explanatory, bottles produced without any external labels or shrink sleeves to aid in recycling – these are growing in popularity, specifically in the Asian market.”
He added that Domino is currently working with several leading beverage brands to develop bespoke digital printing solutions, encompassing Domino’s K300 digital printers, for in-line (pre- and post-fill), and near-line printing directly on bottle caps, with 2D codes to provide access to information which would traditionally have been included on the label.
Operational challenges
Operational and energy costs, along with materials costs and staffing continue to be an issue in the sector.
Haycock said supply chain has been a major challenge for all manufacturers and availability of electronic components has been a ‘constant battle’.
“In the main we have been able to keep up supply to our customers through a robust and resilient supply chain strategy, but material input costs, freight, and wage inflation have been huge additional costs and we have worked hard to minimise price increases to customers, keeping these way below industry norms.”
In addition, sustainability is of growing importance to the company’s customers and employees.
Haycock said digital transformation is key to all manufacturers to drive better customer experience and drive productivity.
“The importance of 2D codes, for manufacturers in all industries cannot be overstated. We see the introduction of 2D codes, and particular the GS1 Digital Link as being revolutionary to the way data is shared all stages of the supply chain.
“Solutions for digital printing and coding and marking may not be the first things that spring to mind when an organisation thinks of efficiency and sustainability in manufacturing – but they can play a surprising significant role. Our integrated products and solutions are designed to help customers improve efficiencies by targeting zero coding errors, zero product waste, zero unplanned downtime, and zero capital commitment.”