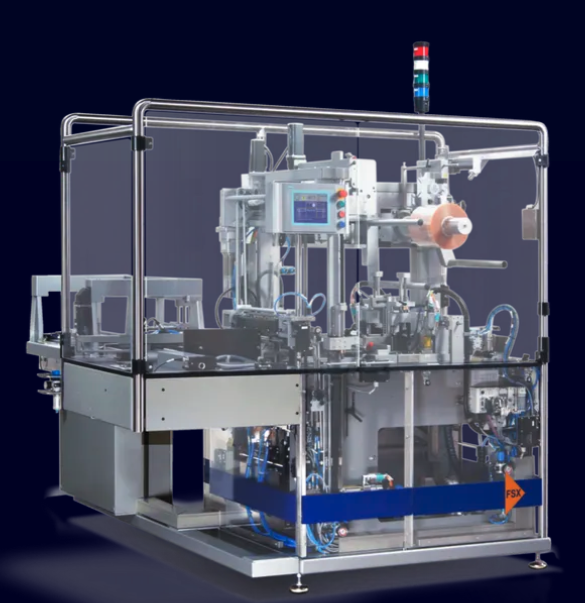
Artificial intelligence (AI) was employed to optimize the control system of a Sollas packaging machine, with prior training conducted on a Digital Twin of the machine. This application serves as a prime example of how the Industrial Metaverse is revolutionizing the manufacturing sector by amalgamating AI, Digital Twin technology, and software-defined automation.
Imagine attempting to wrap a box in transparent plastic – the result often involves wrinkles and uneven corners, testing one's patience. Sollas, however, defies this norm with machines capable of wrapping 160 boxes per minute, each with impeccably smooth surfaces and crisp corners. This precision has made Sollas' machines a favored choice among high-end cosmetics producers. Remarkably, this benchmark of 160 boxes per minute is a recent achievement; until recently, the machines were limited to wrapping "only" 120 boxes per minute.
Engineering Manager Dirk Verbeek of Sollas faced the challenge head-on: "We aimed to increase production from 120 to 160 products per minute, but encountered hurdles. While the machine's mechanics could handle it, the packaging foil posed a challenge. We struggled to configure the control software to ensure even unwinding of the film." Upon hearing of the issue, Siemens Sales Manager Raimondo Hooft immediately thought of Siemens Technology, the central R&D department, where an innovative approach utilizing AI for optimized controls was under development.
Niklas Körwer at Siemens Technology eagerly took on the task of enhancing the machine's output. "We were already making strides in developing an AI model for control optimization and sought a machine builder to test it on the factory floor," he explains.
Eventually, a pilot project was initiated at Sollas, welcomed by Dirk Verbeek: "We believe AI will play an increasingly significant role in automation development. Rather than wait for its full development, we prefer to experiment now and lead the way."
The primary goal of this Sollas-Siemens collaboration was to implement AI-driven control optimization via a function block in TIA Portal, incorporating a neural network trained on the Digital Twin of the machine. This approach, utilizing reinforcement learning, swiftly identifies an optimized AI-based control without the need for additional data, significantly expediting the process compared to manual programming.
Upon successful training, the neural network was integrated seamlessly into the existing program on the Simatic controller, validated by Sollas through a blind test. Dirk Verbeek expresses enthusiasm: "The technician operating the machine was unaware of the AI-based update. The integration was seamless, and the film now unwinds more uniformly."
The throughput of the machine increased by 33% solely through software enhancements, with the AI-trained neural network deployed directly on a Simatic S7-1500 through the TIA Portal. This success serves as a stepping stone for Sollas, positioning the company as a frontrunner in digital transformation, as noted by Raimondo Hooft, Siemens' OEM Sales Manager in the Netherlands.
Looking ahead, Siemens and Sollas are exploring further AI projects, including developing a function block to minimize machine vibrations, as part of Sollas' roadmap to becoming an OEM of the future and a Digital Enterprise.