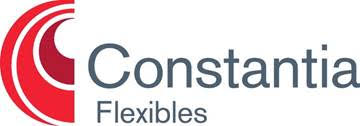
Constantia Flexibles has invested roughly €6 million in new technology to manufacture film-based flexible packaging at its site in Weiden, Germany. These investments will meet growing demand for specialty laminates such as stand-up pouches, with high property barriers, in the confectionery, processed food (coffee, dry food and snacks) and processed meat industries.
As part of the investments, Constantia Flexibles has installed two blown-film (polyethylene) extrusion lines. One line at the Competence Center Film develops in- house proprietary film formulations that enable efficient production and speed up the time-to-market. In addition, a second line produces pre-material for the Weiden plant and other film production sites in Europe. Constantia Flexibles already has several blown- film (polyethylene) lines in operation within its global manufacturing network.
In the coming months, Constantia Flexibles will also integrate an AlOx dual metallizer that will manufacture transparent, high-barrier film products that are catering for the latest consumer trends. The non-metal material is combined with additional barrier lacquers and films to create a barrier against aroma, moisture and oxygen, while the consumer is able to see the product inside the packaging due to its transparency.
“These investments mean we are now fully integrated into the film value chain at the Hueck Folien plant in Weiden and will strengthen Constantia Flexibles’ credentials as a leading supplier of high-performance films for different food industries,” said Stefan Grote, EVP Food Europe. “At the same time, our Ebert plant in Wiesbaden, Germany, will focus on being a leading manufacturer of film-based Twist applications for the confectionery industry.”
The research and development activities of the Competence Center Film, established in 2015, has already yielded its first success: “CompresSeal”, which was one of the winners of the German Packaging Award 2017 in the category Sustainability. New hot-embossing technology and an in-house engineered calander are used to create a film that has a higher seal integrity than standard polyethylene and weighs up to 30% less, while still having the same thickness as standard packaging. In addition, it ensures not only tighter packs, but also constant processing on packaging lines in winter and summer.