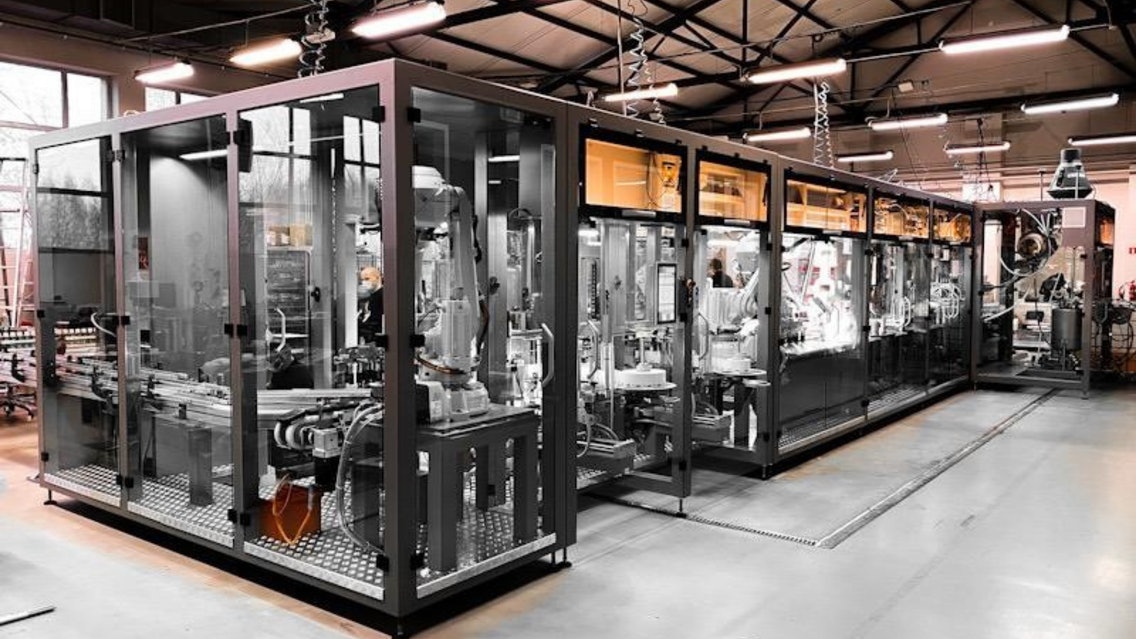
For CPGs hoping to launch new liquid products into industries like cosmetics, pharmaceuticals, and household chemicals and cleaners, highly customized or short runs have always been severely limited by cost and implementation times. Traditional customization methods made it unprofitable to release small batches.
Consider this scenario: The production department at a large cosmetics company at a manufacturing plant in the suburbs of a European capital takes a call. Someone from the marketing department is asking to order a small batch of shampoo for a promotional campaign. How big is the order? It’s quite small at only 5,000 units. That’s a problem in and of itself, but this marketing person is requesting a couple of changes, too, asking that the shampoo color be different, and filled into some custom bottles instead of the usual ones. Oh, and they’d also like to change the caps and the labels. And the deadline happens to be early next week.
These expectations wouldn’t sound acceptable to most CPGs. Unless the product is already waiting on the shelf at the warehouse, it’s simply unprofitable to apply so many changes to a well-oiled machine of a production line. At least, that used to be the case.
Today, Polish packaging machine builder Unilogo Robotics is trying to make these scenarios not only doable for liquid product CPGs, but downright practical. It’s Cleanline system, a new, fully automated packaging line based on B&R’s ACOPOStrak transport system, makes short runs with high variability possible, in fact they can be deployed extremely rapidly and provide unprecedented optimization performance with just a few clicks.
Pioneer and visionary in the packaging technology market
Unilogo Robotics is a medium-sized Polish OEM that designs and manufactures solutions for the cosmetics, chemical, and pharmaceutical industries, specializing in liquid product customization. According to it supplier B&R, the company’s machines and production lines are the embodiment of innovation in its complete form, and of true engineering panache.
“Initially, we provided services to large corporations moving their manufacturing plants to Poland,” says Tomasz Nowacki, founder of Unilogo Robotics. “After some time, large retail chains appeared, too, and began to roll out private labels. This changed the playing field: the market started to demand machines adapted to diverse bottle shapes, caps, and labels. At that time, we set ourselves the goal to create the highest-performing productive production line.”
The company also set itself specific objectives and targets for its lines’ productivity. Production batches are getting shorter and require constant machine changeovers, so Unilogo assumed that its line would always produce 12,000 to 15,000 units per shift, regardless of how complex the customer’s components (bottles, corks, labels) are and if changeover would be required one, two, three, or four times.
