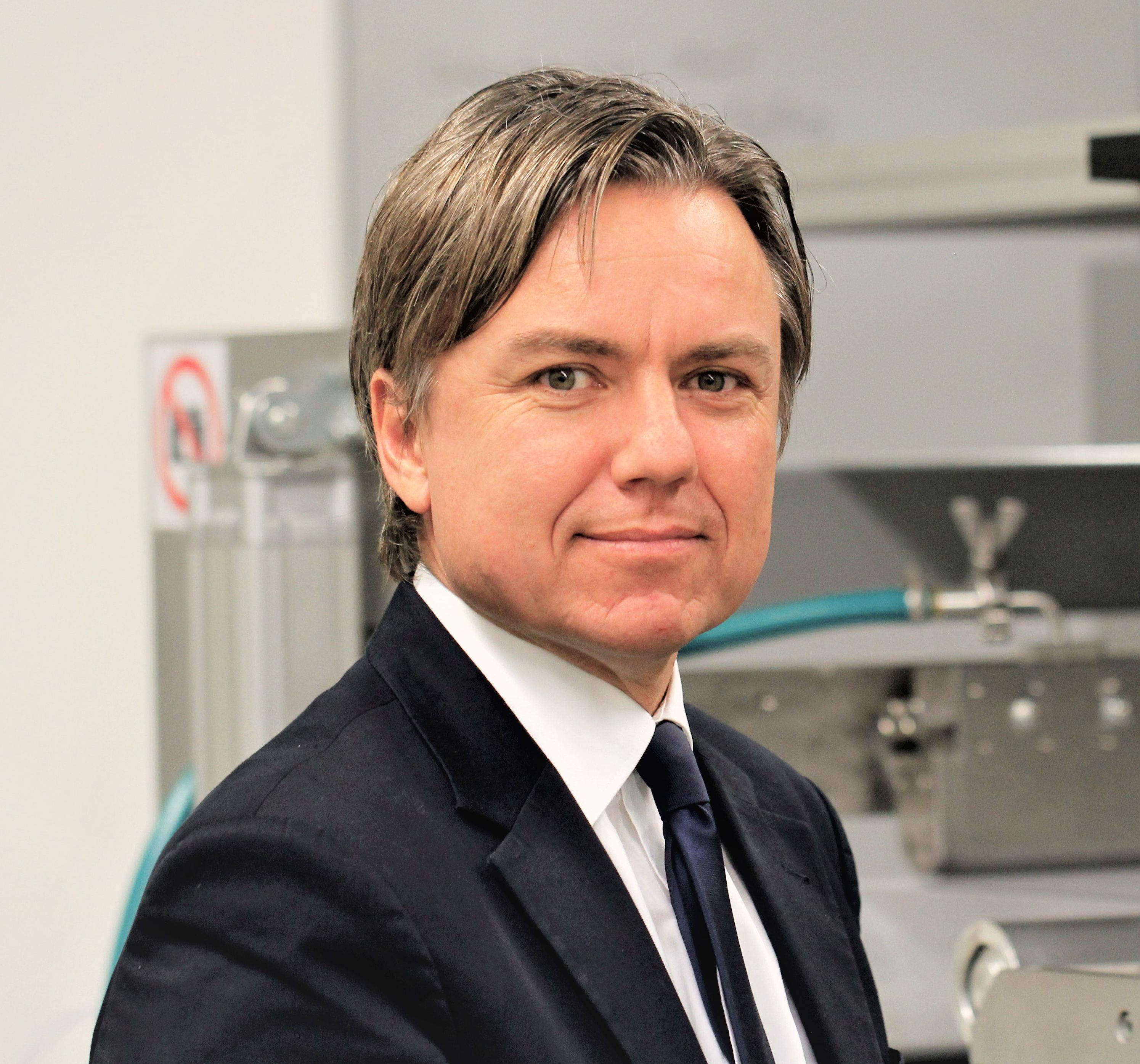
August 24, 2017 Industrial printing has become ubiquitous in everyday printing. In an occasional series of interviews, the VDMA German Association of Printing and Paper Technology shines the spotlight on the active players in this market. In our latest interview, Frank Schäfer, Sales Director of the Hamburg company KROENERT GmbH & Co KG, talks about the significance of industrial printing for his company, growth opportunities in this young market and the challenges in processing unfamiliar substrates and printing materials. The company is also member of the VDMA Working Group OE-A (Organic and Printed Electronics Association), which is in close contact with the Association Printing and Paper Technology.
