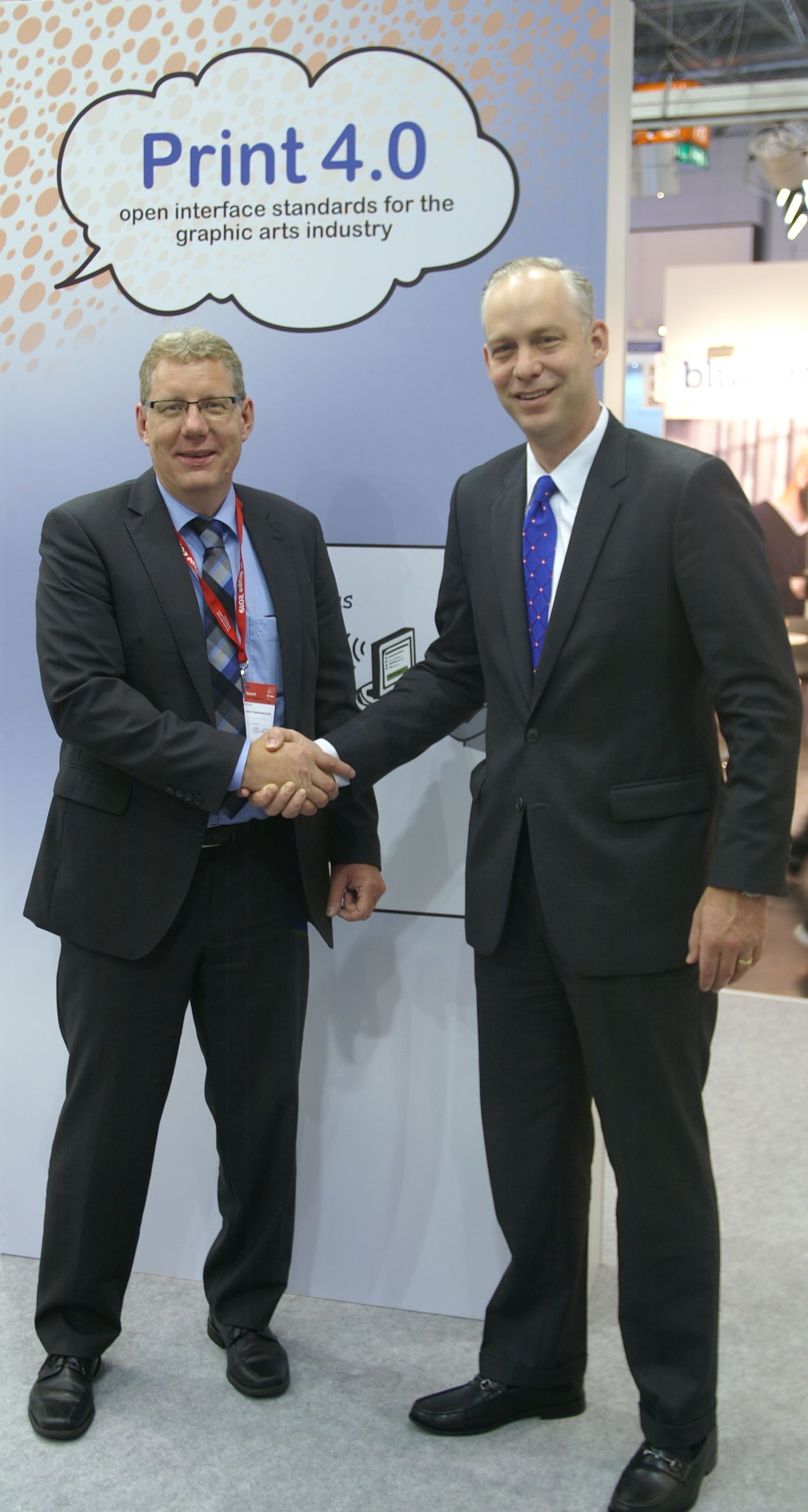
In this interview, Walter Kurz, chairperson of LEONHARD KURZ Stiftung & CO. KG, explains what can be expected of his company at drupa, andwhich role printed electronics and functional printing will play.