E-commerce standards in B2B
An approach that has become a standard now at the consumer level is one we’ve all become familiar within e-commerce: speed and flexibility of service are currently universally required qualities. Is this approach also penetrating the B2B market? Most companies still have a traditional supply and production chain in place, built for an outdated sales model based on holding expensive product in inventory. According to B&R and Unilogo Robtoics, though, today’s world demands immediate response and flexibility, a product-on-demand concept. Unilogo is preparing for such a revolution and is already gaining competitive edge by using adaptive manufacturing in its design process.
Thanks to Unilogo’s Cleanline, cosmetic, chemical, and pharma CPGs are able to implement production-on-demand, and the company says it will bring new dynamics into production and let their customers to realize meaningful savings in warehouse and product storage. Cleanline is an integrated system of robotic modules in the form of a compact production line, designed and developed in accordance with the Industry 4.0 concept. It includes a fully automated robotic production line for lotions, personal care products, perfumes, household chemicals, and similar liquid products, with changeover and start-up times of only a few minutes. Parts are 3D-printed to allow the line to work with any type of packaging and closure, and additionally make it possible to launch new packaging to the market within only a few days.
Click here to watch a brief video highlighting features and capabilities of Unilogo Robotics' Cleanline, particularly its use of B&R's ACOPOStrak transport system.
The biggest advantage of Cleanline is its flexibility, which is an extension of its modular design. The whole line is based on building blocks that can be easily combined and adapted to the needs of the individual business, as well as expanded with new modules. Cleanline includes a module responsible for sorting and capping. With 3D-printed parts, a dosing module, labeling module, and a module responsible for packing the units into corrugated shippers and placing them on pallets. A part of the module is connected with the ACOPOStrak intelligent transport system by B&R.
ACOPOStrak Intelligent Transport System
According to Nowacki, the innovation that makes Cleanline so versatile is the specially developed intelligent transport system. It is based on magnetic trolleys [also called movers in other linear servo contexts] that move along a magnetic track. The trolley shape makes it possible to handle and transport any pack type without having to perform a changeover. The core of the system is B&R’s ACOPOStrak technology. It shortens entire line considerably while making it extremely flexible and sustainable; particularly important for the calculation of capital expenditures.
The entire process takes place in an end-to-end system, without involving human operators or manual labor. What also makes Cleanline stand out is the fully robotic unpacking/packing module. A set of several robots autonomously unpack the pallets with the packaging units, as well as perform their blowing, laser marking, and feeding. Robots are also used at the final stage of packing of the finished products, and human labor is only required to transport the empty pallets and collect the loaded ones.
Capping Module Using 3D Printing
After seven years of experiments, Unilogo Robotics successfully developed a capping module that it’s really happy with. It is fully automated and uses 3D-printed format parts, allowing Cleanline to remain a 100% versatile machine, the company says. The whole system is efficient and optimized in terms of dimensions, occupying only 2.1 m of line length.
Cleanline as a whole complies entirely with the Industry 4.0 and Internet of Things (IoT) principles. This means, among other things, that the machine is coupled with a smart network. The entire process is very simple to control and monitor, and it can all be done in real time.
Control Panel, OPC UA, and Pack ML to Save More Resources
Cleanline is controlled using a universal HTML5-based panel. This solution makes sure that all process parameters can be changed from a single place. On top of that, the panel can be expanded by adding features required in the customer’s process, as well as personalized and adapted to the individual expectations, the standards adopted in the relevant manufacturing plant, or simply to the operators’ habits. Another advantage is the use of the OPC UA (Open Platform Communication United Architecture) technology. It makes it possible to monitor data, also in real time, and to access detailed reports, or even videos recording key process stages or emergencies. Data is stored in the cloud, maximizing working convenience and making it possible to control the whole process from any place. This solution also significantly facilitates repair and maintenance of the line as well as shortens the response time of Unilogo tech support in emergency situations.
A particular advantage of the line for businesses with more than one production device is its compatibility with the PACK ML system, providing time savings, working comfort, and software standardization. Unilogo Robotics’ initial goal was to provide a production line that would be able to unpack a pallet of empty packaging units, fill them, cap them, apply labels and pack them into boxes ready to be shipped to the customer, all done efficiently and involving as few people as possible.
“We believe that robotic Cleanline solutions will soon replace overly complicated and inefficient product customization and packaging systems,” Nowacki says. “The market’s future lies in flexible solutions enabling customization and series production in small batches. We look for companies that think like us and see this as their opportunity for success.” -PW