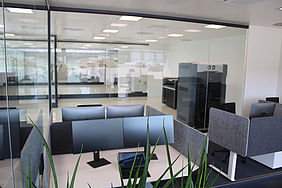
The RDMC was founded back in August 2019 and is equipped with all commonly used printing technologies for additive series production. “Despite the current protective measures implemented in the context of the coronavirus pandemic, we completed the construction project on time, thanks to the outstanding commitment of the teams at our location in Waldachtal,” emphasized managing director Jens Harmeling.
His colleague on the management team, Dr. Axel Höfter, added: “Our customers will be mainly existing customers of the divisions, and our focus will be on series production. We have already implemented the first projects for this successfully.” For the Industrial division, for example, they produce a component known as a trailing edge serration that helps to reduce the noise of wind turbines; the latest development stage of this is now being manufactured additively. Prototypes for a new active grille shutter model are being produced for the Automotive division, and the RDMC is printing cores for injection molding tools with conformal cooling for the production of a tracheal tube (wind-pipe tube) for the Medical division.
Additive manufacturing is quick to use and can be tailored to individual requirements. During the current coronavirus pandemic, the RDMC is producing an attachment for door handles that allows doors to be opened and closed using the forearm; this is intended for the Röchling locations in order to prevent the virus from spreading within the company. A prototype of a face mask with a visor has also been printed and is now being produced by Röchling Medical.
Five employees currently work for the RDMC. Röchling invested a total of EUR 2.5 million in the 3D printing center.
The planned opening ceremony had to be postponed due to the coronavirus pandemic.