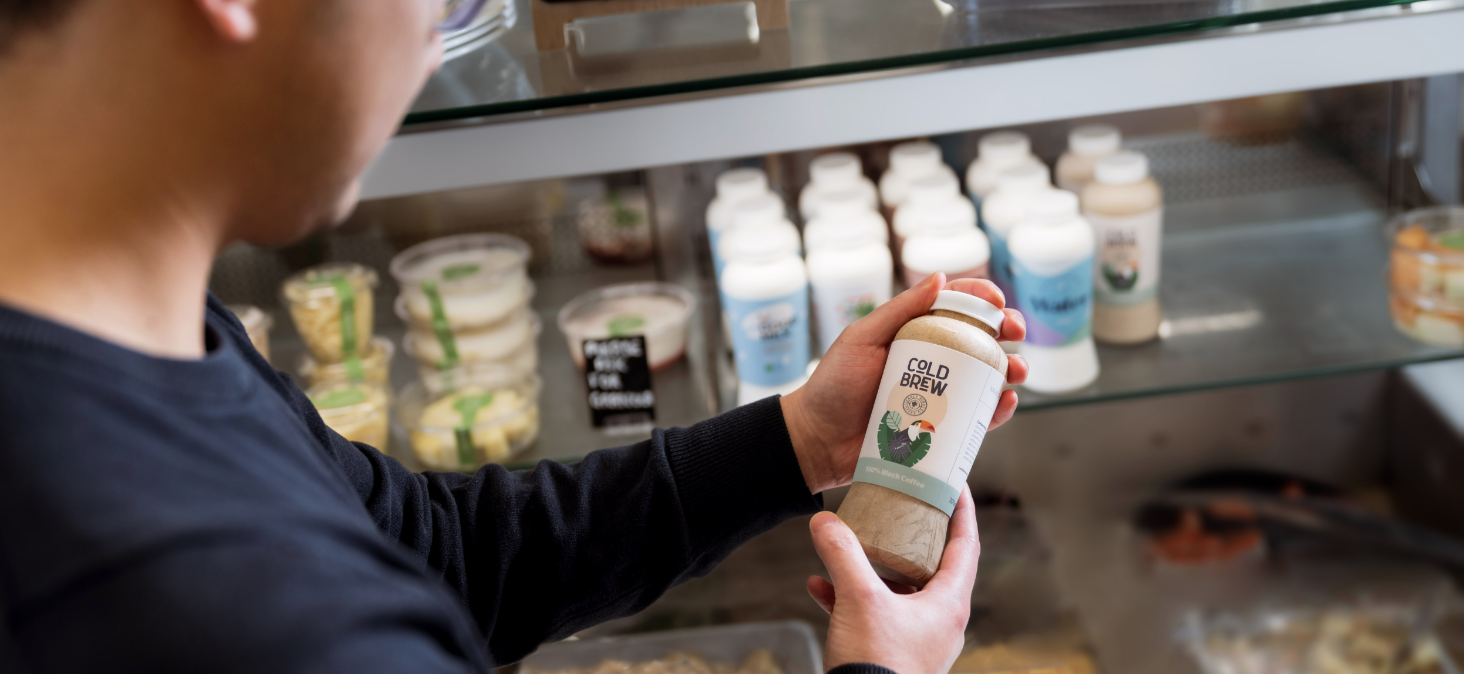
The Bottle Collective is committed to industrializing a recyclable, high-speed, low-cost Dry Molded Fiber bottle process. This technology will be a viable alternative to single-use and commodity plastic bottles and applicable for multiple products and categories. PA’s mechanical engineering, design, automation, and material sciences teams, along with PulPac, have already developed the first functioning prototypes. Multiple leading brand partners joined the Collective to continue developing and scaling fiber bottles by 2025.
Dry Molded Fiber uses renewable pulp and cellulose resources to produce low-cost, high-performance fiber-based packaging. The patented manufacturing process uses less CO2 than plastic and conventional wet molding options. Almost no water is used in manufacturing to create a highly versatile container mold for consumer companies. For instance, fiber bottles could work with water, dairy, non-carbonated soft drinks, adult beverages, detergents, skincare, hair care, etc. Bespoke shape, size, and decoration capability will also allow for the full expression of a brand’s equity.
Tony Perrotta, PulPac Partnership Lead at PA Consulting, said: “We are thrilled to announce the Bottle Collective. Together with leading global consumer brand partners, we can fast-track the development of the world’s first Dry Molded Fiber bottle. This will make the most of our renewable resources while delivering a significant positive impact to reduce today’s single-use plastic pollution. We have the technology. We have a functioning prototype and process. We are now ready to enter the next stage - demonstrating that our Dry Molded Fiber bottles can be produced at the speed, volume, and cost necessary to match the massive scale of this global industry challenge.”
Sanna Fager, Chief Commercial Officer at PulPac, said: “Plastic bottles are the holy grail of plastic replacement. They have an estimated annual production volume of up to 500 billion pieces and are a significant source of plastic pollution worldwide. We proudly share some of our patent-protected advances with PA Consulting, combining Dry Molded Fibers’ forming versatility, broad barrier applicability, and high production efficiency. Backed by strong partnerships across the value chain, we can bring competitive unit cost into the fiber-bottle space, enabling the shift away from today’s single-use plastic. We encourage all brands and relevant industry actors to join this force for sustainable change.”