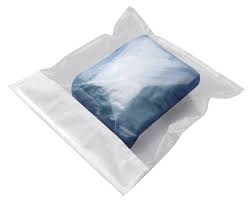
“Sterimed Group has grown significantly in past years. Thanks to the integration of new companies, Sterimed can benefit from the synergy of manufacturing processes, product lines, and R&D teams within the group”, explained Thibaut HYVERNAT President, and CEO of Sterimed. SPS Medical, a member of the Sterimed Group, is a recognized manufacturer of header bags. The addition of SPS Medical expertise in preformed medical packaging accelerated the development of the new Header Bag and its launch to the market.
Where conventional suppliers rely on the functional properties of plastic-to-plastic materials (polyolefins and film), Sterimed seeks an answer to the critical voices for sustainability.
STERIMED is introducing the world’s 1st cellulose-based header bag without a plastic window.
Medical Header Bags are typically used for packing bulky items – from gowns and drape sets to custom procedure kits intended to be sterilized with EO and irradiation. They are recommended by many suppliers, thanks to their relatively easy manufacturing film & polyolefin process.
Header Bags by STERIMED are different. The breathable window is made of Polybond® BGP, Sterimed’s in-house developed, tested, and verified cellulose-based substrate made of 66% bio-based carbon is now replacing the 100% fossil carbon plastic polyolefin of conventional header bags.
The new Polybond® Header Bags offer optimized end-of-life processability. In addition, Polybond® BGP is compostable and biodegradable. The plastic film is mono material; easily recyclable three-layer coextruded, 90 µm Polyethylene.
We can proudly say that Sterimed invented the most sustainable header bags on the market.
No compromise on patients’ safety
Header bags usually offer very high mechanical protection of its content. Polybond® BGP fulfills all the requirements and brings optimized mechanical resistance and flexibility, as confirmed by the extensive testing conducted on the product during its development.
Excellent breathability through an efficient proprietary heat seal layer in grid patterned coating ensures an efficient sterilization process. Sterility maintenance is tested in warm and moist climates and is guaranteed for 5 years.
Tested and validated by healthcare professionals
A critical part of the validation process for Polybond® Header Bags was to conduct extensive trials with end users. Anais Piquet Product Manager for solutions to Medical Device manufacturers at Sterimed, described the focus group user test: “We have created several independent focus groups directly with users in hospitals and got them to test Polybond® Header Bags. Our primary concerns were opening techniques and aseptic presentation. First, blind testing took place, then the same testing after training and with detailed written instructions in OR nurses’ hands.
The results surpassed our expectations. They confirmed that we took the right direction and managed to develop a product that meets the demanding requirements for product characteristics and ease of use."
Choosing the right partner
Healthcare and pharma industries require a stable supply chain more than other industries. Globally, companies are redesigning their supply chains in response to constant disruptions or shortages of products. As a result, it is no longer possible to rely on a single raw material source or supplier to mitigate supply chain disruptions. Shifted responsibilities or unstable prices are those factors that need to eliminate from the supply chain.
Polybond® Header Bags do not depend on a single source of polyolefin material, as is the case with other header bags on the market. Sterimed’s ownership of the overall innovation, industrial, and cost structure ensures accountability and more customer price stability.
Shaping the better future
Sterimed is committed to offering our customers solutions to reach their own environmental impact targets. We will continue to innovate and design products that offer our customers options to choose from.