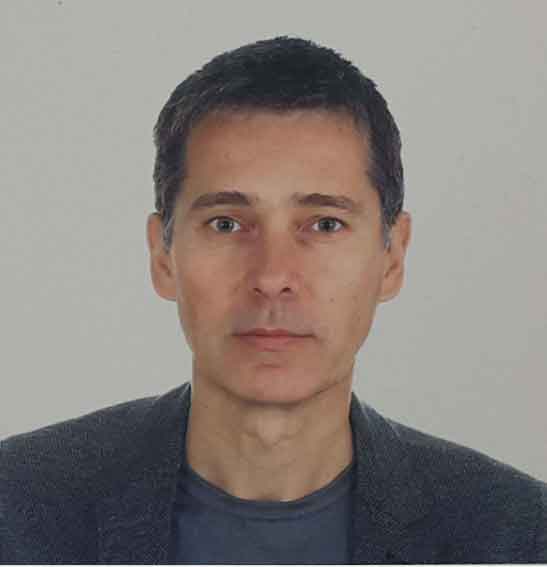
May 24, 2018 - KELENN technology in Antony, close to Paris, is specialised in fast inkjet printing systems, imaging systems and equipment for printed electronics. General Manager Didier Rousseau founded the company in 2005. In the interview he explains why his company invests half of its turnover in R&D, the visions that drive him, and how the sectors printing, imaging and printed electronics interlock with each other. The company is also member of the VDMA Working Group OE-A (Organic and Printed Electronics Association), which is in close contact with the Association Printing and Paper Technology.
Mr. Rousseau, would you like to give us a brief introduction to KELENN technology?
Didier Rousseau: Willingly. I set up the company just under 13 years ago. After starting out with industrial imaging systems, we then began to focus on specialising in inkjet printing systems and printed electronics. Today, we have 24 employees, a turnover of around 2 million euro in 2017 and we export 70 percent of our business. We invest 50 percent to 65 percent of our turnover in R&D - as well as any additional government funding we receive. Two members of our staff carry out fundamental research, six members carry out industrial applied research - in other words, they don't work at all on client projects.
How is turnover split across the three sectors?
Didier Rousseau: Last year imaging systems contributed around 35 percent to our total turnover, printed electronics around 15 percent and inkjet systems the remaining 50 percent. However, the ratio keeps changing; this also due to the fact that the printed electronics sector is currently growing by 400 percentannually.
What are the synergies between your imaging and printing systems?
Didier Rousseau: Half of our customers order printing systems with image processing modules and 90 percent of our image processing projects are linked to our printing technology. These systems verify, track and read printed information. We integrate our imaging systems with printing equipments from large companies such as Xerox, Ricoh, BoeweSystec and others.integrate our imaging systems into their printing equipment. Our inkjet systems are used mainly for customising and personalising direct mail and invoices as well as in the security printing sector. I am pleased to say they are also in growing demand in the packaging and pharmaceutical sectors as well as in other markets.
Your inkjet systems print on many different substrates - paper, cardboard, PET, PVC, metal...
Didier Rousseau: ... and thus serve the changing requirements of the market. Printing on paper is now only one discipline among many. In the future we will be printing everywhere - on all materials. We get enquiries from customers from all kinds of different industries. Especially customers who are not in the printing industry are looking for scalable systems that can easily be integrated into existing equipment. They want fully automated technology that delivers perfect quality at the touch of a button, while in terms of retrofitability takes up very little space. Our inkjet systems sometimes take up less than 50 percent of the space a competitor system needs.
What role do Print 4.0 smart solutions play?
Didier Rousseau: They are absolutely essential these days. In tandem with our imaging technology, we offer fully automated, networked and quality-assured systems. Since we develop our software ourselves, we were able to integrate monitoringof status, performance, print throughput, material consumption and -forcastas well as remote service options early on. Our systems report anomalies and errors automatically on their own. We work closely together with OEMs that adapt and integrate our technologies. We support them with our expertise, including new inkjet processes that are still under wraps.
How is your business with printing systems for mailing doing?
