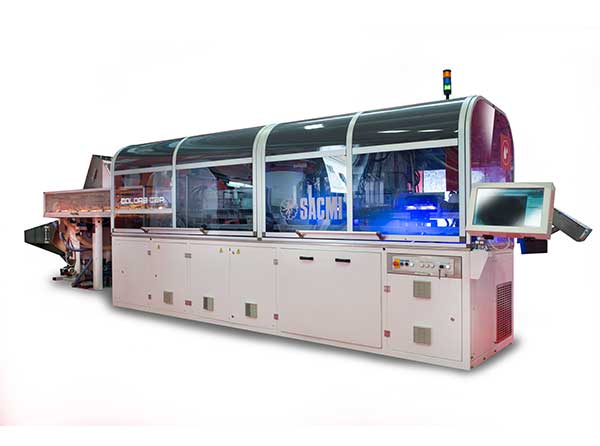
A starring role for the new IPS 400, the machine that makes Sacmi the perfect all-round partner for converters. Also on show: integrated Sacmi solutions for the beverage industry, from stretch-blow moulding to filling, plus the new COLORACAP for the digital printing of caps
Over 90,000 visitors from 160 countries are expected to attend Gulfood Manufacturing, the event scheduled to take place in the United Arab Emirates capital. Over the last few editions, in fact, the number of participants and exhibitors has trebled. An all-round plant engineering provider to the beverage sector, Sacmi will be at the Dubai World Trade Center (7-9 November 2016) to present its range of technologies and plant engineering solutions, all designed to maximise automation, process integration, flexibility and the use of ‘green packaging’.
The all-round partner for the converter world Sacmi has taken the fight to its competitors with a preform production solution with injection technology. This – as part of a long- term project (IPS, injection preform moulding) - has led to the development of the IPS 400, a machine that combines the consolidated characteristics of ergonomics, productivity and user-friendliness with clear-sighted innovations on the production process and flexibility fronts.
An evolution of the successful IPS 220, the new IPS 400 was developed by Sacmi to respond to the specific needs of the converter world. In addition to major innovations on the quality front – from the FIFO circuit in the plasticizing unit to the new system for direct unloading of preforms into containers in the cooling area – the IPS 400 also offers excellent compatibility with existing moulds, including competitors’ products: a strategic choice that lets the Sacmi Group act as an all-round market provider, offering customers a competitive advantage when plants need renewing and upgrading.
Complete beverage lines Integrated Sacmi solutions for the stretch-blow moulding, filling and production/application of caps are also becoming more and more established on international markets. Every stage of the process is automated and takes place in an ultra-clean environment thanks to solutions that ensure product sanitisation during both stretch-blowing (SBF, stretch blow forming) and filling (AWS filler range). More specifically, the Sacmi stretch-blow former also stands out as it allows the installation of single-cavity moulds (for sizes of up to 3 litres) or dual-cavity moulds for sizes smaller than 0.75 l. This means, in addition to very high productivity (up to 80,000 half-litre bottles an hour), that the machine provides remarkable flexibility, making mould changeover tasks easier and allowing saturation of the downstream filling line.
“Green packaging” and digital printing of caps Completing the range are the solutions for ever- thinner, high-performing caps and containers (obtained thanks to the intrinsic advantages of compression technology, in which Sacmi leads the world in terms of number of machines installed and market shares). More specifically, at Gulfood Manufacturing we’ll also be showcasing the new COLORACAP, the cap digital printing machine that, as of this year, is also available for the decoration of coloured caps. An innovative solution that takes Sacmi to the final plastic cap digital decoration frontier: unlimited colour coverage, ultra-high definition yet also extreme flexibility to respond to every type of manufacturing or promotional requirement.
Sacmi, product and service excellence Thirty years of know-how and experience in the industry and a far-reaching after-sales service make Sacmi the perfect global partner to the beverage industry. Alongside compact blowing-filling solutions, Sacmi also provides – for every stage of container, cap and primary packaging production - advanced vision systems for total, ultra-fast quality control directly on the line. All Sacmi beverage production solutions are developed and tested at the Group’s R&D facility, certified by top international players in the industry. Visit the Sacmi stand at Gulfood Manufacturing 2016 (hall 3, n° B3- 18).