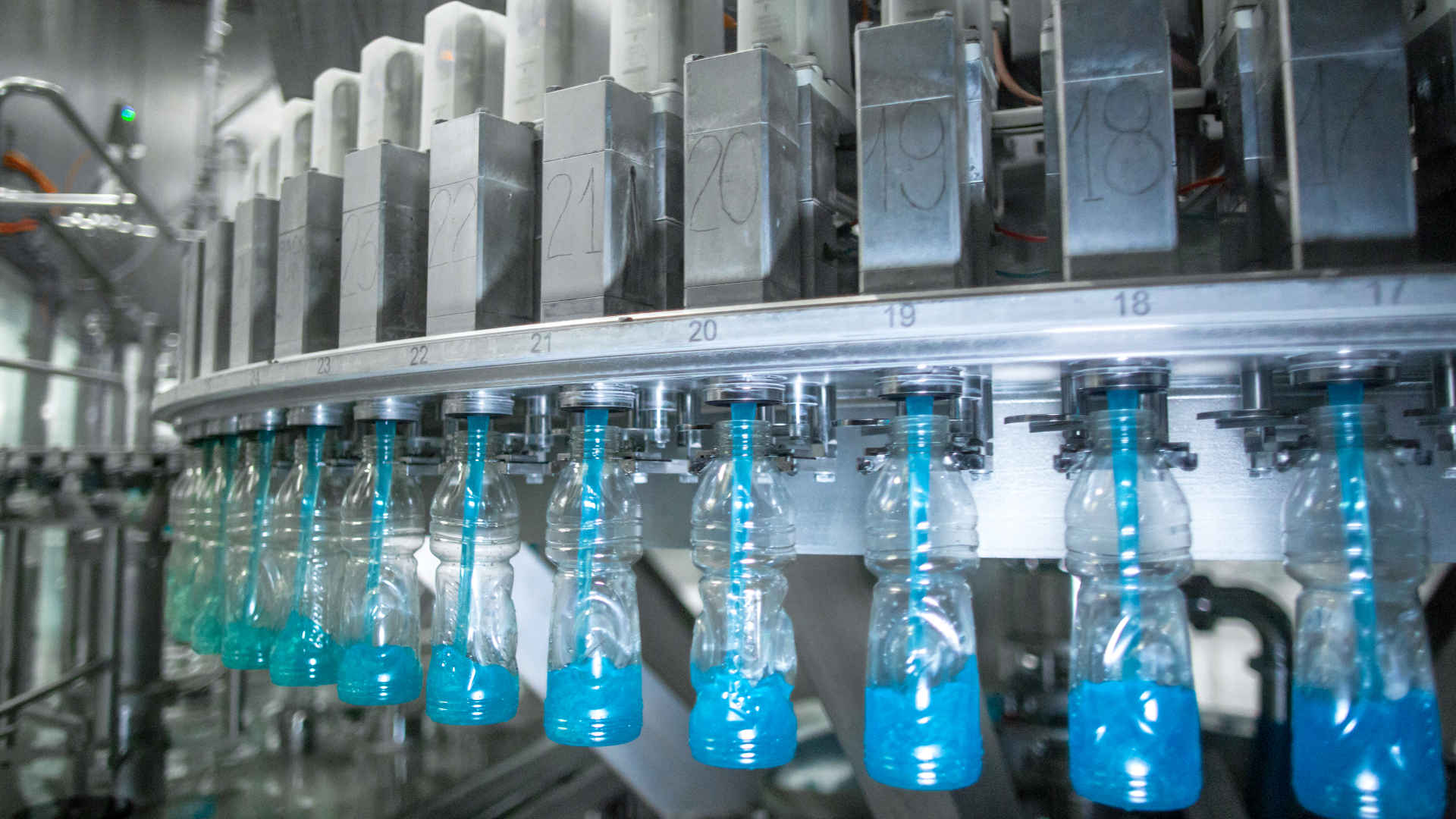
In collaboration with Sidel, Cervecería y Maltería Quilmes – the largest drinks company in Argentina – have reached high levels of efficiency, of up to 100%, on their most recent complete hot-fill line, as part of their ongoing pursuit of excellence. This complete, high-speed bottling solution produces, among other things, the Gatorade brand of isotonic beverages in PET containers, in compliance with PepsiCo's quality standards. The new line offers advantages in terms of production flexibility and protection of the environment, particularly due to energy savings.
Quilmes have been operating in Argentina for over 130 years. The company started out in the beer business by opening their first brewery in the city of Quilmes, about 20 kilometers southeast of the capital, Buenos Aires. “Over the years, Quilmes have expanded across beverage categories by acquiring a carbonated soft drink business. This happened about 20 years ago, with PepsiCo’s exclusive franchise for production, distribution and marketing of the brand's full line of beverages in Argentina,” explained Juan José Ferrer, Plant Manager at Quilmes. The company also participate in the water business through Eco de los Andes SA, the result of a joint venture with Nestlé Waters. “The company’s objective is to provide consumers with quality beverages and to take care of the environment. The investment in Sidel’s bottling line is perfectly aligned with this aim,” he adds.
Doubling PET production capacity with an integrated bottling solution
Investing in a new hot-fill production line at the Southern plant in the city of Buenos Aires was necessary because it is the only facility which supplies the entire national market and also exports to Uruguay. “Both PET container lines were at the top end of their capacity, so we needed a bigger line to increase our market share in Argentina. The second objective was to have a more modern line with lower energy consumption and better efficiency,” says Juan José Ferrer. With this new investment in Sidel’s line, Quilmes have more than doubled their capacity to produce beverages in PET containers, going from 22,000 to 45,000 bottles per hour (bph).
