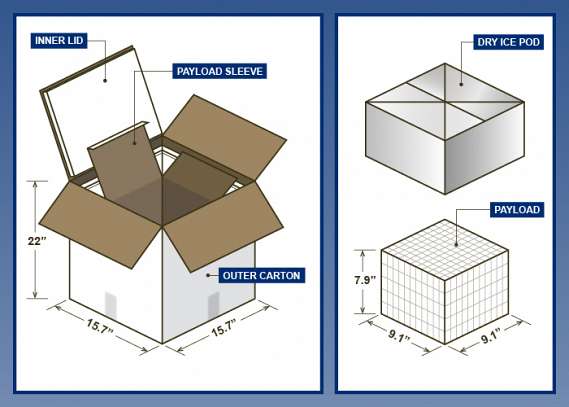
While many of us have been surprised at the speed with which the COVID-19 vaccine has been developed, we may not consider the additional complexity associated with safely transporting it. In the case of one of the available vaccines, Packaging Corporation of America collaborated with several companies to create the best possible solution.
“None of us really knew too much about the vaccine when we started the process back in June 2020,” said Steve Collins, the PCA Sales Representative involved in the project. “You’re making it up as you go, and it’s kind of fun. I know so much now, and it’s very rewarding to me that it’s been an overwhelming success.”
PCA’s expertise in packaging design, coupled with one of our partners’ expertise in cold chain packaging, enabled us to build the right solution. The project presented several challenges, including keeping the box between negative 80 and negative 70 degrees Fahrenheit for 48 hours and being able to insert monitors and dry ice to ensure that the vials stayed in that temperature range.
“We went through 20 to 30 different designs to arrive at the end product,” Collins said. “We needed several different pieces of corrugated to keep the vials suspended and prevent them from touching the dry ice. Our Mooresville, North Carolina, design team did an outstanding job meeting all of these needs.”
Production of the vaccine boxes began in August 2020. Collins highlights the teamwork needed to create a solution that is helping to save lives. “The expectation is high, and our people are committed to doing anything needed to get the job done. I wouldn’t have been able to harness that kind of support from any other company.”
Because of its importance in history, the first shipment — including PCA’s box and all of its interior packaging — recently became part of the Smithsonian National Museum of American History’s exhibit on the global pandemic.