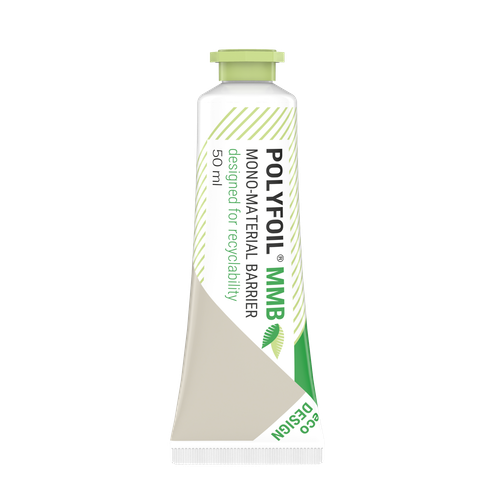
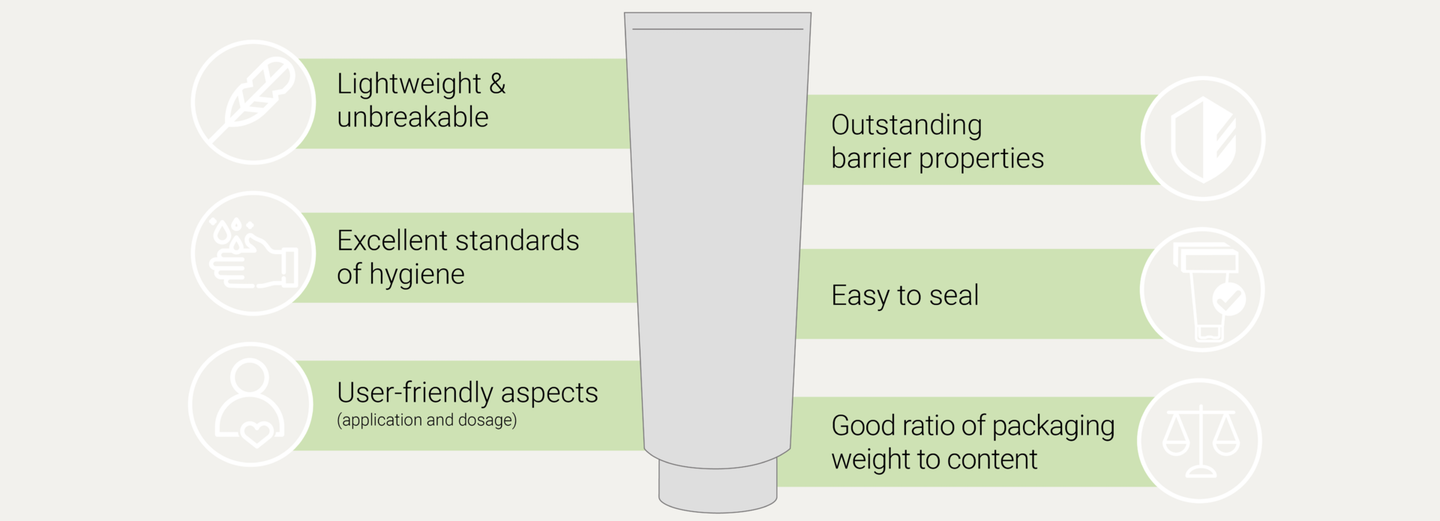
Neopac’s goal is to create tubes that simplify recycling–a crucial aspect of next-level sustainability practices. The EU has announced elevated targets for plastic packaging recyclability, aiming for 50% by 2025 and 55% by 2030. Other geographic areas have introduced similar targets, challenging packaging manufacturers to utilize innovative materials and embrace leaner production and logistics initiatives. Meeting these targets will require increased cooperation between all actors involved in the life cycles of plastics. Over the long term, modernizing and harmonizing systems for waste management is inevitable; in the nearer term, however, eco-minded advancements in the ways plastics are designed and produced are a must. Need for mono-materials Multi-layer aluminum-barrier packaging is particularly problematic for recyclers as, among other challenges, it is incompatible with mechanical sorting techniques. Because of this, each year packaging comprised of multi-material plastics causes one million tons of waste in Europe alone. Neopac’s push for mono-material tubes will employ sound packaging science to align with current recycling practices and processes, while providing its cosmetics, food and pharma customers with strong barrier properties to protect sensitive products. Slated for market launch later this year, the new portfolio of tubes, called Polyfoil® MMB (mono-material barrier) will be almost entirely polyethylene (PE) based, containing less that 5% of foreign materials (inks, adhesives, etc.) to avoid disruptions in existing recycling processes. Neopac is aiming to spearhead the application of new barrier technologies, including highly oriented PE barrier films (MDO), thin film ethylene vinyl alcohol (EVOH) layers, barrier lacquers and ceramic barrier films. In addition to product protection, the Polyfoil® MMB tubes will offer broad options for appealing aesthetics. Notably, the tubes will incorporate metallized tube body options owing to an ultra-thin “sandwich layer” that, in terms of recyclability, is widely accepted. White and transparent versions also will be available. Due to the reduced overall wall thickness, the lightweight tubes will offer as much as 40% tube body weight reduction compared to standard Polyfoil® tubes with aluminum barriers while keeping very similar haptics. Neopac also is currently conducting tests to convert caps from PP to PE, which is another goal being explored for the near future. “The push for enhanced recyclability is undeniable, with nearly 9 in 10 Europeans worried about the impact of plastics on the environment while only 5% of plastic materials are currently being reused,” said Martina Christiansen, Director Sales Tubes Neopac. “Technology must play a role in meeting higher recycling standards, and mono-material barrier tubes will represent a sizable step forward in packaging science.” Neopac has consistently focused on the packaging sustainability movement. The company recently released a Tube Design Guide for Recyclability. The company also offers an EcoDesign portfolio, primarily for cosmetics and personal care applications, that includes: • Recycled Tube featuring 75% recycled, “food-grade light” compliant polyethylene plastics; • Sugarcane Tube, made from renewable raw materials and offering the same characteristics and processability as fossil-based polyethylene; • and PICEA™ Tube, comprised of 95% renewable material in the tube body and shoulder–including 10% of spruce wood from wood waste in sawmills.