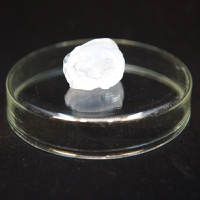
The funds will boost material application research, engage with potential customers and finalize the plan for a demo production facility toward the end of 2024.
Dr. Peter Axegård, CEO and co-owner of FineCell, tells Packaging Insights that the funding will be used “for a detailed process design of our demo production plant including defining optimal conditions for different product properties.”
The investment is Metsä Group’s second investment in FineCell, a spinout of the KTH Royal Institute of Technology in Stockholm, Sweden. The company is a developer of the FineCell technology and producer of CellOx dry cellulose powder.
“FineCell is based on a new method to convert wood- and plant-based cellulose into a material with valuable properties for paint, skin care and cosmetics. The dry CellOx product can be tailored to match specific end-use properties. We are also considering producing hydrogels for customers,” highlights Axegård.
CellOx for material alternatives
The pulp-based materials are made through the novel FineCell technology, which combines pulp-based cellulose with a natural chemical (oxalic acid found in for example, rhubarb), producing a new material that can be stored in a solid form yet is often applied in a liquid form. CellOx is bio-based, light to ship and requires 80–90% less energy to manufacture than other cellulose products, asserts the company.
CellOx can carry other ingredients, making it an “excellent” binding agent for sunscreens, skin creams and paints. It is also transparent, enabling it to be used in various products.
“The world is scrambling to replace fossil-based materials with sustainable ones. Our product, based on softwood pulp from sustainably managed Nordic forest, gives many industries an alternative to the components they are currently using,” says Axegård.
“Metsä Spring has seen the potential in our innovation, and due to their know-how in planning, constructing and operating production plants, including pilots and demos, and their access to the raw material linked to their ambition to upgrade Nordic wood, they were the perfect choice to support us as we move forward.”
Replacing fossil-based ingredients in everyday products is central to many sectors, highlights Metsä Spring. The chemical complexity of these products means that replacing ingredients requires a positive environmental sustainability impact without compromising performance.
Niklas von Weymarn, CEO of Metsä Spring, says: “For us, all technologies that convert softwood pulp into added-value products are of interest. This technology and product stand out, making it especially interesting. The FineCell technology is still young. At this stage, we do not yet know all the directions this platform might take us.”
Combining celluloses
In addition to replacing fossil-based ingredients, the FineCell technology can also be used for applications in healthcare. Also, thin, transparent and flexible films are a key focus area for the company.
Unlike competitors’ offerings, FineCell’s technology provides materials that can be utilized as combinations of many different types of cellulose to produce the desired effect. The patent-protected technology, which allows for constant and energy-efficient change between liquid and solid state, is also “unique” to the company’s technology.
FineCell aims to have the design of its demo plant ready for execution by the end of 2024.
“So far, we are in a pre-study phase. The goal is that the plant will be what we call a ‘Demo Production Plant.’ This means finetuning the basic process steps and, at the same time, producing samples for evaluation by customers in various industrial applications. The capacity we aim for is 1 ton of product per day,” says Axegård.
The company plans to have larger-scale test production underway in 2025, with full commercial production in 2027. It says it has had several meetings with some of the world’s largest brands looking for more sustainable solutions for their consumer products.
Regarding R&D for the upcoming year, Axegård says one of the company’s goals is tailoring product properties. “Another is evaluating several potentially high-value applications such as functional film and barriers, 3D engineering and lightweight foams.”
“Our goal is to bring our bio-based material to more and more sectors, thus replacing fossil-based materials and also increasing the performance of the product. This, in turn, would require scaling up production to the point where we are making a large impact on products people use in their everyday lives. Our story has just begun, and we cannot wait to embark on the next stage in our journey,” Axegård concludes.