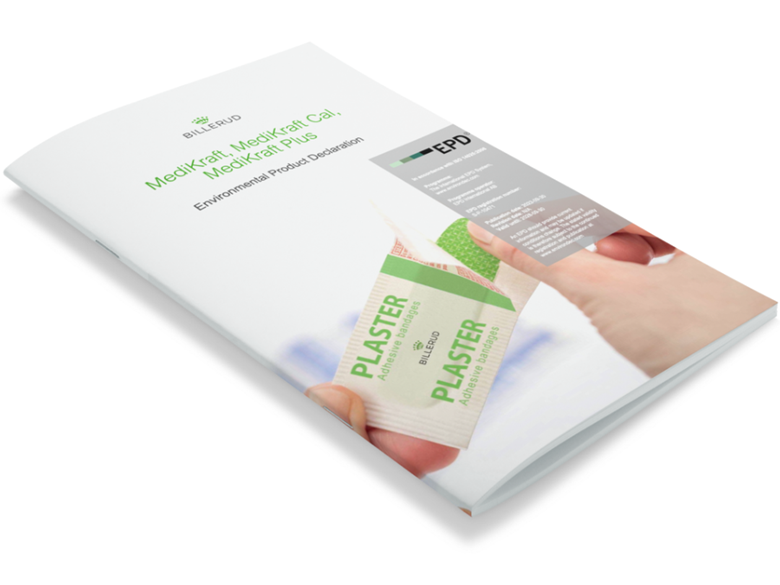
Billerud offers two main ranges of medical paper – SteriKraft, which constitutes ‘clean and safe’ microbial barrier paper for medical applications; and MediKraft, comprising of strong, high-purity papers for non-microbial barrier properties.
The MediKraft SealBase is produced at Billerud’s Skärblacka mill in Sweden. It is a 38gsm-grade paper designed to serve as a base paper for medical synthetic cold seal coatings.
Its purity is tested via controlled bioburden and cytotoxicity testing. Since it is free of OBA, latex, and recycled fibres, the paper’s high purity is said to improve the sustainability of the products in medical packaging applications.
At the same time, MediKraft SealBase is recyclable and is believed to emit ‘low’ levels of CO2 during production. Billerud claims it is the only company on the market to consistently produce and disclose Environmental Product Declarations (EPDs) for almost all its medical paper products, and it plans to do so for the entire product line.
The solution is also free of Optical Brightening Agents (OBAs), and Billerud uses in-house bioburden labs and advanced tools (e.g. Web Inspection Systems) to oversee the product’s quality. With integrated pulp production, the company aims to facilitate complete control of the manufacturing process.
Other testing covers such sterilization methods as E-Beam, gamma, EO, and steam to test wider compatibility with industry requirements and ensure product safety.
Additionally, the material’s strength is set to ensure its runnability and efficiency in the converting process, while its machine-glazed side is expected to improve printability.
“MediKraft SealBase demonstrates our commitment to the medical segment and providing innovative solutions to our customers,” says Robert Torstensson, vice president, Business Area Paper at Billerud. “This is a strategic step in broadening Billerud’s product portfolio in medical paper, allowing us to cater to a wider range of medical applications and customers seeking alternatives to traditional latex-based cold seal products.
“An integrated pulp production ensures complete control of the manufacturing process, supported by comprehensive quality control systems. MediKraft SealBase also offers a competitive edge through our advanced sustainability credentials, solidifying our reputation as a trusted partner in providing high-quality, environmentally responsible medical paper products.”
MediKraft SealBase is being displayed at COMPAMED in Dusseldorf from 11th – 14th November.
In a similar effort, Billerud previously worked with Moelven Wood to replace plastic shrink wrap with a paper-based packaging solution for its wooden interior panels. The solution was expected to help Billerud cut down on its overall carbon footprint.
Meanwhile, Syntegon’s paper-ON-form retrofit kit for cold-sealable paper packaging was nominated as a finalist in the Machinery category of last year’s Sustainability Awards. It enables users to transition away from plastics and run paper material on new and existing horizontal form-fill-and-seal wrappers.
More recently, Bayer and PAPACKS joined forces with their mutual sights set on biodegradable, fibre-based packaging for such consumer brands as Aspirin, Bepanthen, and Claritin. This is expected to help Bayer reach 100% reusable or recycle-ready packaging by 2030.