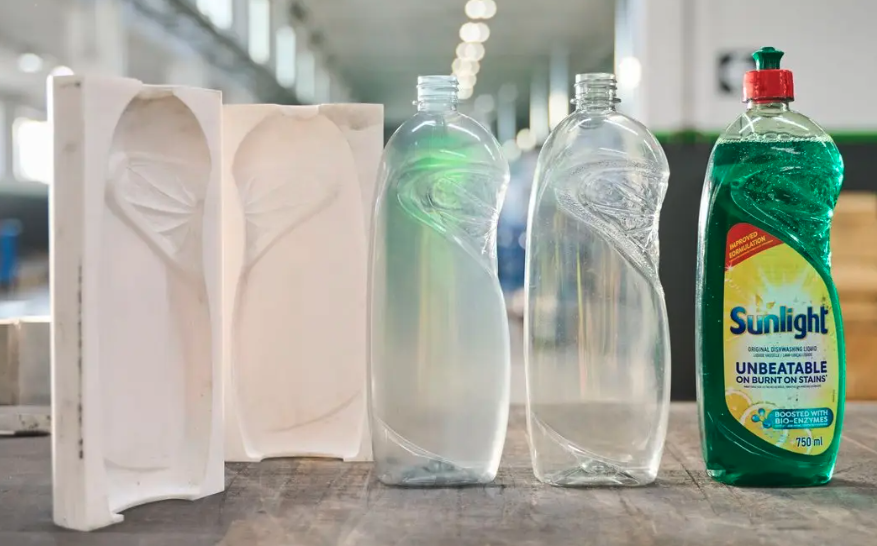
Unilever, one of the world’s largest fast-moving consumer goods (FMCG) companies, consistently pioneers new products across personal care, home care, nutrition, and other sectors. With renowned brands like Dove, Domestos, Cif, Knorr, Axe (Lynx), Ben & Jerry's, and many more, Unilever products are likely found in households globally. The FMCG industry, driven by constant consumer demand, demands ongoing innovation and adaptation in product strategies. Packaging design plays a pivotal role in consumer perception, alongside product quality. Brands like Unilever navigate considerations such as material efficiency, visual appeal, safety, and sustainability across diverse packaging formats and products.
Stefano Cademartiri, CAD & Prototyping Owner at Unilever, along with Flavio Migliarelli, R&D Design Manager at Serioplast Global Services, collaborated to explore the potential of 3D printed molds for low-volume stretch blow molding (SBM), streamlining prototyping and pilot testing processes. This partnership significantly reduced lead times by six weeks and costs by up to 90%.
Traditionally, the development and testing of new bottle designs followed a lengthy workflow. Plastic products, including food and beverage containers, cosmetic, and medical packaging, predominantly undergo blow molding, a rapid mass-production method with short cycle times, making it cost-effective for high-volume production. Three main blow molding processes exist: extrusion blow molding (EBM), injection blow molding (IBM), and stretch blow molding (SBM), commonly used for high-quality PET containers such as water bottles.
Serioplast, a global producer of rigid plastic packaging for FMCG, is a key partner of Unilever in developing and producing packaging for home and personal care markets, producing billions of bottles annually in various materials.
Traditionally, Serioplast utilized either 3D printed mockups or blow molding for prototypes. However, 3D printed mockups lacked the desired properties for consumer evaluation, while production-quality SBM samples required expensive metal tooling, prolonging lead times by six to nine weeks. Metal molds, typically made through CNC machining, incur substantial costs and lead times, either through outsourcing or in-house production.
Consequently, prototyping and pilot testing of blow molding parts in low volumes were economically unfeasible, necessitating extended timelines for final design decisions. This often resulted in outdated tooling and incurred costs for companies like Unilever.