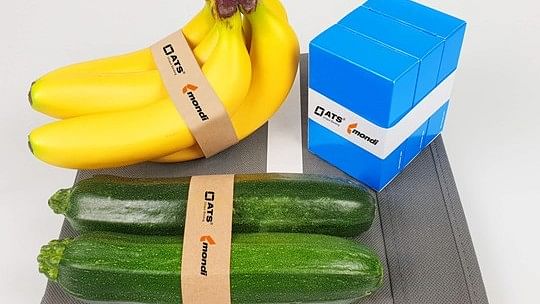
Mondi, one of the global leaders in sustainable packaging and paper, has collaborated with Swiss converter ATS-Tanner to create an innovative paper band that can hold individually labeled products or bundles, reducing unnecessary plastic.
ATS-Tanner uses Mondi’s kraft paper Advantage MF SpringPack and converts it into a band by adding a functional barrier on both sides of the paper. The paper is then sealed using ultrasound, eradicating the need for any adhesive. This ensures that the products are secured with minimum packaging, reducing waste and delivering a cost-efficient solution. ATS-Tanner markets the coated bands under the brand name TruePaper.
The strength of Mondi’s kraft paper means it can hold weights of up to 20 kg, making the band perfect for fruit and vegetable bundles as well as multipacks of bottles and other consumer goods. The paper ensures excellent printing results meaning brand, product, return, and responsible waste management messaging can be communicated to the end user.
Mondi’s kraft paper used for the paper band is made from renewable, responsibly sourced, and certified materials. It is recyclable in existing paper recycling streams across Europe, even fulfilling Germany’s ratio of 95/5.
Carsten Breiter, International Key Account Manager Speciality Kraft Paper, Mondi, says, “By combining world-leading expertise in sustainable packaging with ATS-Tanner’s machinery and skills, we have together created a system that offers great product protection while reducing unnecessary plastic. This is the perfect example of strong collaboration producing a new solution that does just that.”
"We trialed various paper grades, and Mondi’s kraft paper offers the required strength to substitute plastic packaging with this paper band. TruePaper is a resource-efficient solution that can – depending on the banding machine used – wrap products measuring up to 1300 x 500 mm and is convenient to store. Using paper instead of plastic is not the only advantage: an ultrasonic banding machine from ATS-Tanner consumes 98% less energy than it would take to pack a like-sized delivery using a shrink-wrapping machine," Serge Tanner, owner and chief executive officer, ATS-Tanner.