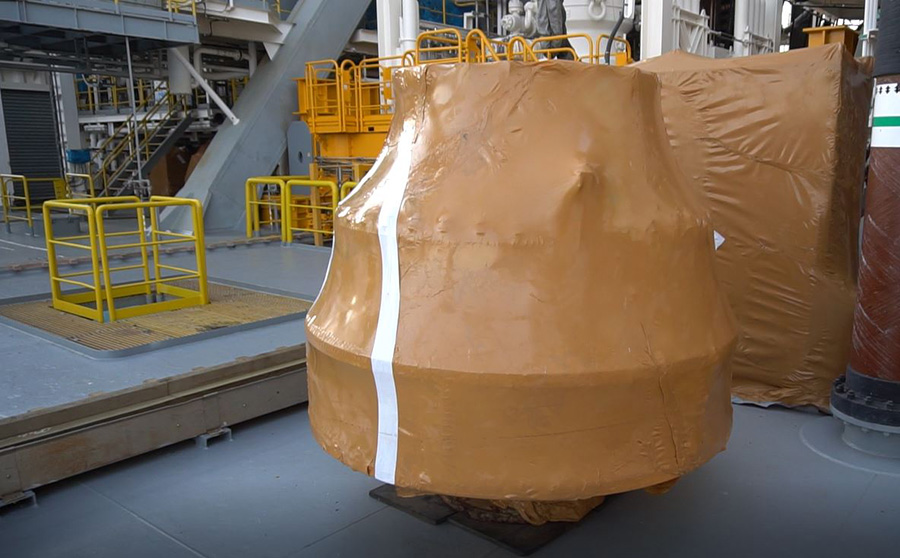
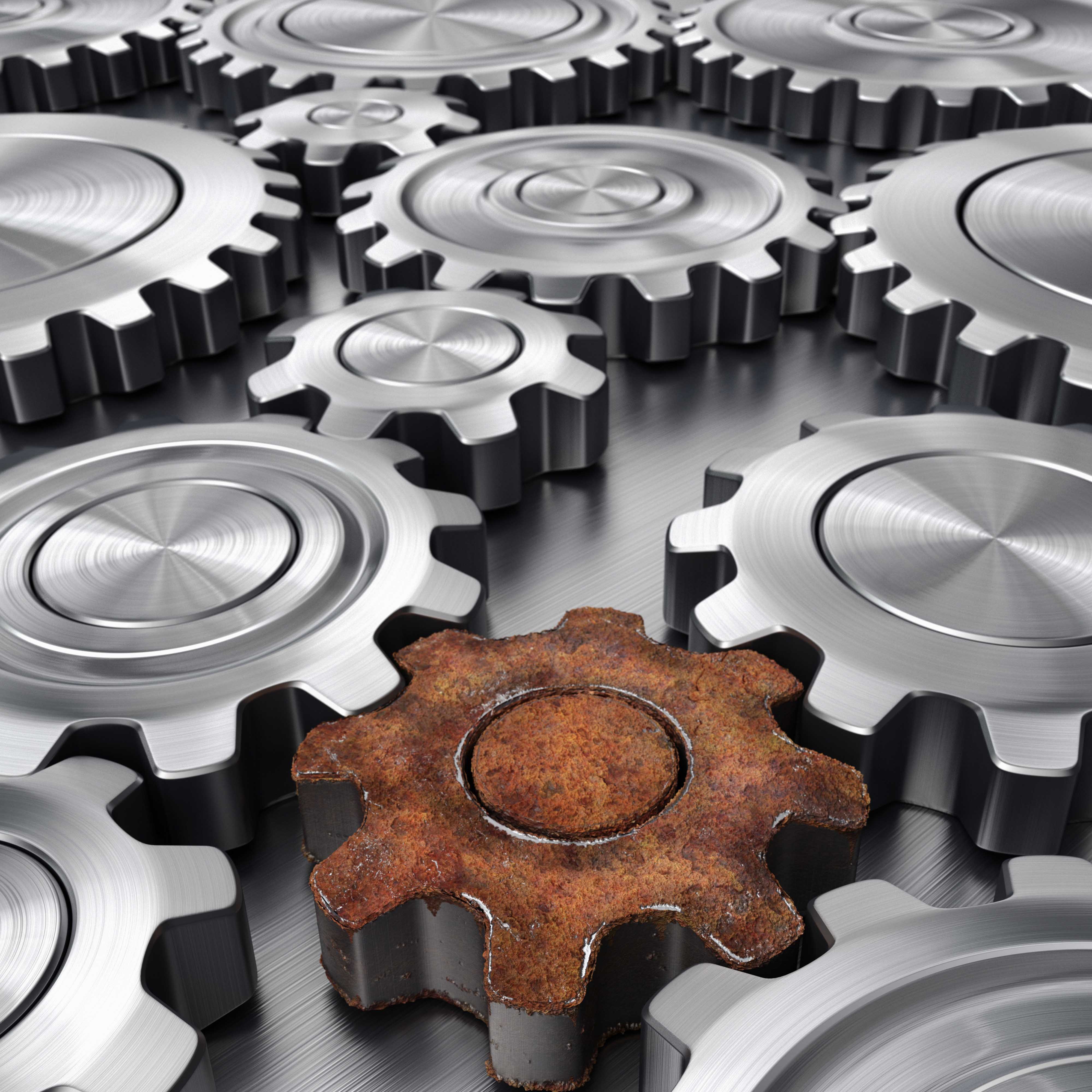
The global cost of corrosion was an estimated $2.5 trillion USD in 2016, according to a study published by NACE International. Allowing for inflation, that number could easily surpass $3 trillion USD today. Unfortunately, many are not aware of the high price tag of corrosion even for individual businesses and corporations. Cortec® Corporation therefore encourages manufacturers, maintenance managers, and other decision-makers to consider the potential cost of corrosion and take reasonable measures to avoid it.