Mr. Kurz, industrial printing is a highlight of drupa 2016 – and an important domain of your company. What can visitors to the fair expect from KURZ?
Walter Kurz: We have our main stand in Hall 3 and are additionally represented even twice in Hall 12: In the drupa Innovation Park at the Touchpoint Packaging and at the stand of the Printcity Alliance, and at each booth we will show innovations from the fields of industrial and packaging printing. This alone shows the importance that we attach to this activity. Printing outgrows the purely visual and haptic aspects and fulfils a variety of functions – be it counterfeit protection, security features for banknotes or printed touch panels for household devices and for automobiles. This also includes our web-based identification, information and communication system "Trustcode". It enables users to access product data about metallized designs, holographic authenticity features or identification codes by smartphone. Finishing and function go hand in hand. At drupa, we will show new intelligent combinations of such stamping products and software from our affiliated company Adorsys.
Are there also some innovations from KURZ as far as graphic printing and packaging printing is concerned?
Kurz: Certainly. In our traditional sector – hot stamping – we present the M-series as a new product platform. It will significantly boost efficiency and flexibility. In the sheet and web fed cold foil transfer sector, we have made great progress with metallic enhancements in industrial printing. For that, we present new types of foils and the new “Distorun” module, which optimizes the positioning of cold foil webs. It not only enables to apply holographic single images and continuous designs more easily and precisely, but the foils can also be used much more efficiently, because the sections of the foil not transferred can now be used in a second and third transfer pass. Already now, the response we receive from the brand owners is great. In addition, we are also active with Print 4.0. In this respect, we show a new digital process management platform for hot stamping processes that networks the process chain for higher efficiency and productivity…
... and what about digital printing?
Kurz: That`s very important. We have refined our Digital Metal approach. This is a technique that combines digital print with a coating and metal transfer process thus enabling to produce short runs and personalized designs. To that, we have added a digital inkjet enhancement component, which makes our digital printing and foil application process with real metal fully online capable. This is an integrated holistic concept comprising the machine, software and foils from our company.
Industrial printing is a growth market. Will its importance increase in your company as well?
Kurz: Yes, that is a strategically important area. Nevertheless, where there is light, there is shadow too. To date, the high expectations have not been fulfilled especially as regards printed RFID chips and printed photovoltaics. The situation is, however, completely different in the Digital Metal area, the printed touch panels and sensors. Here, the intense preparatory work we have already done is paying off. There are many lucrative niches, but not every idea is a really brilliant one.
Where have successes been achieved in the industrial environment?
Kurz: At drupa, we present a Bosch washing machine with a touch display that has completely been produced by industrial printing. The advantages lie in the production process, the freedom of design, and it is possible to produce touch displays that are more robust. This is the kick-off model of a new series. We also receive positive signals from the automobile industry. With electromobility and automated driving, the design of the interior will change. Here as well, touch panels are up and coming. We have invested a lot of development work in that area and walked rocky paths. Now, the demand is rising. Whether this will also be the case in the graphic arts industry one day, remains uncertain. For that sector, there are still only a few isolated marketing activities.
Wafer-thin foils and coatings in the micrometer range are your specialty. Is nanotechnology needed in order to achieve such precision?
Kurz: Our origins lie in leaf gold; present day vapor plating is in the micrometer range. We develop coatings and foils. Nano technology is by no means new to us, but we don`t shout that from the rooftops. We use it in order to optimize the flow properties or brilliance of coatings and to produce ultra-fine structures. However, nano is not suitable as a marketing tool. It is a serious topic and requires consideration of many environment and safety related questions. As a manufacturer of coatings on a large technical scale, we can do that, and we actually do that. Thus, we save our customers a lot of expenses, and that is what we see as the right way.
New nano print processes reach the public`s attention more and more. Are you afraid of the competition?
Kurz: We welcome the highly dynamic development in functional and industrial printing. Since we are an innovative company, it is beneficial for us that our customers are open for innovations. Furthermore, the dynamic development gives reason to believe that the markets will continue to grow. We are happy to accept the competition, because we are convinced of our solutions. Our customers and our success confirm that we are working on the right research and development issues.