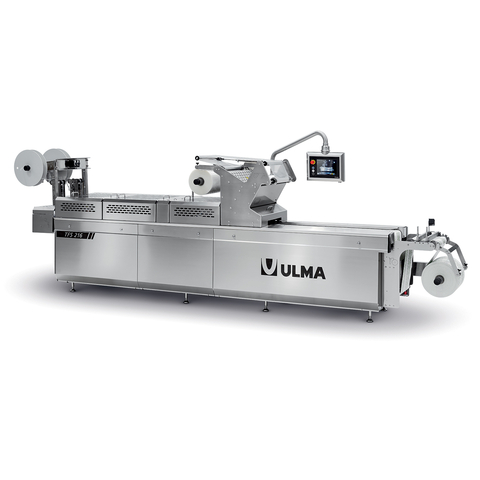
Harpak-ULMA, the industry leader in smart, connected packaging solutions, announced the 2023 North American availability of a new and innovative thermoforming solution that offers more sustainable packaging for fresh food products. The TFS 216 takes ULMA’s pursuit of sustainable packaging solutions a step further by offering a new model of thermoforming machine designed to package fresh products in vacuum skin packs on a flat cardboard base. The TFS 216 uses cardboard roll stock to produce the flat, non-thermoformed base of the packaging – eliminating the need for a plastic tray while generating zero cardboard waste. The cardboard base material can be printed on both sides with product or marketing information and is registered. The use of transport chains, a design common in most conventional thermoformers, requires that part of the original reel width be discarded as scrap. In contrast, the TFS 216 is equipped with an innovative bottom film traction system without chain, so the LeafSkin™ packaging produced retains all of the base material, regardless of its width. LeafSkin™ is one of ULMA’s most unique and sustainable packaging solutions, incorporating both an "easy open" corner to remove the lid, and a "recycling" corner to separate the different materials and make the recycling process easier.
This TFS 216 is part of the ULMAweCare range of solutions, which target more sustainable packaging with a smaller environmental impact. Ken Forziati, Harpak-ULMA’s Thermoformer Product Manager, expects the TFS 216 to enjoy rapid market uptake once the product is available in early 2023. “It really delivers on two key customer concerns” notes Forziati, “First, it’s cost-effective. This approach saves up to 48% in base material costs compared to precut plastic trays. Given the lack of base cardboard scrap, it also saves up to 11% in scrap compared to other conventional thermoformers that employ chain transport systems. Second, it’s a big step forward in sustainability - reducing both plastic and food waste. The TFS 216 uses 100% recyclable cardboard, resulting in up to 80% less plastic compared to traditional skin packaging. It results in a longer shelf life, as well as in a smaller carbon footprint associated both with the transportation of packaging material, and waste management.”