The company had different alternatives of who their bottling line supplier was going to be. “We were convinced by the good experience we had with a variety of Sidel equipment and decided to continue with them. Currently, we are very satisfied with the performance of the line, two years after its installation. Another factor in choosing Sidel for this investment was that Quilmes were looking for a complete solution to satisfy our needs. We took into account not just the bottling line, but also product processing via pasteurisation (Tetra Pak Processing Systems), in order to maximise the potential synergies. Sidel showed the necessary flexibility for this and were able to provide a solution, creating a better model of efficiency and production quality for us,” he continues.
Quilmes were also quite satisfied with the positive collaboration of Sidel’s team of experts throughout the project stage prior to the line installation, as well as during the installation itself and for the aftersales service. He goes on, “Obviously we started by looking for the best options for Quilmes with the line design team. Afterwards, the start-up phase was the most intense, when we required assistance from Sidel. The machines were installed in a new zone of the factory floor, and we underwent the typical difficulties related to our utilities; but in all truth, we were able to solve the problems as they arose quickly and safely with Sidel’s assistance.” Another advantage of working with Sidel that Quilmes recognised early on was the technical support service, both from Field Service Engineers (FSE) and from remote. In case of any need or emergency, this service provides assistance from a FSE 24 hours a day. Alternatively, support personnel can remotely connect to the machine and recommend the best solution. “We used it several times, and it helped us to keep production running successfully.”
Production reliability and flexibility to comply with PepsiCo’s standards
The hot-fill bottling line is characterised by its excellent production flexibility. “It has the capability of hot-filling isotonic drinks, juices and products with or without pulp. Additionally, this line is also able to cold-fill, in order to offer consumers a wider variety of products,” he says. Today, Gatorade is produced in a number of flavours and sizes: 500 ml, 750 ml, 1200 ml and, more recently, 300 ml, with either flat or sports caps. As for labelling, the new solution enables the placement of partial sleeves on just one part of the bottle or full-body sleeves on the whole bottle, providing several marketing opportunities to stand out on supermarket shelves.
“As for the flexibility provided by our production line, we also have the possibility of handling several pack options, such as 6-packs, 12-packs or 24-packs.” When it comes to the palletising of hot-fill products in PET containers, quality is a very important matter and must be guaranteed. “To face the long transport distances on often challenging roads, palletising must be precise, reliable and very stable. We are very happy with Sidel's palletising solutions, since they guarantee the integrity of our products, so that they reach consumers intact,” he highlights.
Quilmes operate as a PepsiCo bottler and, therefore, a new line validation must involve a specific approval protocol. Prior to the launch of the industrial production on the line, there was a validation stage for all the different containers in Sidel’s packaging labs in France. According to the Plant Manager, “the individual validation of each of our Gatorade bottles was executed according to PepsiCo’s specifications, which enabled production of the moulds. Due to PepsiCo’s requirements, during the first packaging runs, we complied with a quality protocol regarding line efficiency and the number of marketable bottles during the process. Every step was carried out successfully.”
Respect for the environment and 100% efficiency
After defining the purchasing specifications for the line, Quilmes worked with Sidel’s technical and project teams to find an ideal layout and location for the machines, which optimised staff ergonomics and the travel time between the different control stations, as well as the supply of consumables. All details for line start-up were reviewed, again in collaboration with the Sidel team, to achieve the best results for this project. “Today, we are very satisfied with the location of the machines in each of the areas, with the general positioning of operators, handling of supplies and access to places where spare parts are stored.” Quilmes’ teams were pleasantly surprised by the efficiency levels reached by the line. “We are working at an average of 95% efficiency and, sometimes, the line even runs for many hours at 100%. Because of the way the line was designed, it is perfectly balanced to ensure reliability. It is also very important to mention that, despite the difficulties, this efficiency was reached very quickly during start-up. At present, with the 500 ml container, we are working at 45,000 bph with 95% efficiency,” Juan José Ferrer summarises.
This line includes the plant’s first Sidel Combi blow-filler, which provides many advantages in line with Quilmes’ commitment to the protection of the environment. The Combi consumes less energy than the blower they used to have, thus eliminating, for example, the air transfer of bottles. In addition, it prevents the exposure of containers to the elements during air transfer, which improves product quality. Fewer people are needed to man the machines during day-to-day operations, which lead to more effective use of our operators and enables them to focus on other maintenance and quality tasks. This is why Quilmes selected the Combi.
Additionally, environmental protection is a very important topic for Quilmes. “In terms of energy, the line offers a thermal equilibrium system enabling us to reuse the heat provided by the hot bottle in the cooler for the first heating stage of the liquid before the pasteuriser. This has contributed to heat savings between 10% and 15%, when compared to the previous line.” The other energy-related benefit involves the Combi blow moulds. “The heating process for the previous moulds was done with hot oil, which consumed more heat. Now, with our Combi, the process is carried out electrically. This ensures a very precise heating process in the areas we need to heat, and it provides heat savings of 15%, compared to the older-generation blower we used to have.”
“In a nutshell, we would recommend Sidel. It is a company with an enormous track record in the beverage world as well as cutting-edge technology, services and support. I would be very happy to work with Sidel again in the future,” concludes Juan José Ferrer.
Editors Note: The images within this document are for illustrative purposes only and should not be used for reproduction. If high resolution copies are not attached with the document, please contact Nikolaus Schreck at F&H Porter Novelli for copies – see contact details below.
-----------------------------------
For editorial, advertising and sponsorship enquiries, please contact:
F&H Porter Novelli
Nikolaus Schreck, Senior Consultant
Tel: +49 (0) 89 12175 123
Email: sidel@fundh.de