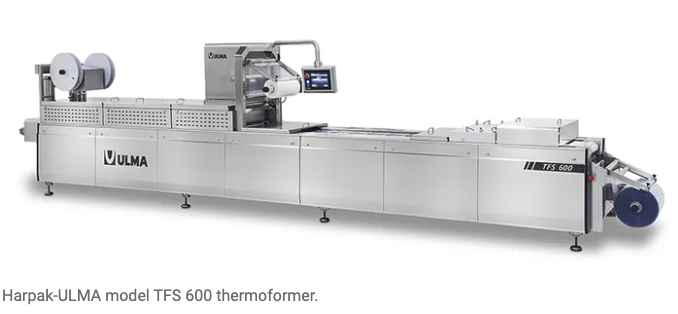
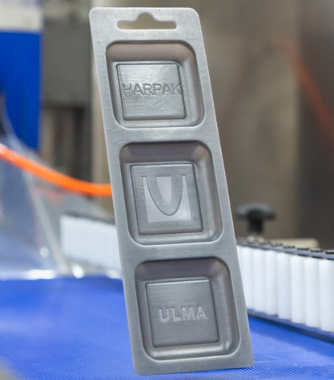
Various companies, including packaging suppliers, are increasingly utilizing the flexibility of 3D printing to explore new opportunities for themselves and their clients. Harpak-ULMA, for instance, now offers a nationwide 3D printing service tailored specifically for thermoform tray package prototyping. This service allows customers to easily, swiftly, and affordably customize their tray designs to suit specific marketing needs and preferences.
Harpak-ULMA's 3D printing service for tray package prototyping provides merchandisers with unparalleled flexibility and versatility in prototyping. Whether adjustments in dimensions, incorporation of intricate features, or inclusion of branding elements are required, this service ensures quick and efficient customization. Additionally, customers have the option of in-person collaboration at Harpak-ULMA’s Customer Experience Center at its Taunton, MA headquarters.
Kevin Howard, an associate engineer at Harpak-ULMA, highlights that their Taunton facility is the first among the company’s three Centers to be equipped with 3D printing capabilities. He emphasizes the ability to provide same-day or overnight tray samples, ensuring nationwide accessibility of 3D printing services to all customers.
The company's other Centers in Ball Ground, GA, and Irvine, CA, may also incorporate additional 3D printing capabilities based on customer demand.
Key advantages of 3D printing prototyping of plastic trays include custom differentiation, significant reduction in time and cost compared to traditional methods, and a more environmentally friendly process due to reduced waste. The rapid, iterative approach facilitated by 3D printing allows for quick incorporation of feedback, leading to improved final products.
Joshua Allen, Harpak-ULMA's marketing director, emphasizes that their 3D printing-enabled package prototype services eliminate barriers, significantly shortening the prototyping process and reducing costs. He highlights the quick and inexpensive iterations made possible by this approach.
Kevin Howard further explains that turnaround times for one-off trays produced on the printers are about two days compared to two to three weeks with traditional methods. Additionally, prototyping costs are drastically reduced, with costs typically ranging from 1% to 4% of traditional methods.
In terms of 3D printing details, Howard describes the printers used and the polymers employed. The Form 3L systems by FormLabs and Bambu X1-Carbons by Bambu Lab are utilized for producing durable, high-quality samples with various resins.
Harpak-ULMA notifies customers of the new 3D printing service at the beginning of each project, allowing them to opt for sample trays/tooling before committing to a final design. The company aims to scale this department throughout the year to accommodate increasing demand.
Moreover, Harpak-ULMA remains responsive to customers' needs beyond thermoformed trays, developing testing brackets, mounts, and reusable demo products using 3D printing technology.
Howard anticipates exponential growth in the utilization of 3D printing for tray prototyping as the company expands its outreach to prospective and returning customers.
FAIR USE DISCLAIMER-
This site contains copyrighted material the use of which has not always been specifically authorized by the copyright owner. The said material is only for the purpose of information and dissemination and reporting of news and events. This constitutes ‘Fair Dealing’ as per the Indian Copyright Act, 1957 and is an exception to Copyright Infringement. This website acts an aggregator of news pertaining to the packaging industry and does not claim any ownership/copyright whatsoever of the content posted except where otherwise stated.