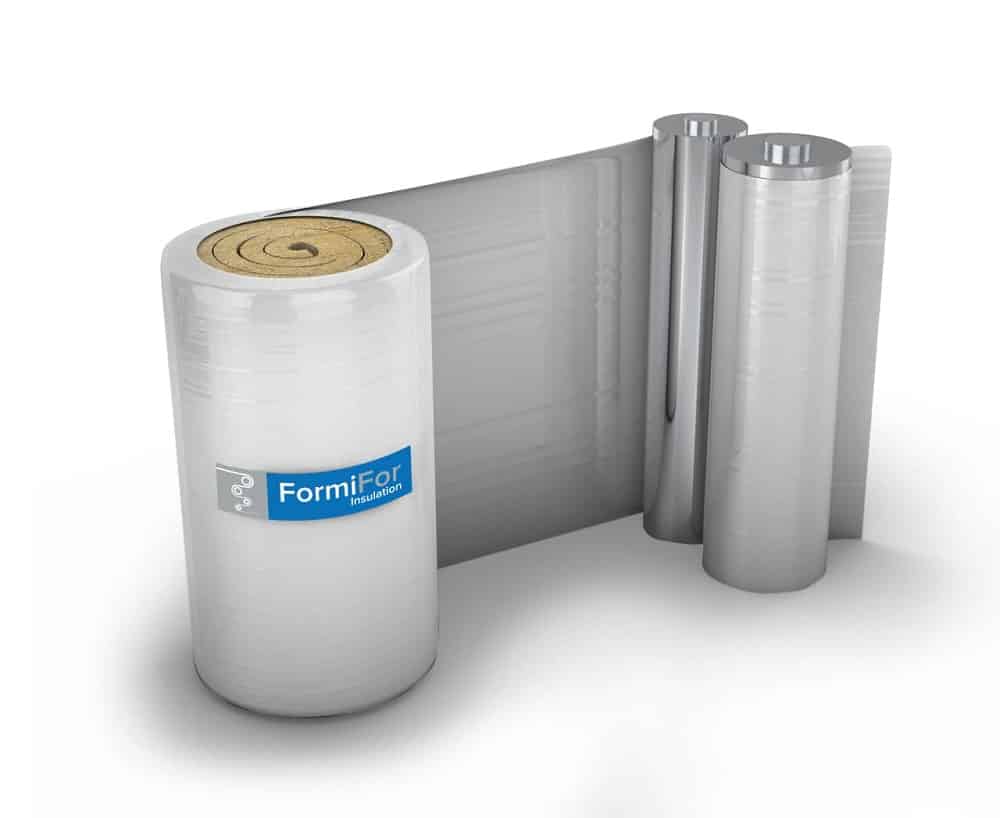
Working with some of the world’s leading Insulation companies to help them in meeting their sustainability objectives, Berry Global’s European flexible films business has launched a next-generation version of its top-selling high-performance FormiFor insulation compression film that now incorporates up to 30% post-consumer recycled material.
This latest addition enables companies to benefit from the many existing advantages of FormiFor while also being able to demonstrate a stronger environmental profile through the increased use of circular polymers. The film also demonstrates the commitments made in Berry’s Impact 2025 sustainability strategy to develop solutions that minimise a product’s environmental impact.
The new version of FormiFor which has received RecyClass accreditation to confirm the authenticity of the recycled content, contains up to 30% of Berry’s Sustane premium recycled polymer. Sustane polymers provide high levels of technical performance, consistency, traceability, and quality. This ensures that FormiFor continues to offer its high weld and holding force characteristics and can be printed in up to eight colours for high-impact and colourful decoration that maximises brand awareness and on-shelf appeal.
Berry is one of Europe's most experienced manufacturers of compression film. FormiFor has been developed to meet the exacting requirements of the insulation, glass wool and stone wool product markets. Its lightweight structure uses up to 50% less material in comparison with other traditional packaging films, thereby minimising the amount of packaging required for each application and further lowering the film’s carbon footprint. Equally important, the film is recyclable at its end of life. Each benefit being a key element of Berry’s Impact 2025 sustainability strategy.
FormiFor’s high compression rate means that wrapped products occupy less space, relieving warehouse and storage pressures and reducing transportation costs. In addition, the new recycled content version maintains FormiFor’s ability for more film to be wound onto a standard reel. This means fewer reels are required for each application, minimising downtime for reel changes and maximising productivity.
“In line with our Impact 2025 sustainability strategy, this latest version of FormiFor demonstrates our ability to design for circularity with a film that maintains all its benefits while helping our customers meet and exceed their sustainability goals,” commented Neal Geryl, Business Development Director, Berry Global.