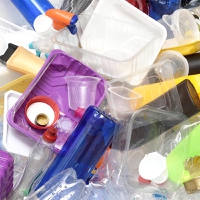
The trials were held at Tomra’s recycling facility in Germany in September, testing the efficiency of Nextek’s technology in differentiating food packaging from non-food packaging. The separation of food and non-food packaging is necessary for meeting the requirements of the UK and EU Food Standards Authorities.
Nextloopp says identifying and sorting any number of pack variants from bleach bottles to milk bottles in any plastic type is a world-first, capable of transforming the way society recycles the growing volume of single-use food packaging waste.
“If the labeling technologies are adopted by UK brand owners and retailers, Nextloopp technology could be on shelves within two years,” Professor Edward Kosior, Nextek’s founder, tells PackagingInsights.
“The technology is ready to go and the funding to invest is available. The packs are being made every day, they just need an invisible, integrated PolyPrism label. The next stage is adoption by the supply chain to join the ends of the circle.”
Plug-and-play recycling
The sorting trials’ success provides validation for Nextloopp’s PolyPrism “plug-and-play” marker system, as used on Tomra’s sorting equipment for commercial purposes.
The trials tested packaging submitted by Nextloopp members, with the project seeking to establish the packaging’s selectivity when co-mingled with 20% non-food packs.
“The results were exciting and impressive, as they demonstrated for the first time how the integrated technologies of the packing, label with marker and NIR/VIS automatic sorter, could work together at full speed in a real-world context,” says Kosior.
“The results were predicted based on earlier trials. However, the packs were not brand owners’, and it was an excellent result to have confirmed.”
“During the recent trials held at our Tomra Test Centre, we achieved very promising results on all PP 3D samples in all test runs with state-of-the-art NIR/VIS technology,” reiterates Ralph Uepping, technical director at Tomra.
“We exceeded the required 95% purity for food-grade in each test run. The next important milestones will be a field demonstration and demonstrating chemical compliance with food-grade regulation.”
The trials will be extended in early 2022, with tests on a fully developed series of commercially ready labels.
Closing the polypropylene loop
The trial results mark Nextloopp’s first anniversary, as it pioneers mechanical recycling for PP, the most popular plastic in the FMCG sector. According to Nextloopp, 210,000 metric tons of food-grade PP are used in pots, tubs, trays and films each year in the UK.
Kosior explains sorting plastic waste into polymer types is the first of three necessary steps for closing the loop on PP and creating a global low carbon economy. The next step requires splitting the plastic packaging into food and non-food fractions.
The final step involves Nextloopp’s patented decontamination process – PPristine – which “unlocks the markets to food packaging.”
Kosior claims the Nextloopp project is the catalyst for transforming current food-grade PP recycling for the next recycling success story. “PET was first and now it’s the turn of PP,” he says.