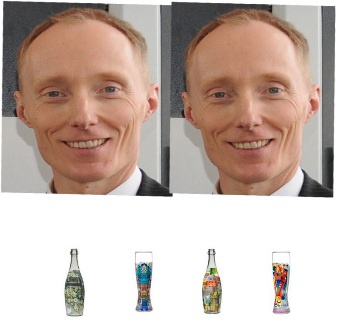
24/07/17 Industrial printing is omnipresent in everyday life.In a loose series of interviews, the VDMA Printing and Paper Technology Association presents member companies that are active in this segment.In this interview, Dr. Christian Maas, one of the two Managing Directors of KBA-Kammann GmbH based in Bad Oeynhausen, explains the importance attached by his company to industrial printing, which markets are in the focus and which technological challenges need to be overcome.
Dr. Maas, what is your understanding of “industrial printing”?
Dr. Christian Maas: I would draw a dividing line to graphical printing. In this sector, the printed product is the actual product. Industrial printing, on the other hand, is normally part of a multi-step industrial productionprocess within which its task is to decorate products, to enhance the appearance of them and to add information.
What are the sectors of industrial printing you are active in as a technology manufacturer?
Maas:Our core business is the decoration of primary packages –above all bottles – for the beverage industry;especially high-quality alcoholic beverages. Furthermore, we manufacture technology for printing on glass and crockery, hence, all sorts of tableware. Our third pillar is the decoration and enhancement of glass containers and flacons for alcohol-based cosmetics and perfumes. Whenever alcohol is involved, direct printing on glass is the better solution compared to labels or packages made of plastics.
How do the customers’ requirements differ from the traditional print market?
Maas: There are above all differences when it comes to substrates.Usually, we print on three-dimensionalcontainers made of glass or glass-like plastic containers in sizes up to 50x50x50 centimetres. In comparison with paper and cardboard, the surface qualities of glass differ substantially.The tolerances are often in the millimeter range. Moreover, the shapes and sizes of the glass containers are not standardized. Just think of the large variety of flacons or the different whisky and cognac bottles.In order to nevertheless achieve the required print quality, exact guidance of the substrate and precise process monitoring is essential.
Which printing methods are on your company`s priority list in industrial applications?
Maas: Above all, we focus on screen printing and digital printing as well as hot-foil stamping on hollow containers.In some cases also pad and flexo printing. In most cases, our customers use UV curing inks in the screen and digital printing systems. For that, we provide the correspondingUV technology. In screen printing, however, many customersalso use thermoplastic or ceramic frit inks. They are dried in down-stream oven lines.
Do you have to handle new substrates, inks and paints?
Maas: Increasingly there are also glass-like plastics that need to be printed on directly. However, apart from a few exceptions, the plastics industryrather prefers labels. That`s where we were also active in the past; now, we focus completely on direct decoration.Mainly on glass, but also plastics and already shaped metal containers, for instance, three-piece cans or deep drawn aerosol cans. Sometimes it`s also about the decoration of ceramics: individually printed coffee mugs or promotional items.
To which extent does industrial printing contribute to your total sales?
Maas: To 100 percent.We are solely and completely active in this segment.
Market studies forecast strong global growth for industrial printing. Does the experience you have made confirm these high growth expectations?
Maas: This may well seem to be true for technology manufacturers seeking to re-orientate themselves from the media to the packaging market. We experience strong and dynamic growth in digital packaging printing; as far as other processes are concerned, the development is, however, rather moderate. There is a continuous upward trend. The drivers are the global growth of population and the growing middle classes in the emerging countries because of the positive economic development there. Besides that, the trend towards sophisticated, high-quality packages is favourable for us.Especially in the luxury segment, for instance, as regards spirits or perfumes, the appealing look of the product and package design is an important tool to stand out from competitors.Packaging designers focus increasingly on the possibilities offered by digital printing.
Does your company push on with development work in the future areas of printed electronics, printed bio / medical technology or 3D printing?
Maas: We were active in the field of printed bio and medical technology when we still built machines for label printing. However, sales were not sustainable. At the moment, this is not a relevant future field for us. Its market potential is overestimated at least by one, if not two magnitudes.For printing technology manufacturers, I see relevant sales potentials neither in printed electronics nor in printed bio and medical technology. Things are different with 3D printing, talking of which we primarily mean printing on three-dimensional containers. To us, additive manufacturing is only interesting from the user`s perspective. We already use numerous printed parts in our machines. Partly in order to produce complex components, partly also in order to produce spare parts that are seldomneeded.