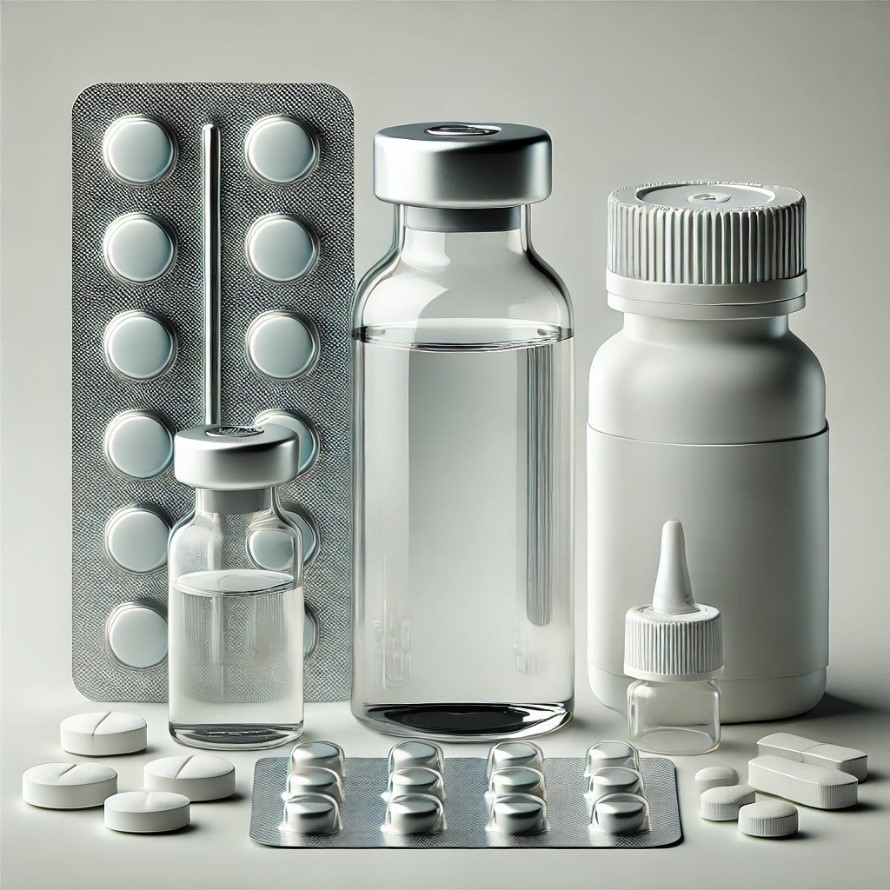
Pharmaceutical Packaging
In the pharmaceutical industry, packaging is not just a matter of convenience; it plays a crucial role in ensuring the safety, efficacy, and stability of the products it contains. Among the different levels of packaging, primary pharmaceutical packaging is the most critical because it is in direct contact with the drug or medication. This blog will explore the types of primary pharmaceutical packaging, their significance, and how they can be improved to meet the evolving demands of the healthcare industry.
Blister Packs
Blister packs are a common form of packaging for solid oral medications such as tablets and capsules. They consist of a cavity made from a formable web, usually made of plastic, and a lidding seal of aluminum foil or plastic. Each cavity holds a single dose, providing a protective environment against moisture, light, and air.
Advantages:
- Protects individual doses from contamination.
- Enhances patient compliance with clear visibility of remaining doses.
Challenges:
- Limited protection against light and oxygen for some sensitive drugs.
- Difficult to use for elderly patients with reduced dexterity.
Bottles
Bottles are widely used for liquid medications, such as syrups, suspensions, and solutions, as well as for tablets and capsules. They are typically made of glass or plastic, with an airtight screw-on or snap-on cap.
Advantages:
- Suitable for a wide range of dosage forms.
- Provides good protection against moisture and contamination.
Challenges:
- Glass bottles can break easily, leading to safety hazards.
- Plastic bottles may interact with the drug, causing leaching of chemicals.
Product Highlight: Rochling’s Round Bottles for diagnostics and analysis
Years of experience have given Röchling Medical proven expertise in developing and manufacturing high-quality plastic primary packaging for the pharmaceuticals, diagnostics and life sciences industries. The company’s own internal R&D department develops, supports and implements customer requests from the very first sketch right down to the finished product.
Vials and Ampoules
Vials and ampoules are small containers used for injectable drugs. Vials can be made of glass or plastic and are sealed with a rubber stopper and metal cap. Ampoules are typically made of glass and are sealed by melting the glass at the neck.
Advantages:
- Excellent protection against contamination and degradation.
- Suitable for sterile products.
Challenges:
- Glass ampoules can be difficult to open, posing a risk of injury.
