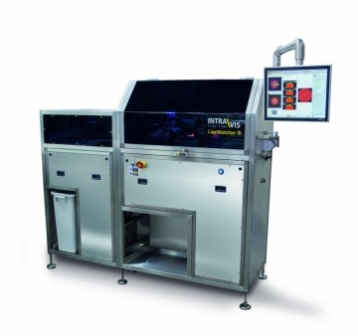
Industry 4.0 continues to inspire our industry. In plastic packaging manufacturing it stands for the fusion of state-of-the-art IT and current production technologies. The goal is to achieve an even higher cost and time efficiency in production as well as maintaining the highest product quality. INTRAVIS supports the latter through the most recent inspection technology including hardware and software updates.
"Closed loop" implemented for the first time
In cooperation with Husky Injection Molding Systems, Netstal-Maschinen AG and Sumitomo (SHI) Demag Plastics Machinery GmbH, INTRAVIS is presenting various solutions for a closed loop link between a vision inspection system and an injection molding machine. This means, all quality-relevant information of newly produced objects captured by the vision inspection system, is first collected in data packets, analyzed and summarized into trends. These analyses and trends are subsequently reported directly to the injection molding machine in data packets using a standard interface, for example based on OPC UA, helping to regulate the manufacturing process. Implementation in the sense of Industry 4.0 means the operator no longer has to intervene as the injection molding machine regulates itself with the help of the analysis results.
INTRAVIS presents various hardware and software solutions for this "closed loop" at multiple partner booths where closures and preforms will be produced live on site. In addition to the CapWatcher® III for the quality control of closures, INTRAVIS introduces a world premiere: For the first time ever INTRAVIS showcases its LayerWatcher® combined with the PreWatcher® III. This allows for the inspection of barrier layers as well as comprehensive 100% quality control of preforms – all in one as an inline solution! The immediate feedback of quality data to the injection molding machine provides an even greater influence on the production process of preforms with barrier layers than before.
Showcasing the Sample-PreWatcher® at the INTRAVIS booth
For the first time, INTRAVIS will also be represented with their own booth at Drinktec. After successful co-exhibitions with several partners at past Drinktec participations, INTRAVIS will have their own booth (Hall A4-344) as a go-to location for their customers. The company based in Aachen, Germany will be presenting its latest generation of the Sample-PreWatcher®. The system designed for comprehensive quality control of preforms and established both as an inline and lab system was again upgraded with multiple innovations.
The most significant upgrade is surely the new lighting concept of the Sample-PreWatcher® providing upmost quality control, especially of opaque preforms. The trend towards increased production of PET packaging and the use of different material and color mixtures is therefore optimally supported.
In addition, the dust suppression is a feature which has resulted in a very positive feedback in several applications at customer sites and is now going into series production. It allows for differentiation between real defects and damages of preforms and acceptable dust particles. False rejects due to errant dust is now a thing of the past.
For the first time, the latest developments for cavity number reading are presented to the public using the Sample-PreWatcher. The proprietary OCRX engine manages to read any cavity fonts immediately after installation. Time consuming training of the software for a font type is no longer necessary. The new OCRX engine is based on INTRAVIS's extensive experience of artificial intelligence in cavity number reading.
INTRAVIS also offers a solution paving the way for industry 4.0 at their own booth. The IntraVisualizer is a powerful analysis software, by being supplied with live measured data of the Sample-PreWatcher. The IntraVisualizer converts the measured results of INTRAVIS systems into easy-to-read graphs. It visualizes different epochs such as shifts, days or even batches. As a special highlight, trend statistics allow for prediction of the Estimated Time to Failure (ETF). This allows an early intervention in the manufacturing process preventing rejects.
Expansion of the product spectrum
In addition to the innovations mentioned above in regards to implemantation of Industry 4.0 as well as improvements to the Sample-PreWatcher®, INTRAVIS is announcing yet more news. For the first time, INTRAVIS will demonstrate their expertise in the field of conveyor technology at Drinktec. At the partner booth of Netstal-Maschinen AG, both a cooling and a transverse conveyor belt for the transportation and cooling of plastic closures are being shown. With the expansion of the product spectrum towards cooling and conveying technology, INTRAVIS is now able to offer their customers even more in-house down-stream equipment. This creates advantages for the customer linking various post injection molding process stations as well as for the service.