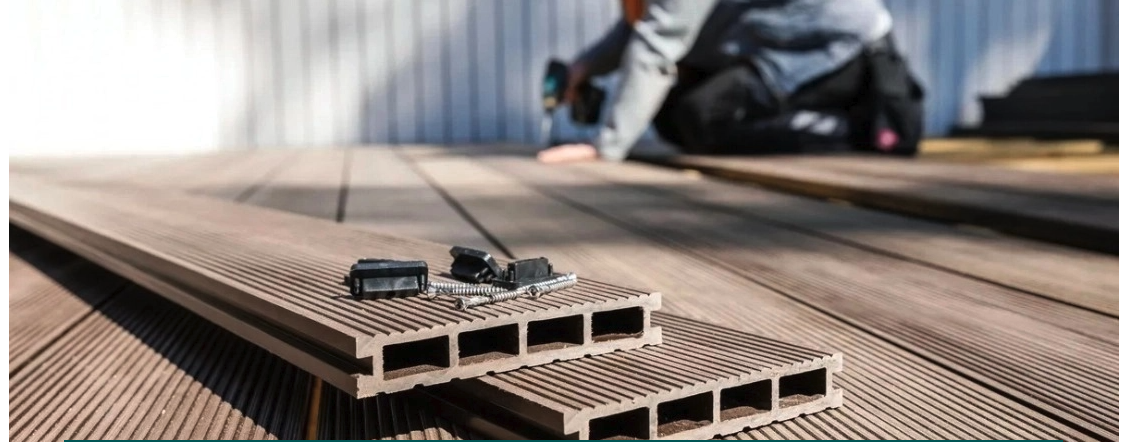
Wood Plastic Composite (WPC), composed of a blend of polymers (PVC, PE, PLA, or PP) and wood dust or vegetable fibres, is paving new frontiers, particularly in construction and street furniture. Its versatility, reliability, and lower production costs compared to wood have led to significant growth in the global market, projected to reach $5.84 billion by the end of 2021, with a CAGR of 12.4% from 2016 to 2021. The residential sector is a major driver of this growth, as WPC offers an elegant and durable solution for coatings, furniture, flooring, and decking, matching the aesthetic appeal of natural wood with enhanced resistance and impermeability.
Furthermore, WPC is gaining traction in the automotive industry, where it is used to manufacture lightweight components, thereby reducing vehicle weight. Notably, WPC is 100% recyclable and helps curb deforestation, as the wood used in its production is often sourced from furniture industry waste.
Bausano’s Advanced WPC Extrusion Technology
Leveraging over 70 years of expertise, Bausano offers state-of-the-art wood plastic composite extrusion lines for profiles and granules, capable of incorporating up to 100phr of wood or natural fibre. Bausano’s POLYWOOD technique supports two key processes:
- Direct Wood Plastic Composite Extrusion: Direct extrusion of profiles from raw material.
- Indirect Wood Plastic Composite Extrusion: Processing material starting with granules.
The latest extruders in Bausano’s MD Nextmover series boast high performance, intelligent remote control, an intuitive human-machine interface, and a variety of modular accessories.
Industry 4.0 Integration with Orquestra Software
Bausano’s innovative Orquestra software and IIoT Data Manager enable continuous, real-time monitoring of production parameters, critical for processing WPC. The software simplifies material processing, optimizes the entire process, and provides immediate performance reports with user-friendly graphs. Orquestra integrates all components of the extrusion system with advanced Industry 4.0 technologies, facilitating intelligent diagnosis and predictive maintenance. This integration connects all extrusion machines to company management systems like ERP, MES, and CRM, promoting automated production management.
Case Study: Collaboration with a European Furniture Manufacturer
A notable example of Bausano’s success is its collaboration with a leading European furniture manufacturer. The project involved installing an extrusion line for granules, designed to mix PVC dry blend with sawdust from production waste, and two plants for the extrusion of finished products. The three lines, managed by a single control centre, are perfectly synchronized, showcasing the efficiency of Bausano’s solutions.
Commitment to Continuous Innovation
In a well-established sector like extrusion, Bausano champions continuous innovation, introducing technological paradigms that ensure high competitiveness for producers of plastic and composite materials like WPC. The launch of Orquestra marks a significant achievement, helping end users enhance production performance, product quality, and lead time through long-term analysis of operational parameters.
Bausano’s dedication to innovation and excellence positions it at the forefront of the WPC industry, driving sustainable solutions and technological advancements in extrusion processes