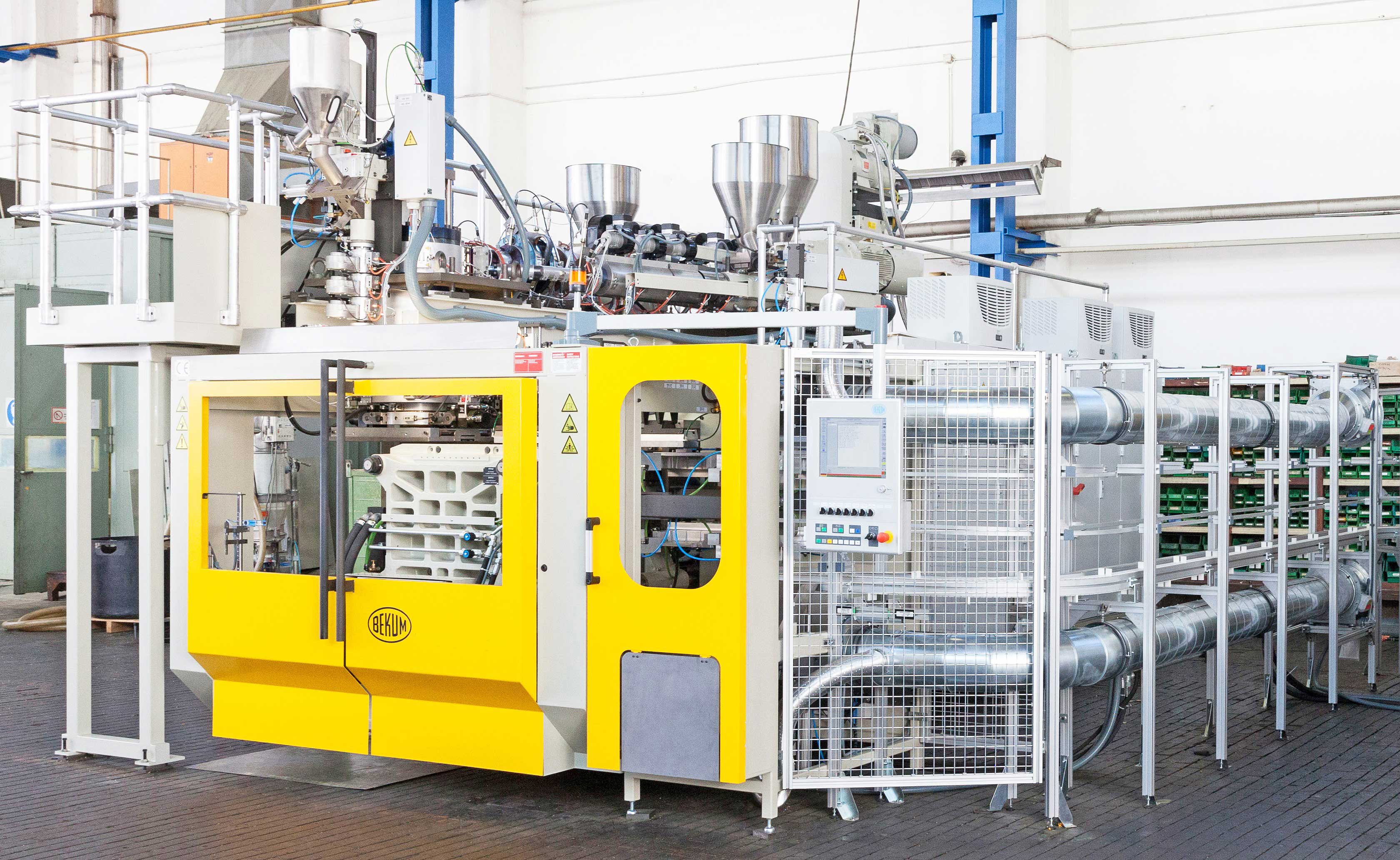
Premiering at the K 2016: New electric blow-moulding machines for the production of canisters
- Energy-saving machine design with fast closing pressure build-up
- High-performance blow-moulding technology: Single-station production for up to 240 canisters per hour
- High flexibility with greater performance in canister production
Berlin (Germany), 08/08/2016: The blow-moulding machine manufacturer BEKUM is extending its electrical series EBLOW. The newest addition is the EBLOW 37 for packaging applications. It premiers at the K 2016 to specialists in the industry. As early as 2007 BEKUM presented the first electric blow-moulding machine at the K- Messe (plastics trade fair) in Duesseldorf. The continual development of the machine range was followed by the introduction of the EBLOW 07 series with patented C- frames.
