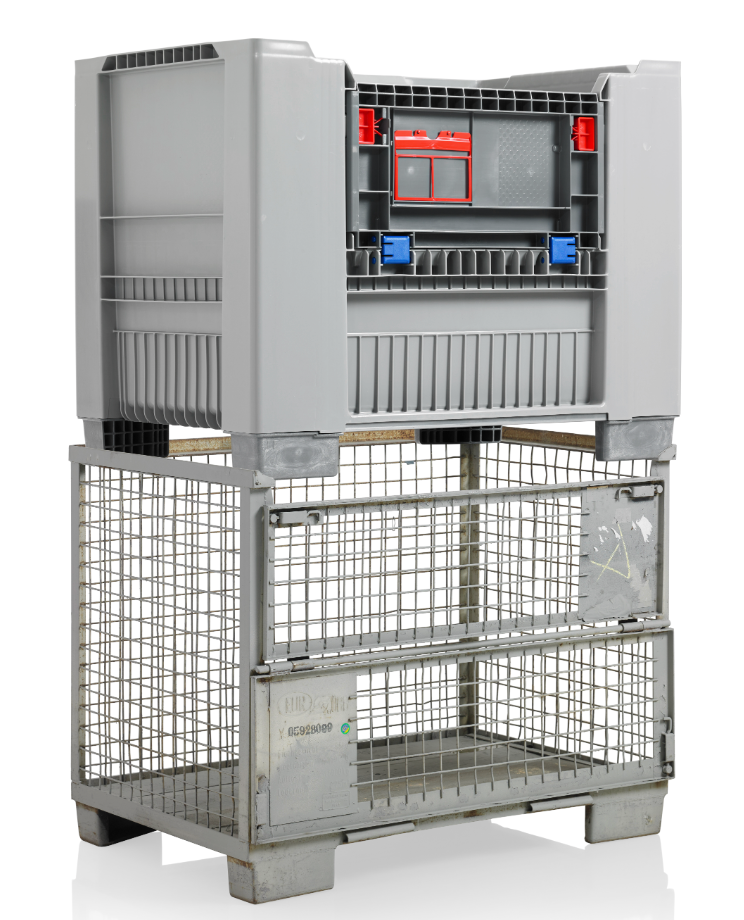
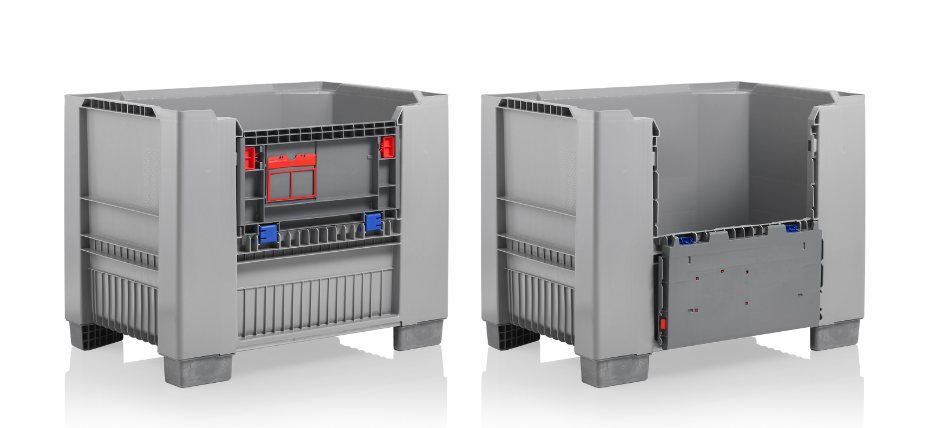
Craemer's automotive know-how has also flowed into the development and production of transport and storage boxes and other logistics solutions made of robust PE, which are manufactured using the injection molding process.
The latest innovation is the Kubo, short for plastic box, as a perfect alternative to the DB Europool lattice box (Gibo) often used for heavy goods and components and for all applications with high requirements. The new Craemer Box made of PE has numerous advantages over the steel frame lattice construction. It is light and robust, easy to empty, clean and dry, guaranteed corrosion-free, very resilient, versatile and stackable, poolable and repairable, and also protects sensitive automotive components thanks to its closed shape.
Plastic alternative to the metal lattice box
The Gibo-compatible Kubo is suitable for an alternative such as a parallel application. With the same external dimensions (1240 x 835 x 970 mm / internal dimensions: 1132 x 732 x 831 mm), it has a volume of around 610 liters; with a net weight of 51 kilograms (including the front wall flap), it has a stacking load of 3000 kilograms, a payload of 1000 kilograms and a dynamic load of 2100 kilograms. The design is based on the standard UIC-435-3 (International Union of Railways) or DIN 15155/8. The four feet are designed as interchangeable corner columns. Craemer's new Kubo four-way box runs maintenance-free and trouble-free on all common conveyor systems and is suitable for automated high-bay warehouses.
In addition to the advantages of the PE material - protected contents due to the closed shape, low dead weight, and therefore cheaper empty transport (around 25% lighter than Gibo) - the Kubo brings with it enormous stability and good stackability. The stacking height of two Kubo is 1940 millimeters, with a maximum payload of 1000 kilograms per box, three plastic boxes can be stacked on top of each other. As with the lattice box, the upper edges offer ideal stacking areas.
The corner pillars strengthen the container, and reinforcements of the lower deck with three transverse and two longitudinal profiles ensure high strength of the container floor. The steel L-profiles on the long sides of the box form - in addition to the additional ribs over the entry openings - further impact protection against forklift tines. As a four-way box, the Kubo offers all-around protection.
Loading and unloading of stacked boxes
A large front panel flap with a locking mechanism and hinges on one of the long sides, opening downwards and outwards 180 degrees (like the Gibo), allows for easy loading and unloading of components even with stacked boxes. The front wall flap (705 mm wide x 423 mm high) is not flush with the edge of the box when it is closed so that the forklift tines can be retracted when stacking or removing a box. To protect the opposite wall from a possible impact of the forks, the upper edge is equipped with an internal chamfer.
The design with clean and straight lines, minimal ribbing, and a rounded shape stands for easy cleaning and drying. In addition, the Craemer Kubo is temperature-resistant from -30 to +40 degrees Celsius (briefly up to +90) and resistant to most chemicals and cleaning agents. It is optionally available with a floor drain, with or without a front wall flap, and with an RFID transponder for seamless tracking. Printing fields are used for embossing logos or inscriptions, knob fields are for temporary stickers, and the front wall flap carries a document holder.
Due to its compatibility with the lattice box, the robust construction, and the high payload, the new plastic box represents an ideal Gibo alternative or supplement for the automotive industry. Craemer's Kubo is particularly suitable for transporting heavy automotive components.