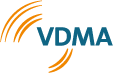
Düsseldorf, May 30th, 2016 – This drupa cannot be overlooked. This true-to-scale print of a drupa ricinus weighs 37 kg and has a size of 160 x 160 x 120 cm. The large-size sea snail is one of the thousands of prints produced with different 3D technologies which the Printing and Paper Technology Association within VDMA is presenting at the world’s leading fair for print and crossmedia solutions of the same name in Düsseldorf (hall 7A, B13).
The calcarous shell of the drupa ricinus has spikes on the outside to keep predators away. On the inside, its coils are very smooth, supporting a fast retreat in the case of danger. “This complex construction plan of creation has put high demands on us,” reports Rainer Gebhardt, project manager of the Additive Manufacturing Association within VDMA. In order to produce exact replicas of the snail housing, the Association’s members involved retraced in fast motion something that cost evolution more than a hundred million of years. “In a playful manner, our project shows that the most complex bionic constructions are realizable with additive technologies,” says Gebhardt.
Laborious path from computer tomography to 3D print
At the beginning of the process chain stood a computer tomography of the calcarous housing. The resulting digital “point cloud” then needed to be transformed into an STL file. The wide-spread data format of 3D print maps solids consisting of miniscule triangles. The team then needed to manually postprocess the transformation from the CT image into the STL file, as the young technology is still prone to faults, especially when it comes to complex shapes – open edges, holes, or uneven areas. The desire to label the drupas with continuous numbering turned out to be a challenge. After all, there is no suitable surface on the spiky, coiled snail shell, which is easily covered by a hand.
In the end, the team revolving around Hans-Jörg Hesser, CEO of the manufacturing and construction services provider Hasenauer & Hesser, managed to meet all challenges. They received considerable support by Materialise GmbH (Bremen) and the start-up 3yourmind (Berlin), among others. The team generated layering data (SLI data) from STL files including labeling. These files control the laser beam in laser sintering systems or in selective laser melting, where the laser builds components layer by layer out of plastics or metal powders.
Six different 3D printing technologies
With laser sintering, Hasenauer & Hesser has produced 2500 pieces of the drupa ricinus out of the synthetic polyamide: exact replicas with smoothly wound inner walls and a spiky shell. It is with the same input data that members of the Association have realized true-to-scale snails of diverse materials and sizes. For example, the systems manufacturers Concept Laser and Renishaw have produced steely drupas with their laser melting systems. The plastics machine manufacturer Arburg has used their Freeformer technology to build snails out of miniscule plastic drops. And out of the 3D data, 3D Fab produced colored drupa snails consisting of a gypsum-polymer mixture.