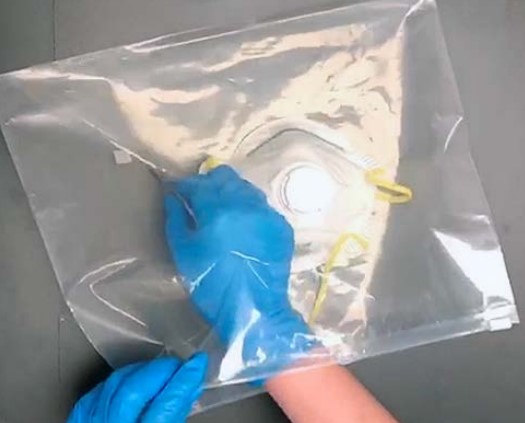
In this simple disinfecting process, the N95 mask and a small strip of Aptar’s ActivShieldTM are placed inside any commonly available one-gallon plastic bag. The strip releases a controlled amount of chlorine dioxide inside the sealed bag to decontaminate the N95 mask. The process takes only three hours until the mask is ready to wear again. It can be performed on-site at the local hospital where the mask is being used. Aptar has submitted its safety and effectiveness data to the FDA for EUA review. The company is working to provide approximately four million ActivShield strips per week and is working to expand its production capacity with the intent to deliver ten million per week by the end of April. “We are extremely encouraged by the promising data generated so far and are eager to deliver this technology to the front line and support the fight against the pandemic,” said John Belfance, President of Aptar CSP Technologies. If the FDA approves the EUA, then ActivShield will immediately become available for this important use. Chlorine dioxide has been widely used as a disinfectant in different industries, including the paper industry, drinking water treatment, food processing, and medical equipment. Aptar’s delivery mechanism uses the disinfecting properties of chlorine dioxide in a controlled sustained release within a contained volume. This innovative patent pending technology can efficiently and effectively disinfect N95 masks used by healthcare workers and first responders. “Aptar’s technology provides a unique, simple, and effective way to help solve the critical problem of PPE shortages we’re currently facing,” said Stephan Tanda, Aptar President and CEO. “We are aiming to provide a solution that is not only fast, but it does not require special equipment or training, making it potentially accessible to the wider healthcare community. This could enable healthcare workers to retain and disinfect their own facemask, helping to maintain continued proper fit to their face.”