Mr. Schäfer, what does the term "industrial printing" mean to you?
Frank Schäfer: Printing in this case is one stage within a larger manufacturing process. It usually involves printing on untreated or specially treated large-scale materials - such as paper, polymer films or metal foils. The printed substrate then undergoes further processing. We're talking about decoration, the application of product information or the printing of functions. For instance, in printed electronics functional coatings are printed to produce circuitry, sensors, data memory or electrochromic and electroluminescent effects. In addition, in biotechnology and medical technology active substances can also be printed. Industrial printing does not result primarily in print products, rather it prints to lend products certain functions.
In which industrial printing sectors is KROENERT active?
Schäfer: Our core business is building and developing coating systems. We have long been supplying flexo printing units with these systems as standard components for reverse side logo printing, such as for silicone papers or self-adhesive products. At the same time, we are driving industrial printing forward as a potential growth segment, focussing especially on printed electronics. It can be physiological data capture in medical technology with printed sensors, for example. In business and logistics, it's all about printing smart, tamper-proof packaging with sensors that give information on the delivery and cold chain, or smart labels for near field communication (NFC) which producers of premium spirits are already using today. If you place your smartphone near the bottle, without touching, you automatically get information on the product. Leading manufacturers use our machines to produce such smart electronic labels, chips and sensors. KROENERT machines are also used in organic photovoltaics or the coating of battery electrodes or fuel cell stacks.
In what way do customer needs differ from the classic print market?
Schäfer: In printed electronics, we have to deal with entirely different specifications. Production usually takes place in clean rooms, which naturally means our machines must not contaminate through dust or other particles. It's harder to meet the precision levels than in conventional printing, too. In process chains, different printing processes are often used for different coatings. And functional coatings are usually thicker than standard printing inks.
Which printing processes does your company use for industrial applications?
Schäfer: We can use screen printing, flexo or gravure, or, if the customer asks for it, digital printing, too. The real challenge lies in the diversity of these processes and their workflows. We have to integrate the various printing and coating modules together with the convection, UV or infrared drying modules in the chain - and keep to the required precision in the roll-to- roll process from start to finish.
You probably come into contact with other substrates, inks and pigments, too?
Schäfer: Exactly. We print mostly on polymer films, on which, for example, silver- or carbon- based conductive inks, insulating layers or adhesives for lamination are applied. Although temperature-stable foils are usually used as substrates, changing between cold printing and hot drying phases can create problems. The foils are under thermal stress and shrink in the process, not only lengthways but also in width. The trick is nevertheless to guarantee the required precision. To ensure the customer can successfully manage this, we carry out complex test series in our Technology Centre and get our material suppliers and customers involved in these tests.
To what extent does industrial printing contribute to your overall turnover?
Schäfer: As of yet, it's unfortunately only in the single-digit percentage range. However, we've started early and are involved in most of today's on-going projects. Frequently as a plant manufacturer - or at least on an informal basis. Today our machines are installed in start-ups and in global companies. They are designed for industrial use and we are ready and waiting for when the markets pick up speed. When the electric vehicle market starts to take off in Europe too, we have technologies, for example, for equipping battery factories.
Market studies indicate global growth opportunities in industrial printing. Would you in your experience agree with such high expectations?
Schäfer: Considering market predictions, we hoped growth would be faster. However, in the meantime there is a market for printed chips and smart labels. The automotive industry uses printed circuits, and the demand for OLED monitors and OLED wide area lighting is continually growing. These are the markets that will make headway. In addition, in the next few years it's anticipated there will be huge growth in organic photovoltaics (OPV). However, by the usual standards in coating and printing systems manufacturing, the areas for printing are smaller. Today's systems run at 15 metres a minute with working widths of 500 mm. That's not a lot for printing presses. However, when you print chips, sensors or labels, you're talking about many thousands per minute. Up to now, demand has come from the high-price segment with low volumes. And so for the moment it's the chicken and egg scenario: When demand grows, the prices per unit in printed electronics will fall due to economies of scale. But at the moment the price per unit stands in the way of mass application. That won't stop us, however, continuing to view industrial printing as a future market with potential, and continuously further developing our technologies.