Didier Rousseau: Our solutions address a growing market segment. Personalisation and customisation are in great demand. The figures for direct mailing as a whole may have dropped as a result of digitisation but our inkjet printers provide customers with the necessary flexibility to print different thicknesses and sizes of envelopes at maximum speed and minimum costs - and personalise them at the same time. Y
ou promise high printing speeds with low printing costs but the costs in inkjet printing depend mainly on the inks.
Didier Rousseau: When it comes to quality, it is all about using the inks that are the most suitable, but that are as efficient as possible. Four of our staff work on matching our printing systems to inks as well as optimising their processing and we have entered into co-operations with ink manufacturers. The printing speed, inks and energy consumption are what counts in the print process - this means the efficient utilisation of time, energy and consumables. This keeps costs down and generates a genuine competitive edge for our customers.
Your KEOS inkjet systems print with up to 400 metres a minute. What is their main challenge for R&D?
Didier Rousseau: We need scalable architecture for software, electronics and printing technology. Only when they are designed from the onset for future scalability can the exponentially growing system complexity be brought under control. We have set up the system architecture with great precision - something that comes from my previous background. At EADS, I headed a laboratory that developed the most complex of systems. I learnt there to think through a development project from day one through to its long-term completion. Our research today will help our company in a few years to meet customer demands, which is why even as a small company we allow ourselves the luxury of 16 engineers in R&D. We want to continually better ourselves and offer the best available solutions.
What brought you to printed electronics: curiosity or strategic diversification?
Didier Rousseau: We as a company are pursuing a vision: printing technology of the future will not only be used for decorative purposes but will print more and more functions. The internet of things is growing. We will be living in a smart environment in which objects and devices will interact with us. Printed electronics can facilitate this interaction at a reasonable price but on a grand scale. This is why we see enormous potential in printing silver and copper nanoparticles and other active materials. We understand more and more how we can reliably use printing technology to work with them. Now we are ready to scale up.
You work in this sector with start-ups such as Genes'Ink and TriDinnov. How far advanced are these activities?
Didier Rousseau: Our inkjet printers for printed electronics are generating strong revenue growth. Independently from this, we are moving our cooperation with TriDinnov and Genes'Ink forward to create promising future technologies. TriDinnov focuses on combining 3D printing with printed electronics and is using our process for high-viscosity fluids with large copper particles for this. With Genes'Ink, we are promoting the EU-funded project "Clearsilver". The project focuses on using the inkjet process to print transparent, flexibly conductive thin layers to replace indium tinoxide, which is brittle and expensive. We have validated this new approach and are now building the appropriate printing technology on an industrial scale; our focus here is also on the three concerns - cost, reliability and speed. One great advantage of digital printing: circuit boards can be printed on demand and can be modified at any time during the production process. This is a paradigm shift in electronics production.
Can inkjet printing on paper help the development of systems for printed electronics?
Didier Rousseau: Our inkjet know-how is helpful - but in the end they are two different worlds with totally different requirements. To get more ink on the paper, you increase the amount of ink applied. In printed electronics, we need otherworkarounds to get the right result: chemical bonding of the substrate and functional ink or the application of inert gas to inhibit oxidation processes. Here we are also often only talking about nanometres. Paper know-how doesn't get you very far here.
Does printing electronics require a different inkjet technology?
Didier Rousseau: Our KEOS systems work with drop-on-demand (DoD) piezo print heads. We have totally modified them for use in printed electronics. Conductive inks make different demands on both the process and environment. We are able to ensure the right process conditions. In printed electronics, we also use our new DMD (Drop Material Deposition) technology. This is a completely different technology to DoD piezo technology and enables a wider range of inks to be used.
What role would you confidently expect printed electronics to play in your company?
Didier Rousseau: The current growth rates of 400 percent and the present-day increasing demand are encouraging. Reality is rapidly catching up with our original vision. Alongside decorative print products, functional or industrial printing is also gaining in importance and we will continue to step up our involvement in this sector.
Where do you see KELENN technology in 2030?
Didier Rousseau:Even more customers from all kinds of different sectors throughout the world will be using our systems because they are an optimal fit within their own value-added chain. We will be a team of a hundred highly qualified men and women developing innovative printing technology for conventional and functional inks as well as imaging technology. KELENN technology will continue to be a highly specialised technological company.