Why Count the Cost of Corrosion?
Failure to count the cost of corrosion may leave manufacturers and facility managers blindsided by consequences such as faulty equipment, delayed production, and customer rust claims that must be made right. Furthermore, without counting the cost, managers may have difficulty getting the approval needed to budget time and money for corrosion prevention. Counting the cost of corrosion helps achieve both the motivation and approval needed to take corrosion protection measures.
Identifying Corrosion Costs in Manufacturing
Manufacturers who work with metal must beware of corrosion risks at every stage: receipt of goods, work-in-progress (WIP cycle), and export. Manufacturers can hope that suppliers will make good on any raw materials that arrive rusty on site, but they cannot make up for production delays or time lost negotiating the rust claim. In the WIP cycle, manufacturers lose time and sometimes metal when parts rust in between manufacturing stages and must be restored or scrapped. Export is even more dangerous. Unpredictable, fluctuating conditions inside a truck or shipping container may lead to corrosion from condensation by the time the customer receives the good. This is perhaps the costliest corrosion stage of all, as the manufacturer must remedy the damage done.
An example of how significant corrosion costs can be for manufacturers is apparent when calculating the price tag of a 1.5% economic loss due to corrosion at a hypothetical steel mill operating 24/7 and producing 100 ten-ton coils per shift, three shifts per day at a nominal material and manufacturing cost of $300 per ton. In only one week, corrosion losses could be near 100 grand. At a fraction of the cost, manufacturers could avoid most of this loss by implementing Cortec® VpCI® protective technologies and also avoiding the time lost for rework.
Hypothetical Steel Mill Cost of Corrosion at 1.5% Loss
Per Shift $4,500
Per Day $13,500
Per Week $94,500
Per Month $410,625
Per Year $4,927,500
Identifying Corrosion Costs on Greenfield Projects
New oil and gas facilities or other large-scale energy projects often take years to build. Meanwhile, custom assets shipped from afar may sit one or two years before being installed. With inadequate protection, the component may be rusty and unsafe by commissioning time. Replacement could not only cost tens of thousands of dollars, but the time and distance required to make and deliver a new part could significantly delay the opening of the project. In contrast, internal protection with CorroLogic® VpCI®-339 Fogging Fluid and external protection with MilCorr® VpCI® Shrink Film could easily save not only the cost of the equipment but also the cost of the production otherwise lost by a delayed startup.
Identifying Corrosion Costs on Spares
The energy industry and other industrial plants also need critical and operational spares that can be installed quickly and efficiently if a main component fails or needs repair. Unfortunately, it is not uncommon for large warehouses to be full of rusty spares that are in no condition to use at a moment’s notice. Even though some of these individual pieces may not cost much, the total cost of corrosion from lacking a clean spare can quickly add up to millions of dollars of lost production value from downtime, along with the cost of restoration and the intangible cost of safety issues that could arise from installing a faulty component. In contrast, a Cortec® restoration and preservation plan eliminates most of these costs and headaches with solutions that are easy to apply and remove.
It's Time to Calculate Your ROI!
Whether the calculation is done on paper or estimated mentally, counting the cost of corrosion gives a better picture of the importance of corrosion protection, allowing decision-makers to see the value of making a small relative investment in rust prevention to protect their bottom line. If you want additional guidance counting the cost of corrosion and factoring in the price of possible solutions, be sure to contact Cortec® for assistance.
Keywords: cost of corrosion, calculating corrosion cost, Cortec, preservation, WIP cycle, corrosion protection, corrosion on steel coils, oil and gas corrosion, critical spares, greenfield construction costs
Need a High-Resolution Photo? Visit: www.cortecadvertising.com
Cortec® Corporation is the global leader in innovative, environmentally responsible VpCI® and MCI® corrosion control technologies for Packaging, Metalworking, Construction, Electronics, Water Treatment, Oil & Gas, and other industries. Our relentless dedication to sustainability, quality, service, and support is unmatched in the industry. Headquartered in St. Paul, Minnesota, Cortec® manufactures over 400 products distributed worldwide. ISO 9001:2015, ISO 14001:2015, & ISO/IEC 17025:2017 certified. Cortec® Website: http://www.cortecvci.com Phone: 1-800-426-7832 FAX: (651) 429-1122