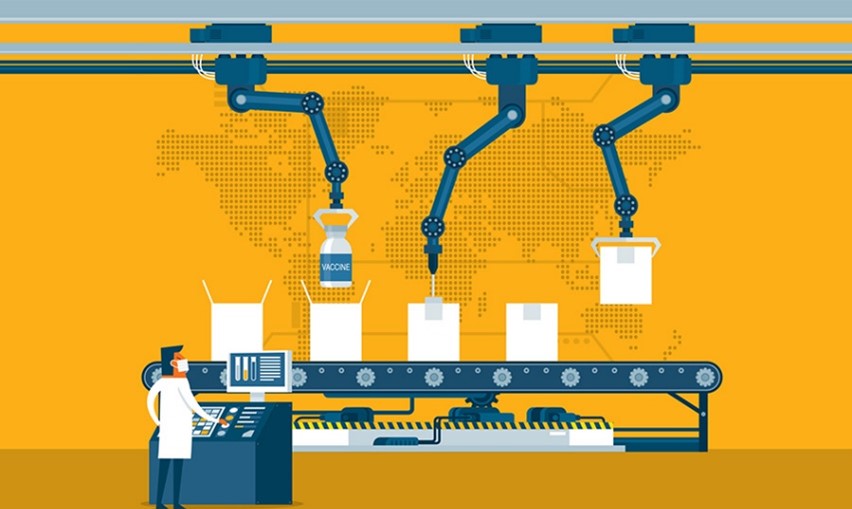
Packaging Machinery: Back to Basics
Deciding what packaging machinery to install in the production space is a crucial step in product manufacturing. While picking specific machines, equipment, and layout as well as the size of the workforce factors such as economic efficiency, room for growth, and level of automation need to be considered.
In this blog, we will discuss the questions machine manufacturers and packaging specialists, together, must ask in a specific order to design and set up the best possible product floor based on their requirements.
What exactly is the packaging required for?
Knowing the contents of the packaging use, design, and quantity help determine the kind of filling machine required for the line. Extensive details of the design also help determine the sealing (or capping) equipment as well as the labeling machinery.
What is the production requirement and are there any capacity restrictions?
The operational hours of the manufacturing unit as well as the required production rate determine the speed and thus the efficiency of the packaging line. Any economic restrictions to buy higher-grade machinery will also be considered in this step. Once calculations are made, the level of automation can be decided upon.
What makes this step tricky is the additional variable of expected growth. The equipment installed should provide room to increase the production rate as the company grows and the economic feasibility of upgrading the machinery in the near future should also consider.
How much area and manual labor is available for the facility?
To finalize the layout of the production floor, it is important to have a floor plan for the facility and also know how much labor is available to support the automated processes. Knowing the size of the workforce is important in determining the secondary equipment used at the facility. These including loading turntables, case packers, pallet wrapper, etc.
Besides the consideration of the above-mentioned factors, what comes first and foremost is ensuring the safety of your workers which requires conducting a risk assessment at beginning of your procurement process. Risk analysis should also be conducted periodically to ensure that standards are being upheld.