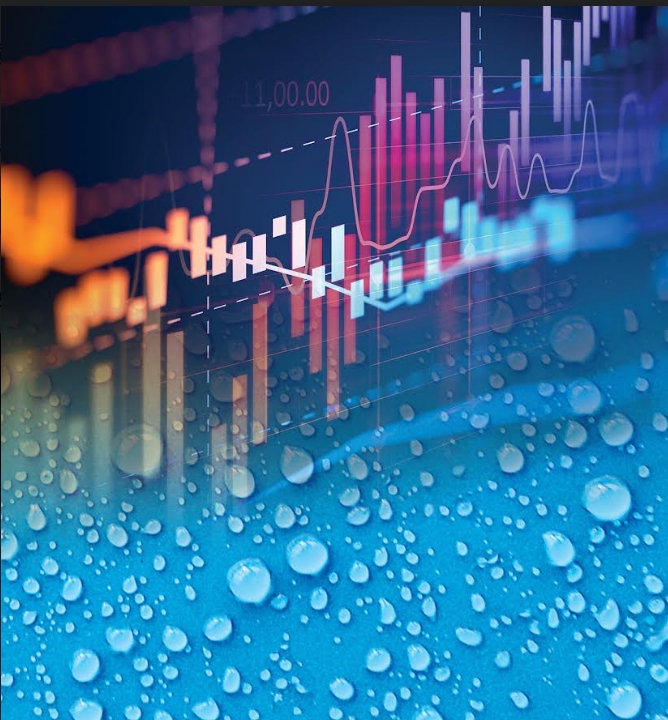
Company’s Process Analytical Monitoring (PAM) Moisture Control
system provides 100% inspection of food items, while offering
production process optimization and intuitive operation.
Northern District, Israel – Yoran Imaging, which develops and supplies thermal imaging systems to optimize filling and heat-sealing processes on packaging lines, will debut a system for inline moisture control and process optimization at Pack Expo, November 3-6 in Chicago. At Booth LU-8847, the company will offer live demonstrations of its new Process Analytical Monitoring (PAM) Moisture Control solution, which utilizes thermal imaging technology to provide 100% moisture monitoring, and continuously oversees the overall process to maintain defined moisture level boundaries.
Yoran Imaging’s PAM Moisture Control system is a robust step up from two common methods of moisture control. For food brand owners utilizing moisture control inspection via sampling, Yoran’s inline, 100% monitoring system yields immediate and substantial upgrades to both inspection comprehensiveness and, by eliminating the need for inspection-related line slowdowns and stoppages, production output. For companies already using inline inspection via spectroscopy, PAM Moisture Control provides a significantly simpler system for operators, as well as enhanced process control that can virtually eliminate unscheduled line downtime.
Through a passive process that requires no direct product contact, the PAM Moisture Control system converts recognized moisture content into corresponding thermal images. The system then generates this information into useful moisture and process control data, helping operators keep the line within specified moisture contents while recognizing any desultory trends that, should they continue uncorrected, could bring the line out of spec.
The system’s elevated inline moisture and process control capabilities lean on sound science: water molecules vibrate vigorously when absorbing infrared light. This allows the thermal imaging-enabled system to determine a product’s moisture content with exceptional precision – and, from there, display these findings in a user-friendly HMI setup. As the PAM Moisture Control system continues inspecting each and every product, it also recognizes developing trends, indicating the need for preventative corrections that prevent small issues from becoming larger, line-stopping ones.
In being among the first to utilize thermal imaging technology specifically for moisture control processes, Yoran Imaging aims to bring food industry customers a set of layered benefits. For starters, it eliminates outdated sampling and single-purpose spectroscopic sensors through cost-effective, comprehensive and contact-free inspection of each product, vastly decreasing the likelihood of defective products entering the market.
At the same time, productivity also can be considerably increased, with user-friendly data alerting operators when preset quality or OEM parameters are degrading, providing guardrails and guideposts that minimize machine downtime through informed preemptive measures. Helpfully, the company’s systems also occupy a small footprint and are easily integrated into a wide range of production line configurations.
About Yoran Imaging
Specializing in the food & beverage sector, Yoran Imaging utilizes cutting-edge thermal imaging technology to revolutionize the filling & heat-sealing process on packaging lines. Drawing upon more than two decades of thermal imaging inspection experience, the company’s solutions provide non-invasive, 100% in-line inspection combined with production-optimizing data collection and analysis. This real-time sealing data allows for enhanced predictive maintenance, reduced labor investments and minimized materials and product waste.
Yoran Imaging’s groundbreaking Process Analytical Monitoring system replaces inadequate manual sampling with comprehensive product inspection, provides unprecedented levels of packaging line insight, and preempts production failures before they occur. The result is dramatically heightened brand protection, smarter manufacturing processes, and a more efficient packaging operations.