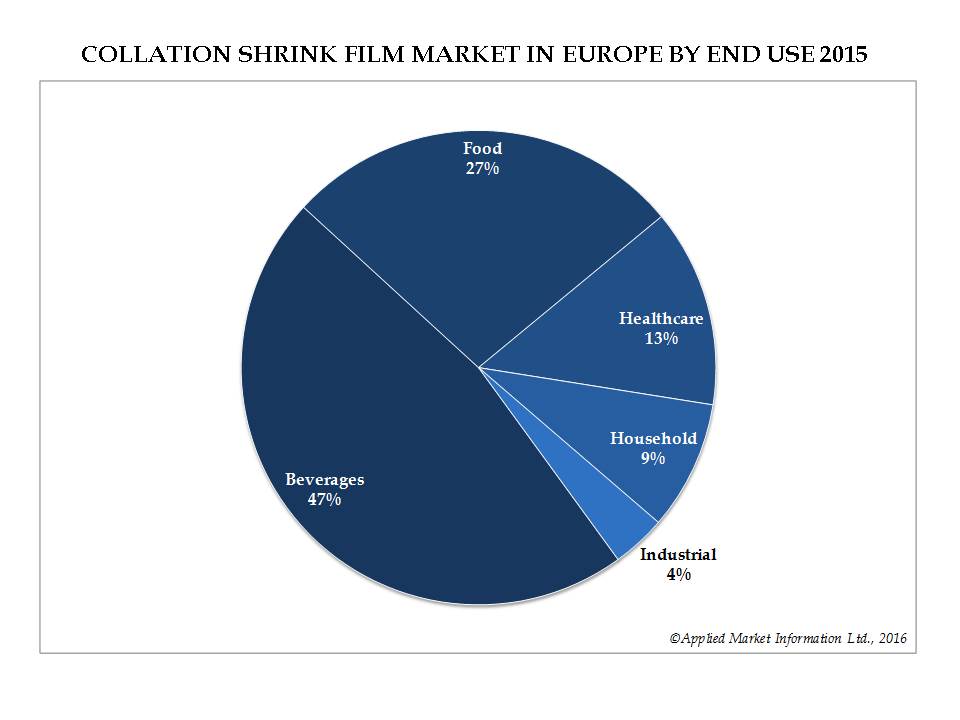
AMI, Bristol, 18th July 2016 - AMI Consulting, a division of Applied Market Information Ltd., has just published a new report on the collation shrink film market, analysing the latest trends in the use of these packaging films, along with developments in raw material technology, innovation and changing film formulations.
Currently, many millions of euros are lost annually as a result of goods becoming damaged in transit. This trend has been on the increase over recent years as a result of downgauging across all levels of packaging, i.e. primary, secondary and tertiary. For example significant downgauging has occurred with plastic bottles, collation shrink film and pallet stretch wrap, any or all of which can have a serious impact on the overall load stability. Companies need to understand that it is the optimisation of the overall packaging system that is critical to the safe transport of palletised goods. Film extrusion technology and advances in raw material properties will continue to facilitate cost reduction without compromising film performance and safety criteria.
At 800,000 tonnes demand, collation shrink film represents a major segment of polyethylene packaging film activity, accounting for 10% of all polyethylene films produced in Europe. Much of the increase in usage of collation shrink film over the past few years has been masked by the down-gauging resulting from advances in polymer technology and enhancements to extrusion equipment. Even so, the market for these films is forecast to advance at a moderate pace of around 1.5% per year over the next five years to reach 850,000 tonnes by 2020.
The use of collation shrink films as a secondary packaging medium has gained in popularity throughout Europe. Initially, the main thrust leading to the change from printed cardboard to printed shrink film holding multipacks of bottles or cans was to achieve a reduction in the weight of packaging. Not only was this switch financially desirable, but it also helped brand owners achieve packaging waste reduction targets, which are based solely on packaging weight regardless of the material used. And so the growing consumption of shrink film has been driven by the ongoing switch from glass bottles to their lighter plastic or metal alternatives, hence resulting in moving away from crates and cardboard boxes to flexible film multipacks. Changing from a cardboard box to a shrink film multipack can lead to a weight reduction of up to 70%. In addition, the switch has led to a reduction in carbon footprint, lower transport costs and, increasingly, marketing benefits. With the trend towards co-extruded films, the use of metallocene resins in the outside layer has provided a high gloss finish which has led to the development of very high quality print on the shrink film, enhancing product appeal by providing an eye-catching pack at point of sale and differentiation.
The largest sector to use collation shrink film is the beverage market, which currently accounts for almost a half of all polyethylene collation film demand and has been driven by growing popularity of functional and 'on-the-go' bottled and canned drinks. Food is also a significant market, particularly canned items, and represents around one quarter of collation shrink demand. However, only about 15% of collation shrink film for the food sector is printed, because much of it is for transit packaging only and is removed before the product reaches the shelf, whereas 60% of film for the beverage sector is printed as it is intended that these products be sold in bulk.
The largest players in the collation shrink film market which operate also in other large volume polyethylene sectors include Armando Álvarez Group, British Polythene Industries, Coveris, Papier-Mettler, Plastotecnica, RKW and Sanders Polifilm.