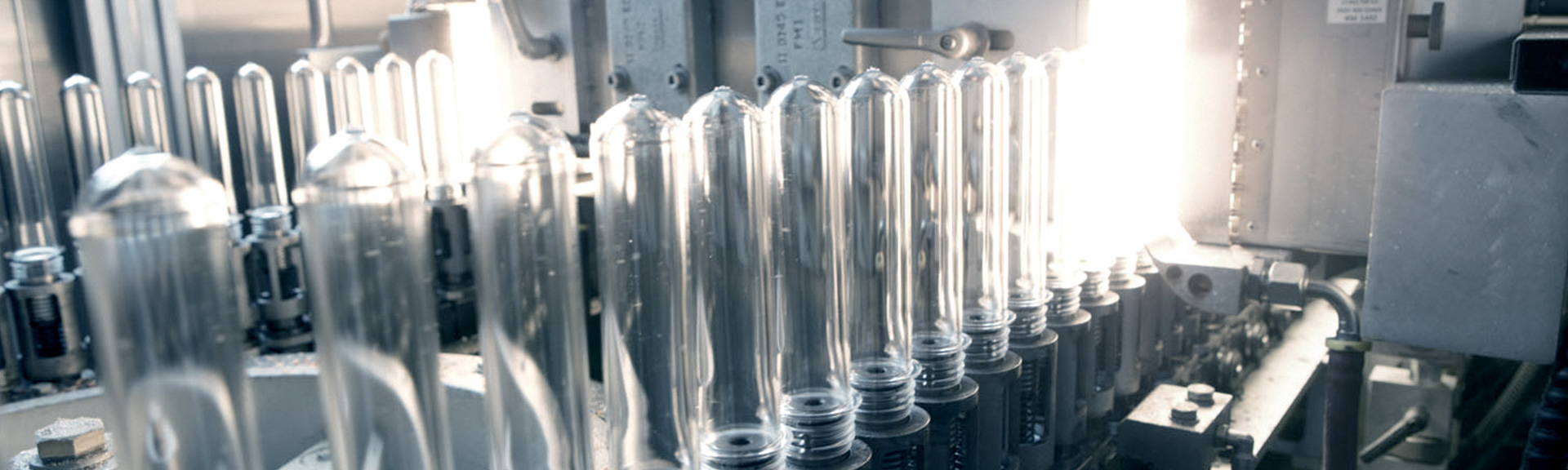
Gable X Cleaning Solutions Company Limited, located in Chaguanas (Trinidad and Tobago), has ordered its second blow moulding equipment from Sidel, the leading global provider of PET, can and glass solutions for liquid packaging. With the recently acquired Sidel blowing machine, the co-packer has significantly improved its production capacity, adding as much as 75% to its daily output of PET packaging. Alongside being fully equipped to meet the growing demand for PET packaged goods in the region, this choice enables Gable X to protect their competitiveness and guarantee a regular and reliable supply flow.
Today, Gable X is one of the most advanced, innovative, custom packaging blow moulding players in the Caribbean. The company is active in three business segments: sale of raw materials, manufacturing of cleaning products, and blowing of PET bottles. 85% of the PET containers blown by Gable X serve various size manufacturing companies in the region, making them the first Trinidadian company to offer many local, regional, and even international customers lightweight bottles in PET.
The co-packer is a leading supplier of PET bottles, producing 250,000 units daily, six days a week 1 , with over 50 different formats and shapes. The company provides packaging for the food, beverage, agricultural and home care industries to hold products as diverse as pepper sauce, peanuts and grains, soy bean oil, fresh coconut water, milk drinks, fabric softener, hand soaps and disinfectant. The products are distributed in the domestic market but are alsoexported widely to the broader region.
Sidel blow moulding solutions among “the best in the world”
Gable X’s satisfaction around the first piece of Sidel blowing equipment installed in 2014 was reinforced by very strong recommendations from local bottlers. One of them, also a returning Sidel customer, decided to install a Matrix TM Combi for still water. The company chose the integrated blow-fill-cap solution from Sidel to increase their operating capacity. They were able to improve cost efficiencies and add new products, as such expanding their market reach, while better serving existing clients.
When the Trinidadian co-packer renewed the confidence in their long-term partner Sidel, the company was looking to manage the increasing demand for PET packaging in the market and labour challenges they experienced on a daily basis. By equipping one of their production lines with a Sidel blower, Gable X showed their trust in the company’s advanced technology and high specifications to produce up to 12,000 bottles per hour. The incorporation of the Ecoven into the blow moulding system means that preform heating time is reduced and fewer heating modules or lamps are needed with the oven’s electrical consumption cut by up to 45%. Gordon James, founder, owner and Managing Director of Gable X, says, “Having now two blowers from Sidel brings many advantages for us. Our capacity has increased by 75% and the equipment represents the state-of-the-art when it comes to energy savings and production efficiency, working fewer hours for a higher output.” He continues, “Sidel’s blower is rated as one of the best in the world and for a good reason. The blow moulding solutions are extremely easy to use and require very little maintenance, contributing to decrease our delivery time – another key condition to win our customers’ preference. Not less important, Sidel is number one in terms of online support and after-sales service and helps us keep the long-term efficiency of our equipment.”
Lightweighting, durability and rigidity as key factors for PET
James goes on to explain that one of the main challenges Gable X is facing is to facilitate PET adoption among their customers: “The key arguments I am using are that, by packaging their products in PET, they would get the transparency of glass, along with other benefits.” PET allows the consumer to visually experience the product inside the container, without scuffing and scratching the bottle’s surface. Additionally, the virtually endless design options for the PET bottle shape and format can also enhance the appeal and brand identity of the finished product on the supermarket shelf. The durability and rigidity of PET significantly reduces the possibility of damages throughout the value chain and the consumer experience is enhanced, as the packaged product is lighter and safer for the user to handle. “Multiple lightweighting opportunities around PET bottles also save on raw material and transportation costs. Making the long story short: PET is better because it is more durable, cost-effective, and recyclable as a packaging material,” he concludes.
More resistant and more stable bottles with Sidel StarLite
The Sidel blowing machine recently installed at the Gable X plant in Trinidad ensures top consistent bottle quality with a large process window and the electrical stretching, with no compromises on the performance and the lightweighting potential of the containers. Marcel Ndoumna, Sidel Sales Manager for North America, comments: “With the new blow moulding equipment, the customer is also benefitting from the patented, award-winning Sidel StarLite™ bottle base, which significantly increases base resistance and stability. This means the customer can improve bottle rigidity, while enabling a lower package weight and reducing energy consumption during production. The end result is a PET bottle that can cost less to manufacture, yet offers better pallet stability and higher bottle integrity throughout the supply chain, without compromising the safety standards of the beverage inside.” Based on the successful cooperation with Sidel, the Caribbean co-packer is again considering the company as a valuable partner in setting up additional installations to serve the heat- resistant PET packaging needs for hot-filled beverages.