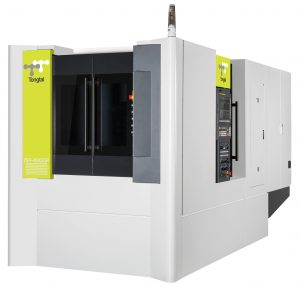
[LORAIN, OH – JULY 2018] The new SH-4000P Horizontal Machining Center from Tongtai was developed for mass production lines. The new compact machine has a 35% smaller footprint than the previous model, allowing for maximum shop floor space utilization. At only 69” wide, floor space is minimized. Sold and serviced by Absolute Machine Tools Inc., the Tongtai SH-4000P horizontal machining center is the latest generation, low cost, state-of-the-art high speed machining center. This machine will exceed the demands of any manufacturer with high volume machining needs. The compact size consumes very little valuable floor space while the fast speed will deliver more parts per hour than competitive machines costing thousands more.
The machine is a XY traveling column type design where the pallet moves in Z. The APC unit, located in front of the machine, provides easy access and slashes idle time. The APC is a rotary type pallet changer and it exchanges the pallets in only 5.9 seconds. For pallet rotation in the machining envelope, a full contouring “B” axis precisely indexes the pallet every .001 degree and a hydraulic clamping mechanism is used to clamp the pallet in place for excellent repeatability. The B axis is high speed, with 90-degree index time of 0.5 seconds
The SH-4000P features an ultra rigid Meehanite cast iron frame with an advanced 3-point leveling system. The eco-friendly LHL / LubeUSA grease lubrication system is standard for ways and ballscrews – no coolant contamination and no waste oil. The 40mm (1.57”) diameter ballscrews are class 3 with a double nut pre-loaded and pre-tensioned design allowing a blazing rapid traverse rate of 2362 inches per minute. Furthermore, high-speed acceleration drastically reduces non-cut time (X,Y, Z acc/dec of 1.0G). The ABS (Absolute Pulse Coder) servo system does not require zero return. The machine can be started anytime from any position, saving non-productive time. A standard rear discharge chip removal system includes a center trough design with high volume chip wash for efficient chip removal. A combination dual level caterpillar-type conveyor with fines separator is standard and is suitable for virtually any types of chips / material.
At the center of the machine is our high power integral spindle with 15,000 RPM and spindle acceleration from 0-7000 in just 0.48 seconds and 0-15000 in only 1.9 seconds. Deceleration from 12000 RPM to stop is only 0.8 seconds. Our powerful spindle, which switches windings on the fly, produces 50HP peak (10 min. rating), 35 HP in high and 25HP in low while producing 184 ft./lbs. of peak torque at only 980 RPM. To enhance milling capabilities, a Big Plus dual contact spindle is standard. Air/oil mist is used for spindle bearing lubrication to increase spindle life.
The standard 60 station automatic tool changer provides ultra fast tool selection. Tool change time is only 1.4 seconds tool to tool due to the use of the patented Sankyo RollerDrive™ gearbox for the arm mechanism. Average chip to chip time is only 2.6 seconds. The ATC system is a random style system.
The Fanuc OiM-F conversational control is standard to provide reliable state-ofthe-art controllers and the latest in servo and spindle technology. The OiM-F is capable of handling the most demanding high speed machining applications and is available with a full complement of high speed machining options for mold detail and electrode machining.