- Potential for interaction between the drug and the rubber stopper in vials.
Product Highlight: Yukon Medical’s ViaLockTM
Yukon Medical’s ViaLok Non-Vented Vial Access devices are used to access standard drug vials for needle-free drug preparation and administration.
Sachets and Pouches
Sachets and pouches are used for single-dose applications, often for powders, granules, or liquid formulations. They are made from flexible materials such as laminated films.
Advantages:
- Lightweight and easy to transport.
- Good barrier properties against moisture and air.
Challenges:
- Difficult to open, especially for patients with reduced hand strength.
- Potential for contamination during opening.
Tubes
Tubes are primarily used for semi-solid formulations like creams, gels, and ointments. They are made from plastic, aluminum, or laminated materials and feature a cap that can be screwed on or flipped open.
Advantages:
- Easy to dispense the required amount of product.
- Protects the contents from external contaminants.
Challenges:
- Not ideal for products sensitive to air once opened.
- Potential for residual product remaining in the tube.
Opportunities for Improvement in Primary Pharmaceutical Packaging
Enhanced Barrier Properties
Current Challenge: Some drugs, especially biologics and other sensitive formulations, are highly susceptible to degradation from exposure to light, oxygen, and moisture.
Potential Improvement: The development of advanced materials with superior barrier properties can help extend the shelf life of these products. For example, multi-layered laminates or high-barrier films could be used to create blister packs or sachets that offer better protection.
Smart Packaging
Current Challenge: Ensuring patient adherence to prescribed medication regimens is a significant challenge, particularly for chronic conditions requiring long-term treatment.
Potential Improvement: Smart packaging solutions, such as RFID tags or embedded sensors, can monitor when a dose is taken and send reminders to patients. This technology can also track temperature and other environmental factors, ensuring the drug remains effective throughout its use.
Regulatory Compliance
Current Challenge: Pharmaceutical packaging must comply with stringent regulatory standards across different regions. These regulations cover everything from material safety to labeling, traceability, and child resistance.
Potential Improvement: Companies can streamline compliance by adopting standardized packaging formats that meet the highest global standards, reducing the complexity of navigating different regulatory environments. Additionally, investing in robust quality control systems and digital solutions for tracking and documentation can ensure that packaging consistently meets regulatory requirements. Automated systems that integrate real-time monitoring and reporting can further enhance compliance by quickly identifying and addressing potential issues before they reach the market.
Business Processes and Cost-Effectiveness
Current Challenge: Advanced packaging solutions can be expensive to develop and manufacture, which can increase the cost of the final product. Inefficiencies in business processes can also lead to delays, errors, and increased costs.
Potential Improvement: Optimizing business processes through lean manufacturing principles and adopting scalable packaging solutions can help reduce costs and improve efficiency. For example, modular packaging lines that can quickly switch between different formats or product types can reduce downtime and increase flexibility. Standardizing components across product lines can also lower production costs and simplify supply chain management. Incorporating predictive analytics into business processes can help anticipate demand, optimize inventory, and reduce waste.
Automation and Digitalization
Current Challenge: Manual processes in packaging can lead to inconsistencies, errors, and slower production times. This can impact product quality and increase the risk of non-compliance with regulatory standards.
Potential Improvement: Implementing automation in pharmaceutical packaging lines can significantly enhance efficiency, consistency, and accuracy. Automated systems can handle tasks such as filling, sealing, labeling, and inspection with greater precision and speed than manual processes. Additionally, integrating digital technologies like IoT (Internet of Things) and AI (Artificial Intelligence) can provide real-time data analytics, allowing for predictive maintenance, continuous improvement, and real-time adjustments in packaging operations. Automation can also play a crucial role in ensuring traceability and anti-counterfeiting measures, which are critical for regulatory compliance and patient safety.
User-Friendly Design
Current Challenge: Elderly patients and those with disabilities often struggle with packaging that is difficult to open or manipulate.
Potential Improvement: Designing packaging with ergonomic features, such as easy-grip surfaces or pop-open mechanisms, can make medication more accessible. Child-resistant packaging can also be improved by balancing safety with ease of use for adults.
Sustainability
Current Challenge: The pharmaceutical industry is under increasing pressure to reduce its environmental footprint. Traditional packaging materials like plastic and aluminum contribute to waste and environmental pollution.
Potential Improvement: The development of biodegradable and recyclable packaging materials can help address these concerns. For example, plant-based plastics or compostable films could replace conventional materials in blister packs and bottles.
By embracing these opportunities, pharmaceutical companies can lead the way in innovation while maintaining the highest standards of quality and compliance, ensuring that their products meet the needs of a global market.