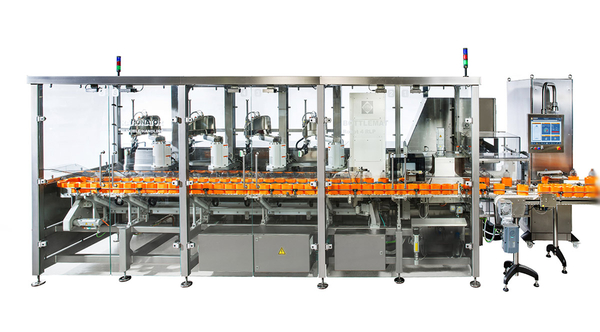
Automated system with four robot arms increases output by about 20 percent
High process reliability and flexibility through the RATILIGHT Puck System
Cosmetics manufacturers like to highlight their products with inventive format designs. However, this is associated with increased demands on the flexibility of the filling lines, since each format change requires a time-consuming changeover of the line. At the same time, the operating costs should be as low and the output as high as possible. For this reason, RATIONATOR Maschinenbau GmbH from Hillesheim, Germany, which is specialized in filling lines, has decisively further developed its bottle handling machine BOTTLEMAT Robot as part of the filling line: By adding a fourth vacuum gripper, which inserts the bottles lying on a conveyor belt into the transport pucks serving as containers, the possible output could be increased by about 20 percent. The RATILIGHT Puck System used in all lines produced by RATIONATOR guarantees high process reliability and compatibility with a multitude of different formats. The handling of PET bottles has been significantly improved through modifications to the machine's loading area. With the plant-internal networking of the individual units in the filling line, the requirements of industry 4.0 are also met - delays can be detected automatically and enable an optimization of the operation.
"Bottle handling systems form the first step in the filling process chain", explains Michael Musat, Sales Engineer at RATIONATOR Maschinenbau GmbH. "At the same time, they are particularly important because the precision and speed at the beginning of the handling process determines how much output is possible at the end". In order to meet the increasing competitive pressure in the cosmetics industry, RATIONATOR has further developed its bottle handling machine BOTTLEMAT Robot so that four, not as previously two or three vaccum grippers pick up the bottles from the conveyer and insert them into the RATILIGHT Pucks.
Due to the additional gripper the BOTTLEMAT Robot can now set up up to 165 bottles per minute instead of the previous maximum of 140 bottles and forward them to the filling process.
80 RATILIGHT Pucks for 1000 different bottle formats
In addition to the highest possible output, the focus for bottling in the cosmetics industry is also on format diversity. "80 percent of our machines are manufactured for the cosmetics industry," reports Musat. "However, as there are no design standards in this area, manufacturers are constantly developing new formats to differentiate themselves. This means that the filling lines must also have a particularly high degree of flexibility in order to process the many different formats. RATIONATOR recognized this problem already in the 1980s and therefore developed the so-called RATILIGHT Puck System, with which all filling lines of the company are equipped today. The special feature is that the bottles do not simply stand on the belt, but are inserted beforehand into a transport module, a RATILIGHT Puck, and therefore cannot fall over. The RATILIGHT Pucks all have the same outer dimensions and are only differently shaped on the inside. This makes it possible to transport a wide variety of sizes and shapes of bottles in a stable manner and to considerably reduce format parts and changeover times. Â "80 RATILIGHT Pucks are compatible with more than 1000 different bottle formats," says Musat. "The possible volume of the bottles ranges from 5 to 1000 ml." Moreover, the transport forms produced by injection moulding are available from stock at low cost. Thanks to the combined control of robot unit and machine, no service technician needs to be called in to adjust the system to a new format. The BOTTLEMAT Robot has a common control system so that a single teaching process for the new format via the touchpad of the control unit is sufficient. Separate teaching of the individual robot units is not necessary. Specifically, format adjustment is carried out via the bottle check, which is responsible for coordinating the robot arms with vacuum grippers. The high-performance camera system records new formats simply and easily. "This means that the BOTTLEMAT Robot now also has the ability for supervised learning, the employee only enters the measurements and places the format under the camera for learning. The system takes care of the rest," says Musat. In addition, formats that have already been taught can be activated simply by pressing a button.
Improved handling of PET bottles
A further advantage of the new range of the BOTTLEMAT Robot is the processing of PET bottles. Because freshly produced PET bottles have a very high surface adhesion, which creates a sticky effect and makes handling more difficult. "In the further development of the BOTTLEMAT Robot, we have therefore made various optimizations to improve the handling of PET bottles - especially in the area of feeding", explains Musat. Corners and edges in the bottle infeed area were removed, the transport process was straightened, the elevator belt now rises at a smaller angle and the area of the receiving belt and the return opening were enlarged. As a result, especially bottles with a larger volume can spread better and do not stick to each other.
Machine modules react automatically to delays
In addition to possible problems with PET bottles, other difficulties often occur during filling: Bottles can fall over and leak during transport, so that operation must be stopped and the system cleaned. The BOTTLEMAT Robot is doubly protected against this problem. "Thanks to the RATILIGHT Puck System the bottles always stand securely and cannot fall over. And if a delay does occur, for example in the bottle infeed area, the system modules are networked with each other and automatically reduce the processing speed or stop the system", says Musat. In addition, non-inserted bottles are automatically returned to the circuit and thus neither fall out of the system nor cause a malfunction. With this contribution to the transformation of the industry towards Industry 4.0, RATIONATOR increases the process reliability of its lines and strengthens their independent operation.
Contact:
RATIONATOR
Maschinenbau GmbH
Alsheimer Str. 1
67586 Hillesheim
Germany
T +49 6733 9470-0
F +49 6733 9470-109
sales(at)rationator.de
Statement of Data Protection