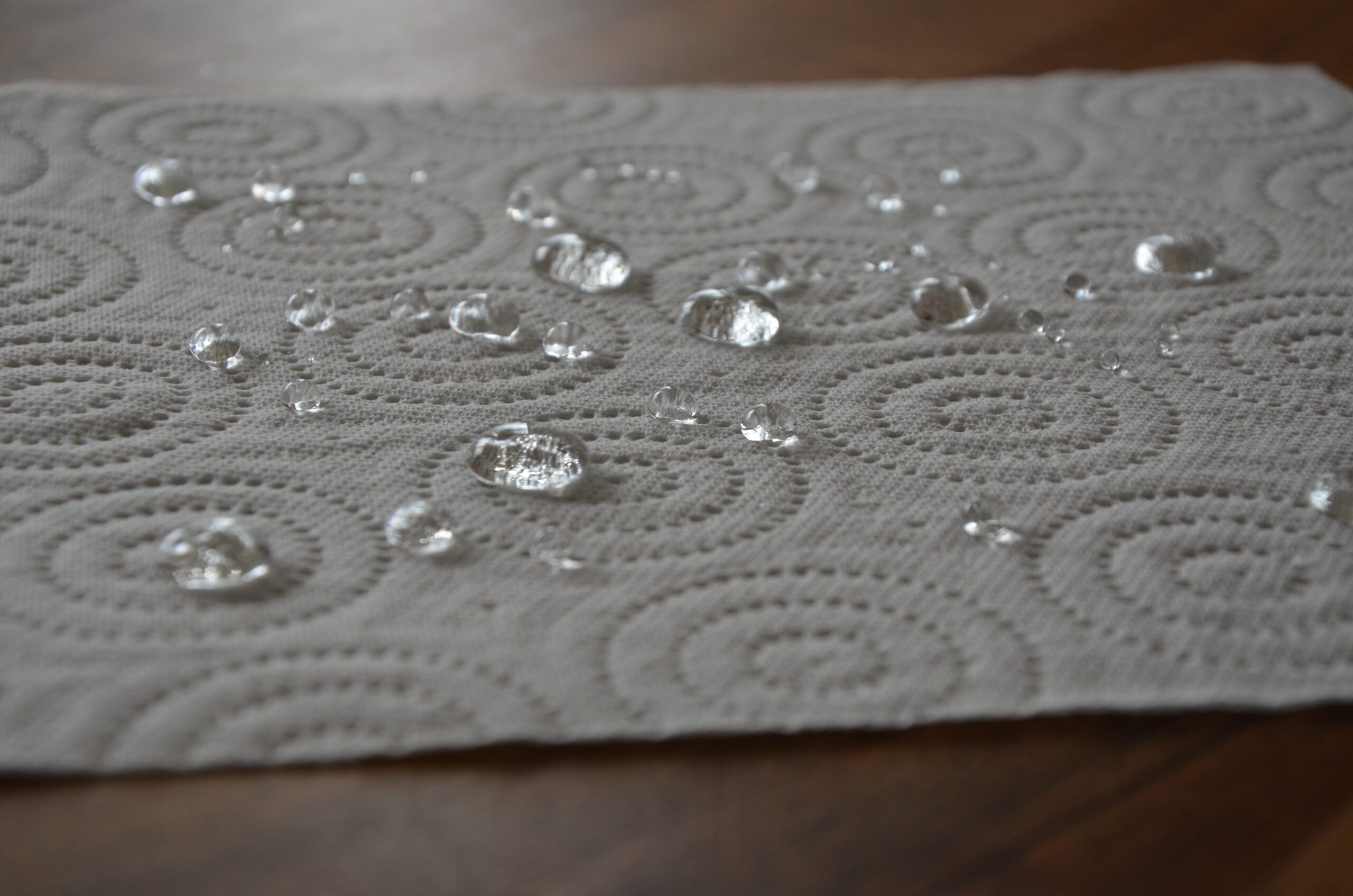
Olivier Muquet, Chief Marketing and Sales Officer explains the plastic-free solution sees cellulosic materials, such as paper, cardboard or moulded cellulose, coated with a thin layer of alumina.
"What makes us unique is the fact we have a process that brings gas barriers to all types of cellulosic materials, whether they are in rolls or have already been shaped as objects, such as trays while maintaining a high rate of cellulose after treatment. Our materials are still 99.9% cellulose after having been processed by us.”
A Thin-Film Deposition Technique
Launched in Grenoble in June last year, Cilkoa employs a technology called atomic layer deposition (ALD), which is familiar to microelectronic companies.
This is a thin-film deposition technique based on the sequential use of a gas-phase chemical process. Mr Muquet adds:
“At the origin of our creation, there was the meeting of two laboratories: one specialized in papermaking processes and the other in gas phase processes used in microelectronics. What provides the effective gas barrier is the alumina film that we can create on any fibre accessible to the surface of cellulosic materials. The thickness of this film is just a few tens of nanometers.”
Recyclable and Compostable
Alumina, also called aluminium oxide, is a synthetically produced aluminium oxide. It is used in ceramics and has other widespread applications in industry. It is also approved for use in items intended to come into contact with food.
The alumina film that is created on the surface of the cellulosic material does not affect the substrate that the company treats, Mr Muquet says.
“Apart from their reinforced barrier properties, the substrates maintain their flexibility, their printability, and their end-of-life properties. Thus a paper that is recyclable and compostable will remain so after treatment by the Cilkoa process. The first studies that we have been able to carry out concerning our low-temperature process show a very favourable carbon balance. We are also starting a complete approach to analysing the life cycle of the materials produced using our process.”
Packaging for Food and Cosmetics
Cilkoa has already been contacted by food and cosmetics manufacturers, but any product that needs to be protected from oxygen and/or humidity is of interest, Mr Muquet continues.
“We will have industrial capacities by the end of 2024 – it is on this date that the first packaging that has been through the Cilkoa process will come out. We are currently in the co-development phase with two types of players: packaging users, especially in the food industry, and paper processors.”
The aim, Mr Muquet concludes, is also to further enhance the process to make it suitable for an even wider range of applications.
“We are already working on adding new properties or improving our performance, such as making certain materials hydrophobic for instance.”