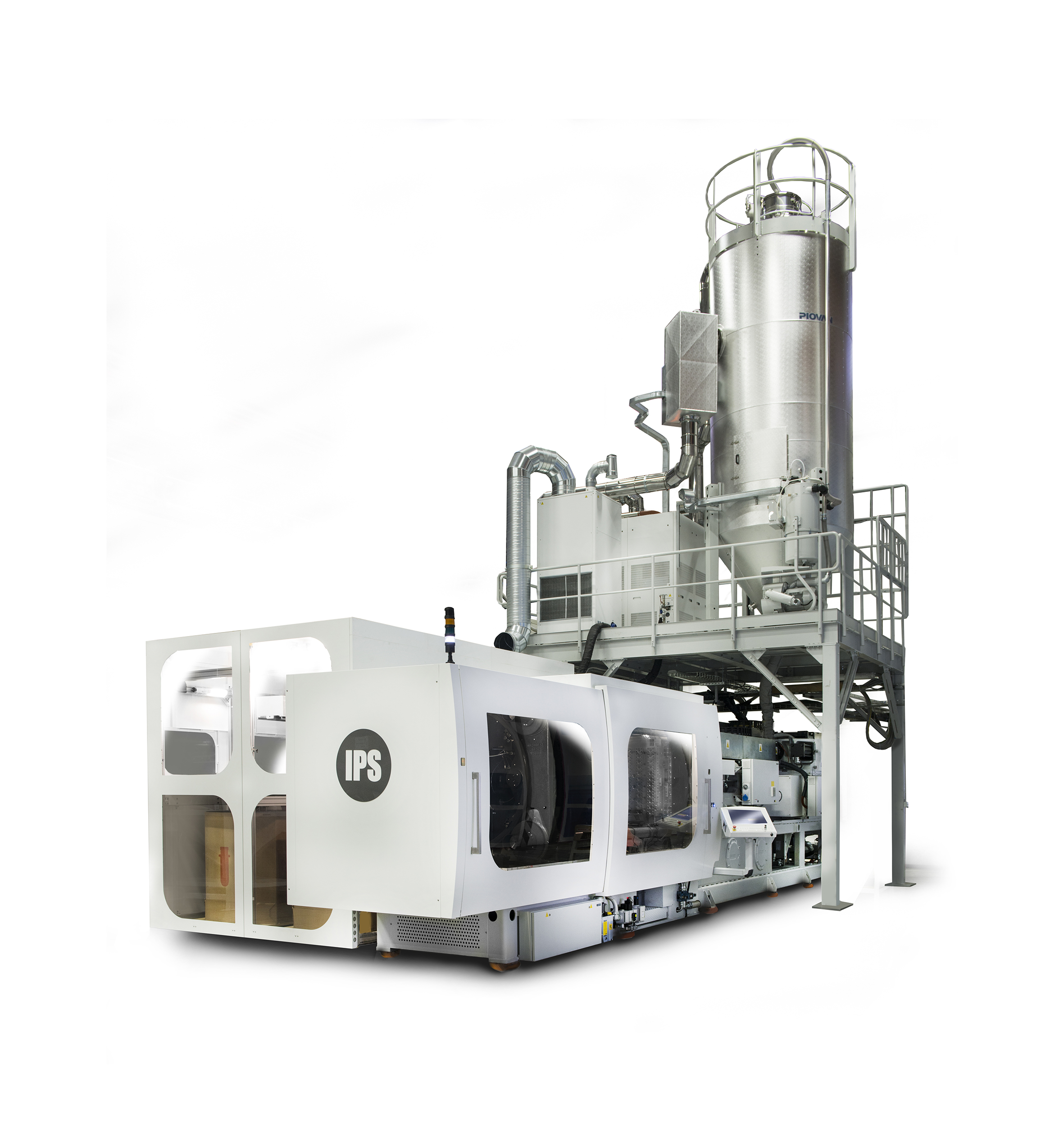
From automated, ultra-clean filling to a wide range of solutions for closure-making and control of every stage of primary packaging production: Sacmi is once again ready to impress at Latin America’s biggest beverage fair
The industry’s leading all-round plant engineer, the Sacmi Group is preparing for the 32nd edition of Fispal Technology, the international food & beverage processing, packaging and logistics fair (Sao Paolo, Brazil, from 14th to 17 June). The world’s third-biggest producer and consumer of beer and soft drinks, with investment in the industry estimated at over 10 billion dollars between 2015 and 2018 (source: National Bank for Economic and Social Development), Brazil is a strategic market for the Group. Consequently, Sacmi will be showcasing a broad range of high-productivity, highly automated, energy-efficient technological/plant engineering proposals at Fispal.
In this regard, complete filling lines designed by Sacmi to ensure a totally ultra-clean process and guarantee absolute quality even with delicate products such as wine, beer and CSD, are gaining ever-wider international acknowledgement and acclaim. What makes the difference is the high level of automation on the line, configured to combine pack forming, filling and case sealing all in one process – not to mention robot-aided finished product palletization.
In addition to complete lines for Bag-In-Box type packaging, Sacmi has also demonstrated its ability to combine effective solutions for the management of other pack types (such as beer in glass) with the returnable bottle system, with good feedback being observed on the Brazilian market itself: "Profitable activities on this market, where we’ve been operating for years with Sacmi do Brasil”, explains Iacopo Bianconcini, Marketing Manager of Sacmi’s Beverage & Closures Division, “has allowed us to expand into more complex areas, fielding projects with top bottling players, creating partnerships that have proved to be successful and clearly demonstrating, in the field, one of the Sacmi Group’s most distinguishing features: the ability to work alongside the customer right from the design phase with complete, customised solutions”.
There’s also plenty on offer for the closures sector: in addition to investment in ever-lighter, higher-performing plastic caps using compression technology, Sacmi will also be showcasing over half a century of know-how in crown caps and metal caps production technology, complete with closure decoration, embossing solutions. Then there are the modular labelling machines: these stand out on account of their unique efficiency and flexibility, applicable on multiple labelling systems. All this goes hand in hand with intense development work carried out in 2015 to perfect and expand the IPS (injection preform moulding) platform, currently one of the best solutions on the market for the production of PET preforms in terms of both quality and output flexibility.
Every stage of cap, label and primary packaging production is monitored thanks to hi-tech Sacmi vision systems that use HD image acquisition (we’re the world’s first company to equip its systems with cameras with a resolution of up to 5 megapixels) and advanced software to ensure total quality control of every part of the piece and so provide precious information on overall line efficiency.