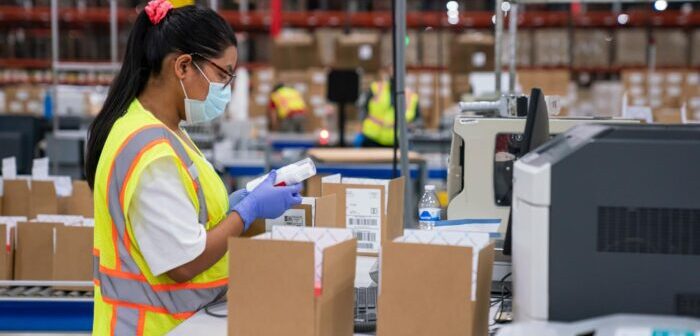
The AI-powered OptiCarton system helps to optimize the filling of boxes from a pre-configured set of cartons and can even suggest splitting an order into several consignments to make individual shipments more cost-effective or to reduce their carbon footprint.
With OptiCarton, DHL is not only responding to the current shortage in cardboard boxes and packaging materials in the market, but initial pilots also indicate that the solution offers customers additional benefits in the shape of shipping-cost savings of up to 35%, and with an average saving of 15%.
Dietmar Steins, executive vice president Global Solutions Design at DHL Supply Chain, said, “Even though this kind of solution might sound relatively simple at first, providing packing instructions for individual e-commerce shipments in real time is actually quite complex. We are excited to offer a fully automated software solution that can help our customers optimize the utilization of existing pack sets with the power of AI. Based on the products, volumes and sizes in question, the software not only suggests the optimal size of the outer packaging, it also provides individual, visual instructions on how to ideally utilize the space inside the box. It’s highly intuitive – and not unlike the well-known computer game Tetris. It may be a simple piece of software in application terms, but it certainly delivers major savings.”
According to initial calculations, an optimally pre-configured and well-utilized set of cardboard boxes can save as much as 50% in superfluous shipment space. This greatly reduces the number of truckloads, allowing commercial customers to save costs not only with regard to oversized cartons and filling material, but also shipping. Furthermore, the solution can provide recommendations as to whether and how an order should be split up to optimize the shipment configuration, making the solution particularly end-consumer friendly.
Markus Voss, CIO and COO at DHL Supply Chain, said, “At DHL Supply Chain, we are continuously working to improve our services and adapt them to the changing needs of our customers. Digital solutions in particular are firmly anchored in our global strategy, helping us to operate more efficiently and sustainably. When you look at the increasing numbers of e-commerce and single-item shipments, it’s easy to recognize that on-demand packaging in combination with the optimized utilization of packing material and transport capacities offers incredible leverage when it comes to saving costs, reducing carbon emissions and improving the customer experience – all at the same time. The main challenges for customers are how to maintain a reasonable spend on packaging and reduce the number of shipments damaged in transit, while optimizing their own transport capacities. OptiCarton can help them master all these challenges.”