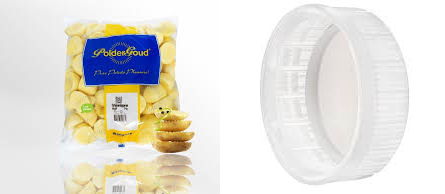
sustainable food and beverage production along with food and packaging waste reduction have become topical issues around the globe. Apart from an increased interest in food quality, the demand for environmentally friendly and bio-degradable packaging solutions has been on the rise. True to the motto “it’s cool to care”, today´s consumers request a green conscience along with their packaging. In its role as a leading international packaging manufacturer, Coveris is against this backdrop constantly searching for new processes, technologies and materials, aiming to further refine existing packaging solutions and develop new products.
“A particular focus lies hereby on the refinement and development of packaging solutions for the dairy and spreads industries that save material and improve the overall carbon footprint. Due to our continuous R&D efforts and product improvements, we are able to manufacture lightweight packaging solutions that reduce weight as a result of material reduction”, said Helmut Ruland, Director for Technology & Innovation, from Coveris Global Rigid.
One example are breakable, thermoformable sheets for Form-Fill-Seal (FFS) applications such as ECOCELL® as a result of a continuous development and improvement from solid to lightweight sheets. The latest sheet innovation is called NEOCELL® and was launched in 2014. This allows Coveris to offer to its environmentally aware consumers and consumer products manufacturer lightweight FFS sheets not only made of polystyrene (PS) but for the first time ever also made of polypropylene (PP). By means of this new technology, Coveris is able to produce innovative multilayer sheets for yoghurt multipacks with up to 26% weight reduction as a result of density decrease through the use of foamed materials in the middle layer, which consists of mineral fillers.
Furthermore, Coveris’ Injection Compression margarine tubs offer up to 20% material savings as compared to standard injection molded tubs. Material and weight savings are the result of an improved Injection Moulding technology, which is well established in the industry for decades.
In addition, Coveris has developed Compression Molded caps and closures for milk-based and other beverages that significantly outperform current industry standards. While two of the company’s more recent developments, the lightest dairy cap in the world and the lightest tamper-evident 38mm closure, weigh in with 1.2 grams and 2.3 grams respectively, the industry standard for the latest averages around 3.3 grams.
Besides its efforts to further reduce the weight of its packaging solutions, Coveris focuses its R&D competencies on replacing traditional raw materials with materials that are environmentally-friendly and renewable. On example of this is packaging made from renewable materials such as PLA (corn starch) or Green PE (sugarcane). Both materials are biologically degradable and complete Coveris’ broad range of sustainable packaging solutions in the food and beverage industries. By choosing FSC or PEFC certified papers, which are used e.g. for Coveris’ famous DuoSmart® cups, consumers are provided with environmentally-friendly packaging solutions from well-managed sources.