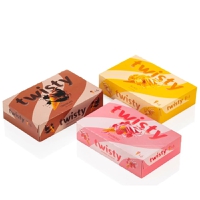
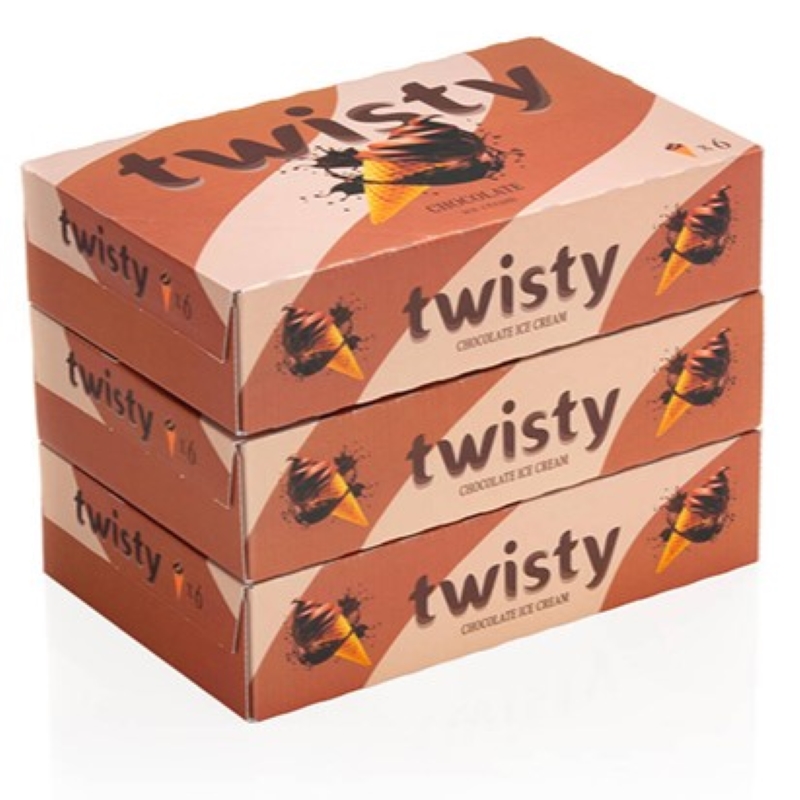
Metsä Board has joined forces with industry leaders to revamp packaging for ice cream cones. The project focused on reimagining the entire value chain, from material production to logistics, resulting in a packaging solution with a “significantly” lower climate impact.
The interdisciplinary team involved in the project includes packaging designers Futupack, Adara Pakkaus and Marvaco. The design, printing and converting experts began by scrutinizing existing frozen food packaging to identify areas for improvement.
According to the detailed calculations conducted by Metsä’s Sustainability Services, which compared the new paperboard materials to traditional white-lined chipboards prevalent in the European market, the 8% lighter weight and the use of fossil-free energy from Metsä’s chemical pulp production resulted in up to a 36% lower climate impact.
“This ice cream packaging project showcased again the power of seamless teamwork. With the careful selection of materials and pushing the traditional boundaries of printing, we were able to combine excellent functionality and resource efficiency,” says Metsä Board’s packaging services director, Ilkka Harju.
“Collaboration was crucial for understanding the requirements and capabilities in the different supply chain stages.”
Material selection
The team aimed to showcase possibilities using carefully selected lightweight, fresh fiber materials and flexographic printing methods, departing from recycled fibers and spot color printing.
Metsä Board opted for its double-coated white-top kraftliner as the top liner while the inside liner and fluting were made of uncoated kraftliner.The goal was to achieve usability and halftone graphics with a reduced climate impact.
Metsä Board opted for its double-coated white-top kraftliner as the top liner, leveraging its lightweight and smooth surface for detailed visual reproduction. The inside liner and fluting were crafted from uncoated kraftliner, offering high strength, ideal for small and lightweight packaging.
Both materials, derived from pure and traceable fresh wood fiber, ensure the packaging is recyclable or compostable, meeting safety standards for food packaging. Furthermore, the company details that having two layers from the same material simplifies production without compromising quality.
User-centric design
Futupack prioritized the user experience by creating an easy-to-open design, eliminating the need for plastic parts or special tools.
Special attention was also given to minimizing ink usage while ensuring the distinct taste variants remained recognizable. Process printing was chosen to enhance efficiency and flexibility by eliminating spot colors.
Meanwhile, packaging manufacturer Adara Pakkaus introduced 64 lpcm expanded color gamut (ECG) co-printing as a suitable method for the corrugated board. The optimally selected kraftliner materials eliminated the washboard effect commonly seen in corrugated boards.
“This high-resolution quality is unusual in such solutions – corrugated post-print typically achieves lower accuracy. ECG benefits co-printing, consolidating designs, reducing waste, plates, energy and press return inks,” says ECG printing specialist Dr. Kai Lankinen, who consulted on the project.
Adara’s Head of Printing, Lari Seppälä, adds: “With our new seven-color press and ECG tools, we were able to reduce ink usage, simplify logistics and make the entire process flexible and cost-efficient.”
“We used a four-color set with upgraded water-based inks adopting Siegwerk’s UniNatureCor Postprint Process Extender, having a 49% bio-renewable content and 26% lower carbon footprint.”