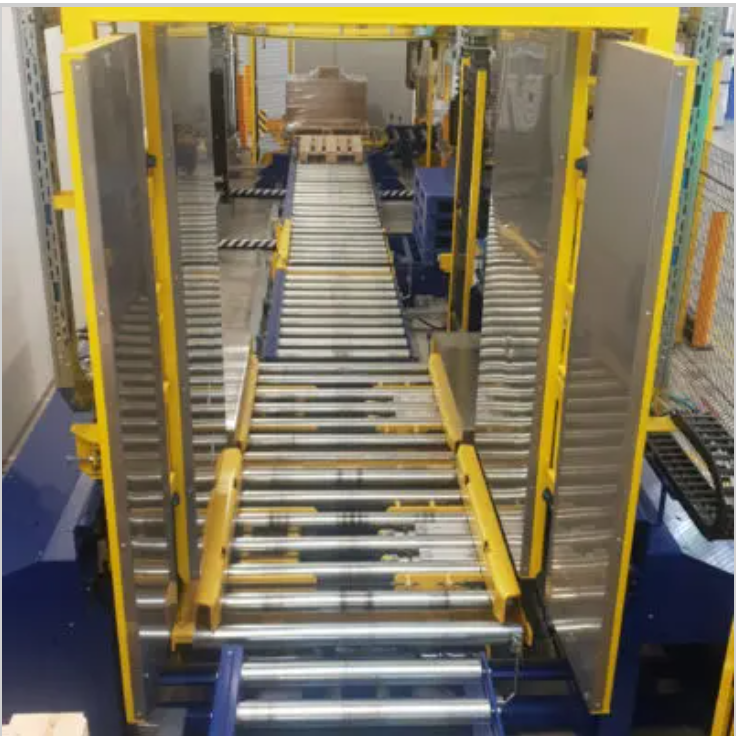
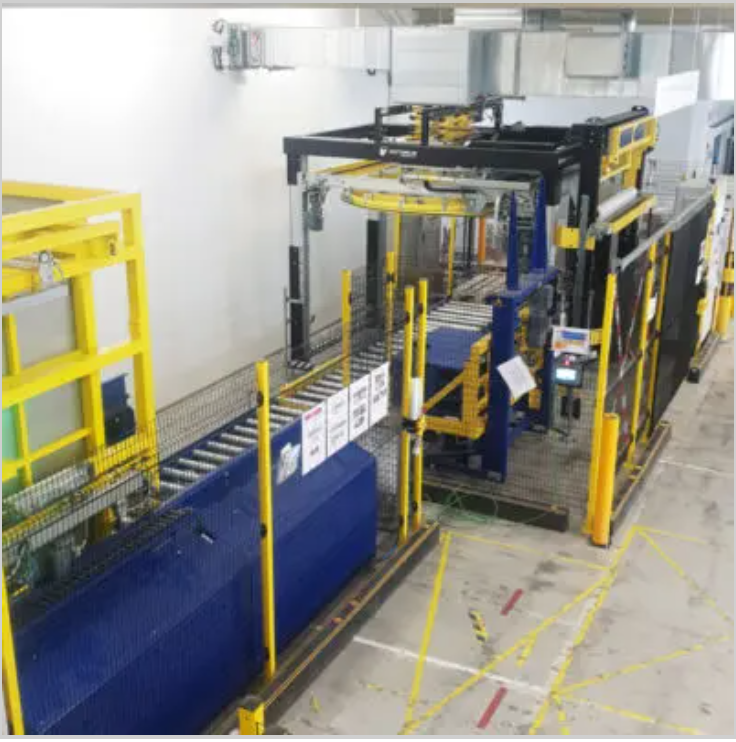
The Baust team recently accomplished a demanding project in the vicinity of Geneva, meeting stringent requirements for quality, safety, and ergonomics in automated processes. The challenge extended to precise planning within a complex room layout, navigating various mechanical and electrical interfaces. The project primarily focused on optimizing core processes related to pallet changing and wrapping within the logistics operations of a Swiss pharmaceutical producer.
To ensure a secure, gentle, and swift transfer of loads between plastic and wooden pallets, a pallet changer employing a push-over process was implemented. The system's ingenuity allows for a reversible change, maximizing flexibility. Fully automatic magazines handle the unstacking and stacking of empty pallets before and after the changer, achieving impressive throughputs of up to 60 pallets per hour.
In addition, an integrated winder plays a crucial role in enhancing outgoing goods packaging. This high-performance winder, directly connected to the system, eliminates the need for manual winding using standalone turntable devices. The result is a significant reduction in stretch film consumption by up to 50%, along with the elimination of rework and returns associated with incorrect manual winding. The stretch ring wrapper's performance is further complemented by an integrated cover film dispenser, ensuring dust-tight wrapping of the load.
The entire system is seamlessly connected by a well-planned and customized conveyor line. Feeding lifting stations reduce loading heights, enabling the use of low-floor vehicles like hand pallet trucks. Barcode scanners read labels, automatically identifying the required mode of operation, whether it involves passing through without changes or executing specific modifications. The project showcases Baust's commitment to tailored planning and innovative solutions in tackling intricate logistical and operational challenges.