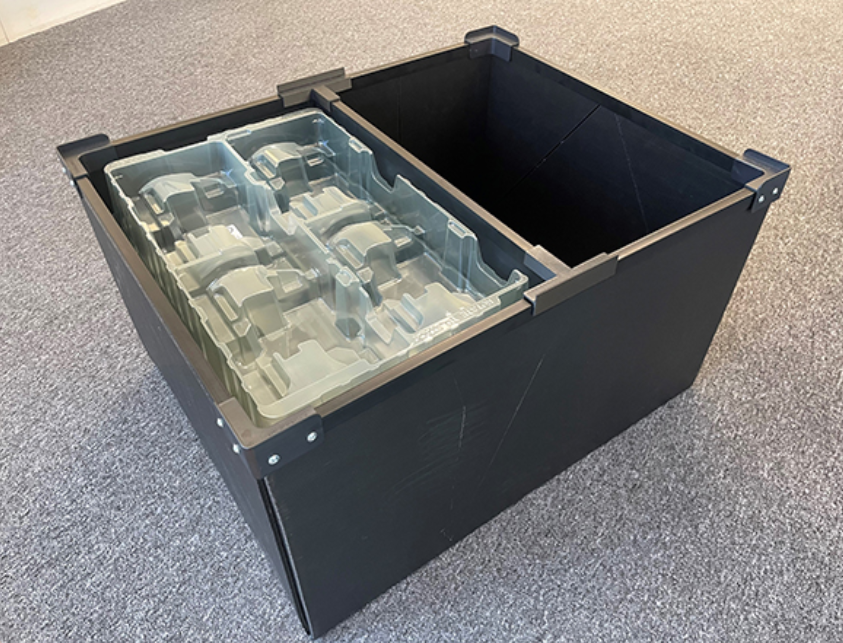
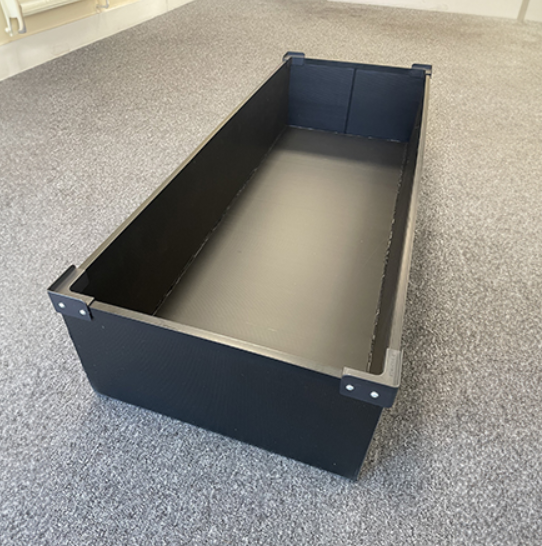
Twinplast Drives Innovation in Sustainable Packaging for Major Luxury Automotive Brand
In a landmark project, Twinplast has rolled out a custom packaging solution for a prominent luxury car manufacturer, demonstrating its expertise in designing durable and reusable containers specifically tailored for the automotive industry’s high-value, sensitive components. Known for its reliance on precision and efficiency, the automotive sector demands specialized packaging solutions, especially as more manufacturers embrace Just-In-Time (JIT) manufacturing, requiring deliveries to arrive damage-free, on time, and ready for assembly.
The Challenge: Protecting Complex and Critical Components
With the release of its latest model, featuring new technologies and intricate components, the luxury car manufacturer approached Twinplast to develop a robust and reusable packaging solution capable of withstanding the heavy demands of industrial logistics. The brief was precise: create a custom, highly impact-resistant container that would secure each component in place without unnecessary fillers, maximizing material efficiency while also accommodating the client’s commitment to sustainability.
The packaging had to be resilient enough to safeguard items such as batteries and hydrogen fuel cells, while also being lightweight and optimized for transportation to minimize space and emissions.
The Solution: Durable, Efficient, and Environmentally Friendly
Twinplast’s technical team engineered a fast-prototype design that met every need. Using high-density corrugated polypropylene, Twinplast crafted a strong, durable outer casing, reinforced with corner brackets and rim supports for extra resilience. Inside, a custom insert was developed to precisely fit each component, ensuring a snug, secure cradle for items with zero movement during transit. This design eliminated the need for additional padding, reducing waste and creating a streamlined unpacking process that saved on handling time for the client.
To support ease of transport, Twinplast incorporated ergonomic handles, further simplifying the logistics process. Importantly, the polypropylene material is both reusable and recyclable, aligning with the manufacturer’s goals for a lower carbon footprint and reduced environmental impact.
Leading by Example in Sustainable Practices
Twinplast’s commitment to sustainable practices didn’t end with the product itself. The company’s in-house recycling system processes excess raw materials back into production, further reducing waste and supporting circular economy practices in the supply chain.
The result? A robust, reusable, and fully recyclable packaging solution that ensures safe delivery of critical components while supporting the automotive manufacturer’s ambitious carbon reduction goals.
Twinplast’s success in this project underscores its role as a leader in bespoke packaging solutions across industries, pushing the envelope in both innovation and environmental stewardship.