The newest development of the Berlin technology leader is the EBLOW 37, a blow-moulding machine for high-performance production of blow-moulded articles, especially for canisters. With this model BEKUM is looking to win points in the packaging sector, particularly from producers who are interested in an energy-efficient, flexible machine solution tailored for high-performance.
Improved added value with the EBLOW 37
The EBLOW 37 design has its roots in the hydraulic machine range. For the Berlin company however, the future is now also electric. The goal of the new innovation was to take the experience from the manufacture of the EBLOW electric packaging machine series and combine it with the advantages of the proven BA 34.2 hydraulic canister machine. The hydraulic BA 34.2 has been successfully positioned in the market with over 200 machines. Now BEKUM is transferring this to an electric generation of machines, which offer a technically and economically attractive solution for producing articles between 10 and 35 litres. Typically, this model is targeted toward canister manufacturers all over the world. According to BEKUM, the high-performance EBLOW 37 provides canister manufacturers with the option of upping their added value through increased output volumes.
The best of both worlds - an energy-saving system with fast closing pressure build-up
The EBLOW 37 follows the performance of the BA 34.2 without compromises. Here, BEKUM is relying on a new energy-saving system for the movements of the machine: Closing unit and mould closing function are electrically driven, while the closing pressure build-up for effective force transmission is achieved through servo hydraulics and is thus available quickly as usual. This hybrid principle makes use of the advantages from both types of drive technology.
Pure high performance: Up to 15% more output volume with 20 l canisters
With a closing force of 370 kN and a mould width of 700 mm, canister production is the domain of the EBLOW 37. According to BEKUM, the comparison measurements of the single-station machines are very promising. Compared to a conventional hydraulic solution, the EBLOW 37 enables production to be increased by up to 15%. This corresponds to an output volume of 240 pieces per hour based on a 20 l lightweight canister as reference item. These values recommend the EBLOW 37 as a new standard in its class.
High extrusion quality with high-tech spiral distributor blow heads
BEKUM provides its machines with spiral distributor blow heads, which feature excellent, uniform wall thickness distribution in the pre-form and the finished article. This results in significant potential for the operator to optimise the parison quality not only for single-layer products, but especially when it comes to products with a multi-layer structure. And there is no need for the customer to compromise on user-friendliness either: the heads can be easily set from the front of the machine. And not only that: the design of the head enables faster colour changes than standard design principles, which leads to a direct increase in machine productivity. Change material for cleaning is also reduced to a minimum. The compact construction of the spiral distributor heads is also impressive. Their smaller surfaces mean considerably less energy is required to heat them.
Flexible application expands the range of production
BEKUM’s many years of manufacturing know-how from the packaging sector has gone into the machine development of the EBLOW 37. The user can thus expect a high degree of flexibility. The setting of blow moulds with different mould thicknesses can be performed quickly and very conveniently thanks to a production-optimising automated calibration run. In combination with the company’s own specially designed and produced extrusion heads with spiral distributor technology, the EBLOW 37 also impresses on the material side. Many blow-mould materials made from HDPE and PP in single- and multi-layer designs (3-layer and 6-layer), including those with transparent strips and polycarbonate, can be processed with excellent results. The new design allows very fast colour changes for the highest level of flexibility and cost efficiency. Through the use of a characteristic BEKUM top or bottom calibration, the production range can be expanded even further. Many proven and process- safe options of the familiar BA 34.2 will also be available in the new EBLOW 37. The future is electric – including in the packaging.
BEKUM at the K 2016: Hall 14, C03.