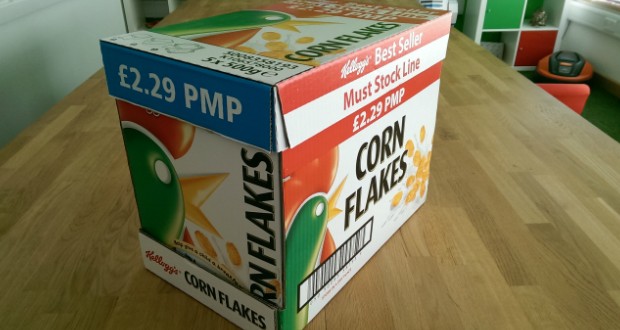
In addition to its enticing on shelf appeal, the practical benefits of this cost-saving solution made a stand out in this category. The customer historically packed their product in 10 count cases within their production plant. They then shipped cases to a co- packer to put the cartons into 5 count high quality printed sleeves which was then shrink wrapped.
The revised pack was designed to help streamline the supply chain which then reduced the packaging costs. The first step was to develop a case or sleeve which could be erected at the manufactures production plant with a 5 count without having to make any major changes to the packing machinery.
The solution was to use and adapted Saica Innovation Product PUSH. This pack is used to dispense products from the outer to the supermarket shelf in one operation and was the perfect solution for this product.
A die cut case was developed which worked with the current packaging machines, this has vacated the need for a separate operation in a co- packer and significantly reduced the operational costs for Kellogg’s whilst also making the product much easier to dispense at the supermarket front line.
This was an extremely successful solution and has now been rolled out over 5 product lines.